Why is Sand Casting Used?
Sand casting is one of the most traditional and widely used metal casting processes in the manufacturing industry. It involves the use of sand as the primary mold material for shaping the liquid metal that is poured into it. This method has been a favored choice for many manufacturers for several reasons, each contributing to its enduring popularity in various industrial applications.
Cost-Effectiveness
One of the foremost reasons why sand casting is widely used is its cost-effectiveness. The materials required for sand casting—primarily sand, which is abundant and inexpensive—make it an economically viable option for producing metal parts. Unlike other casting methods that may require expensive equipment and materials, sand casting can be executed with relatively low initial investment. The reusable nature of sand also adds to the cost efficiency, allowing manufacturers to recycle used sand in multiple casting cycles.
Versatility
Sand casting is exceptionally versatile, allowing the production of a wide range of complex shapes and sizes. This flexibility enables manufacturers to create anything from small, intricate parts to large components, which makes it suitable for various industries, including automotive, aerospace, and machinery. Additionally, sand molds can be easily modified for different designs, facilitating the rapid prototyping of components and offering manufacturers the ability to respond swiftly to changing market demands.
Scalability
Another significant advantage of sand casting is its scalability. The process can be employed for both small-scale production runs and large-volume manufacturing with equal efficiency. For small projects, sand casting can be performed manually using simple tools and equipment. In contrast, larger production runs can take advantage of automated processes, including automated sand molding machines, reducing labor costs and increasing productivity. As a result, companies can scale their production up or down as needed without facing substantial overheads or resource constraints.
Excellent Surface Finish and Detail
why is sand casting used
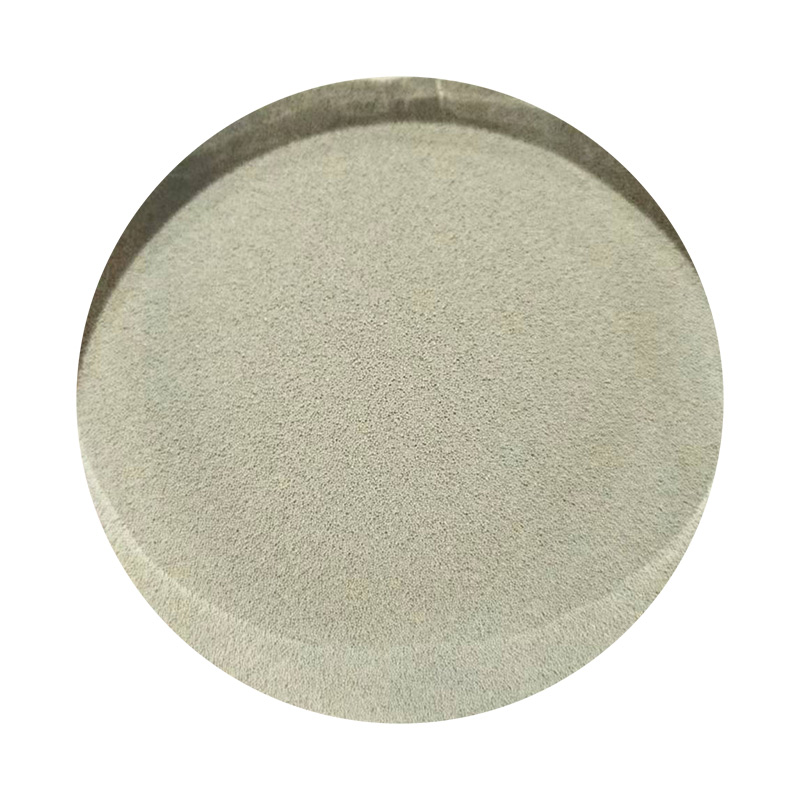
While sand casting traditionally had a reputation for producing rough surface finishes, advancements in techniques have greatly improved the quality of the final product. Modern sand casting allows for finer control over the surface finish and detail of the castings. Additionally, post-casting processes such as machining or polishing can enhance the surface quality further, making it suitable for applications that require tight tolerances and aesthetically pleasing finishes.
Ideal for Complex Geometries
Sand casting is particularly advantageous for creating parts with complex geometries that would be difficult or impossible to achieve using other methods. The ability to produce intricate designs and details without the need for extensive tooling makes sand casting a go-to option for many engineers and designers. Whether creating shapes with deep cores, thin walls, or unusual contours, sand casting provides the flexibility required to meet intricate design specifications.
Good Heat Resistance
Sand molds exhibit excellent heat resistance, allowing them to withstand the high temperatures encountered during the metal pouring process. This property is particularly vital when working with metals that have high melting points, such as aluminum and copper. The ability of sand molds to absorb heat while providing structural integrity prevents defects in the final product, making sand casting a reliable choice for fabricating high-performance components.
Environmentally Friendly Properties
In recent years, the environmental impact of manufacturing processes has come under scrutiny. Sand casting is considered a more environmentally friendly option compared to other methods due to its ability to use natural, recyclable materials. Modern trends also emphasize the recycling of sand, minimizing waste. Additionally, many foundries are adopting greener practices, including reducing emissions and improving energy efficiency, which aligns sand casting with sustainable manufacturing practices.
Conclusion
In summary, sand casting remains one of the most widely used metal casting processes due to its cost-effectiveness, versatility, scalability, and ability to produce intricate designs and geometries. As industries continue to evolve, sand casting's inherent advantages position it as a resilient and reliable method for crafting quality metal parts across various sectors. With its longstanding history and a promising future, sand casting continues to play a pivotal role in the manufacturing landscape.
Post time:Ліст . 25, 2024 09:50
Next:sand casting supplier