Revolutionizing Casting The Impact of 3D Printed Sand Casting
In recent years, the manufacturing landscape has evolved dramatically with the introduction of innovative technologies that enhance production efficiency and design flexibility. Among these breakthroughs, 3D printed sand casting has emerged as a transformative method in the foundry industry. Utilizing additive manufacturing techniques, this method not only streamlines the casting process but also offers numerous advantages over traditional casting methods.
What is 3D Printed Sand Casting?
3D printed sand casting involves creating molds for metal casting through the use of 3D printing technology. Unlike traditional sand casting, which requires patterns to be carved from wood or metal, 3D printed molds are made directly from digital models. This method employs a binder jetting process, where sand is selectively bonded together using a liquid binder according to the specified design. The result is a precise and complex mold that can be produced rapidly, reducing lead times significantly.
Advantages of 3D Printed Sand Casting
1. Design Flexibility One of the most significant advantages of 3D printed sand casting is the freedom it offers designers. Traditional casting methods often impose constraints due to the limitations of pattern-making and mold creation. However, 3D printing allows for intricate geometries and complex internal features that would be difficult or impossible to achieve with conventional methods. This flexibility not only fosters creativity but also enables the production of lightweight components that maintain structural integrity.
2. Rapid Prototyping The speed at which 3D printed molds can be produced is a game-changer for industries that require quick turnarounds. Rapid prototyping facilitates faster design iterations, allowing engineers to test and refine their concepts without the lengthy wait times associated with traditional mold production. This agility is especially beneficial for industries such as automotive and aerospace, where time-to-market is critical.
3d printed sand casting
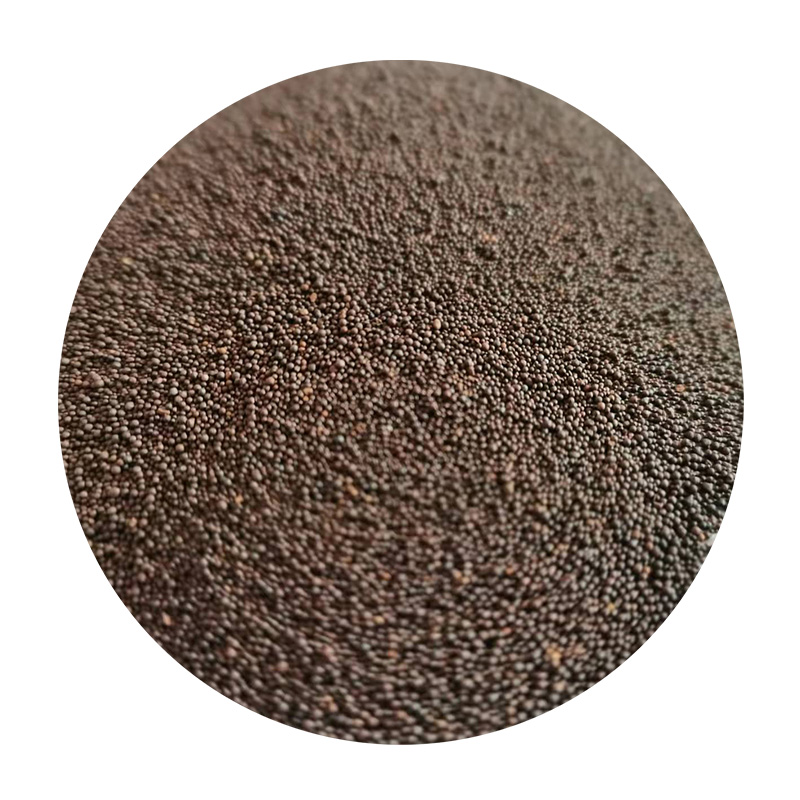
3. Cost-Effectiveness Although the initial investment in 3D printing technology may be substantial, the long-term cost savings can be significant. 3D printed molds reduce waste, as material is only used where necessary, and they eliminate the need for expensive and time-consuming tooling. Moreover, the ability to produce small batches economically makes 3D printed sand casting an attractive option for custom manufacturing and low-volume production runs.
4. Environmental Impact The traditional foundry process often generates a considerable amount of waste through metal removal and the creation of patterns. In contrast, 3D printed sand casting uses only the material required for the mold, minimizing waste and promoting sustainability. Additionally, the reduced energy consumption associated with 3D printing compared to traditional manufacturing processes contributes to a lower carbon footprint.
Applications in Various Industries
The versatility of 3D printed sand casting has led to its adoption across a variety of industries. In the automotive sector, manufacturers use this method to create complex engine components, reducing weight and improving fuel efficiency. Aerospace applications benefit from the ability to produce lightweight and highly engineered parts that can withstand extreme conditions. Additionally, the medical field has embraced 3D printed sand casting to produce customized implants and prosthetics tailored to individual patients.
Future Prospects
As the technology continues to advance, the future of 3D printed sand casting looks promising. Innovations in material science and printing techniques are likely to expand the range of metals and alloys that can be used in this process. Furthermore, the integration of artificial intelligence and machine learning can enhance design optimization and predictive maintenance, further streamlining the manufacturing workflow.
In conclusion, 3D printed sand casting represents a significant evolution in the casting industry, offering a blend of flexibility, efficiency, and sustainability. As more industries recognize its benefits, this technology is poised to become a cornerstone of modern manufacturing. The shift towards additive manufacturing methodologies not only enhances production capabilities but also paves the way for a more sustainable future in manufacturing. Embracing these innovations will enable industries to not only meet current demands but also adapt to the evolving landscape of technology and consumer needs.
Post time:дек. . 21, 2024 08:51
Next:wet sanding ceramics