3D Printing Patterns for Sand Casting Revolutionizing Traditional Manufacturing
Sand casting is one of the oldest and most widely used methods for producing metal parts. It involves creating a mold from a pattern, pouring molten metal into the mold, and allowing it to solidify into the desired shape. Traditionally, patterns for sand casting have been made from wood, metal, or other materials, but the advent of 3D printing technology has ushered in a new era of pattern production, enhancing the efficiency, accuracy, and flexibility of the casting process.
The Need for Innovation in Sand Casting
Despite its long history, the traditional sand casting process is not without its challenges. Creating patterns can be time-consuming, labor-intensive, and prone to errors. Additionally, modifications to the designs often require the production of entirely new patterns, which can be costly and lead to increased lead times. These issues highlighted the need for a more efficient solution that could streamline the manufacturing process while maintaining the high quality of cast parts.
The Role of 3D Printing
3D printing, also known as additive manufacturing, offers a transformative solution for pattern production in sand casting. The technology allows for the creation of complex geometries that may be difficult, if not impossible, to achieve with traditional methods. By using advanced materials, such as polymer resins and powdered metals, manufacturers can produce highly accurate and detailed patterns quickly and at a lower cost.
One of the primary benefits of 3D printing is its ability to create intricate designs with minimal material waste. Traditional machining methods often remove excess material from a solid block, resulting in significant waste. In contrast, 3D printing adds layer upon layer of material, allowing for efficient use of resources. This not only reduces costs but also aligns with modern sustainability practices, making this method more environmentally friendly.
Customization and Design Flexibility
3d printing patterns for sand casting
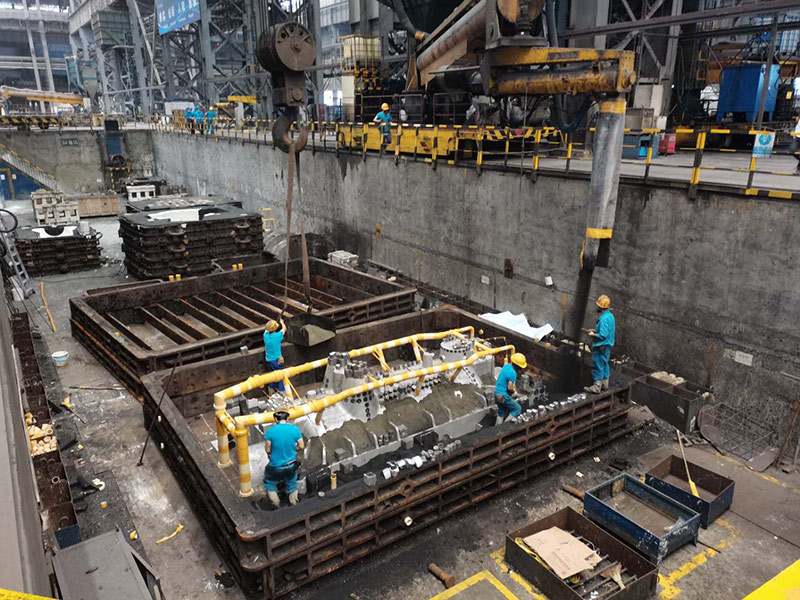
Another significant advantage of 3D printing patterns for sand casting is the ease of customization. Engineers and designers can make rapid adjustments to digital models and reprint patterns almost instantaneously. This flexibility is especially valuable in industries that require rapid prototyping and short production runs. It facilitates a more iterative design process, allowing for improvements and refinements based on immediate feedback and testing.
In addition to improving turnaround times, 3D printing enables the production of lighter and more complex patterns. By leveraging advanced design software and additive manufacturing techniques, engineers can optimize the patterns for better thermal performance and enhanced mechanical properties. This can lead to better quality castings with fewer defects, reducing the need for secondary machining operations and further lowering production costs.
Challenges and Considerations
Despite its numerous advantages, implementing 3D printing in sand casting is not without challenges. One of the primary hurdles is the need for specialized equipment and materials, which can entail a significant initial investment. Additionally, while the technology has advanced rapidly, there may still be concerns about the long-term durability of 3D-printed patterns, especially under the high temperatures encountered during the casting process.
Moreover, collaboration between design engineers and 3D printing specialists is crucial to ensure that patterns are optimized for both printing and the casting process. A thorough understanding of the characteristics of the materials used in 3D printing, as well as the specific requirements of the sand casting process, is essential for achieving successful outcomes.
Conclusion
The integration of 3D printing into sand casting represents a significant advancement in manufacturing technology. With its ability to produce intricate, lightweight, and customized patterns quickly and efficiently, 3D printing is poised to revolutionize the traditional casting process. While challenges remain, the benefits of this innovative approach are clear. As the technology continues to evolve, it will undoubtedly play a pivotal role in transforming the future of sand casting and other manufacturing processes. Embracing these advancements will not only enhance productivity but also pave the way for a new era of design creativity and sustainability in manufacturing.
Post time:окт. . 18, 2024 03:08
Next:pagpapalaglag ng buhangin