Types of Sand in Foundry
In the foundry industry, sand plays a crucial role as a primary molding material for casting processes. The type of sand selected often determines the quality of the final product, the efficiency of the casting process, and the characteristics of the finished mold. Understanding the various types of sand used in foundries is essential for optimizing both performance and cost-effectiveness in metal casting operations.
Types of Sand in Foundry
Another popular choice is olivine sand, which contains magnesium and iron silicate. This type of sand is known for its superior thermal properties and lower expansion rate compared to silica sand, making it ideal for casting processes that involve high temperatures. Olivine sand is also less prone to metal penetration, contributing to smoother surface finishes on the cast products.
types of sand in foundry
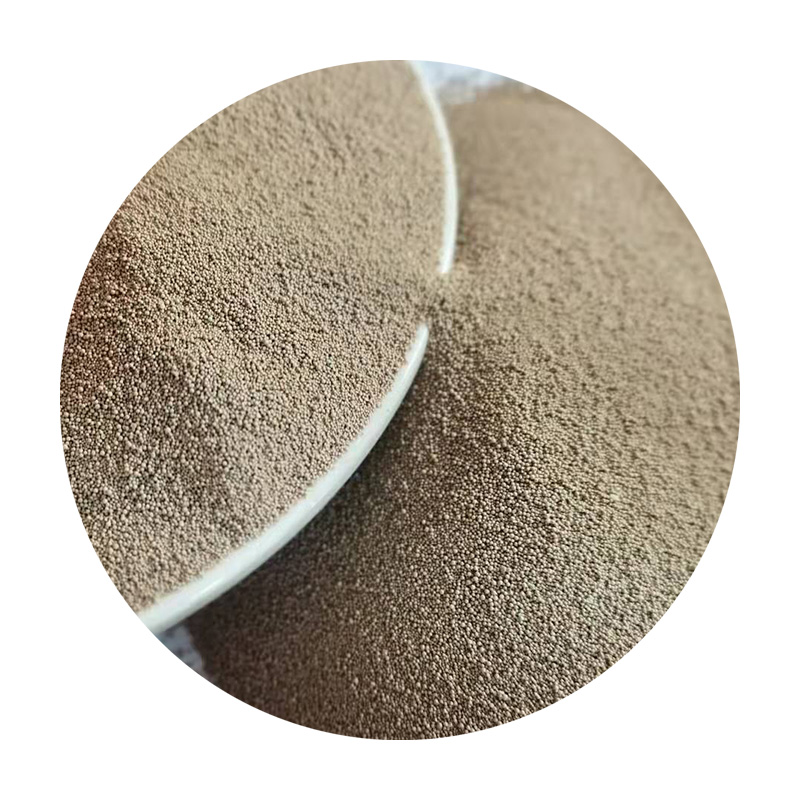
Clay bonded sand is another category, often referred to as green sand. It is a mixture of silica sand, clay, and water, forming a mold that retains its shape even when heated. The clay acts as a binding agent, providing strength and workability, while the water helps to maintain moisture levels within the mold. This type of sand is widely used due to its cost-effectiveness and ability to produce intricate designs.
Resin-bonded sand is an advanced option that utilizes resin as a binding agent, providing higher strength and rigidity compared to traditional molds. This type of sand is often used for precision casting applications, as it can produce finer details and smoother finishes. Additionally, the use of resin sand allows for quicker drying times and reduced environmental impacts, making it an attractive option for modern foundries.
Lastly, there are special sands such as zircon sand and chromite sand, which offer unique properties for specific applications. Zircon sand is known for its high refractoriness and resistance to abrasion, while chromite sand provides excellent thermal conductivity and is ideal for steel casting.
By carefully selecting the type of sand used in foundry operations, manufacturers can enhance the performance, quality, and efficiency of their casting processes, ultimately leading to superior final products.
Post time:Каст . 11, 2024 17:36
Next:Innovations and Techniques in Sand Casting for Modern Foundry Applications