Types of Sand Casting Processes
Sand casting is one of the oldest and most versatile metal casting processes, widely used in various industries due to its flexibility and cost-effectiveness. This process involves creating a mold from a mixture of sand and a binding agent, pouring molten metal into the mold, and allowing it to solidify. The ability to produce complex shapes and large parts makes sand casting a popular choice for manufacturing. There are several types of sand casting processes, each with unique characteristics and applications.
1. Green Sand Casting
Green sand casting is the most common type of sand casting process. It uses a mixture of sand, clay, and water to create the mold. The term green refers to the moisture content in the mold rather than the color. The mold is typically created by compacting the sand mixture around a pattern made from metal or wood. Once the mold is ready, molten metal is poured in, and after cooling, the sand is broken away to reveal the finished product. This method is ideal for producing both ferrous and non-ferrous metals and is widely used in the production of automotive components and various industrial parts.
Shell mold casting involves using a thin layer of sand that is bonded with a thermosetting resin, creating a mold that is both highly durable and capable of producing intricate designs. In this process, a heated pattern is coated with the sand-resin mixture, allowing it to adhere and bond to form a shell. Once the shell is formed, the molds are fused together to create the complete mold cavity. The advantages of shell mold casting include improved dimensional accuracy and a smooth surface finish. This technique is often used for producing parts with complex geometries, such as small gears, housings, and brackets.
3. Investment Casting
types of sand casting process
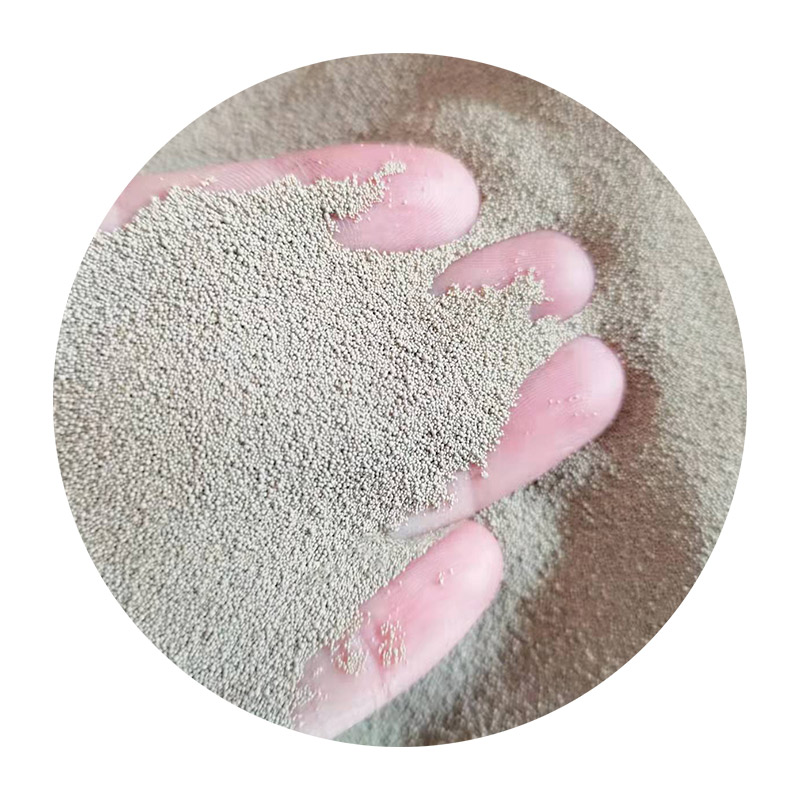
Investment casting, also known as lost-wax casting, is a precision casting process where a wax pattern is coated with a ceramic shell. Once the shell is hardened, the wax is melted away, leaving a hollow cavity into which molten metal is poured. This technique offers a high degree of accuracy, making it suitable for producing complex and intricate parts, usually in smaller quantities. While it is not strictly a sand casting process, investment casting sometimes uses sand molds for certain applications. It is widely used in industries such as aerospace, medical, and jewelry manufacturing due to its ability to produce high-quality components with excellent surface finishes.
4. Co2 Sand Casting
CO2 sand casting uses a mixture of sand and sodium silicate as a binder. Carbon dioxide is passed through the mixture, causing a chemical reaction that hardens the sand into a solid mold. This process is advantageous because it eliminates moisture and improves the hardness of the mold, reducing the risk of defects in the cast part. CO2 sand casting is often employed for producing large and heavy components, including machinery parts and industrial components. Its rapid setting time also makes it a preferred choice for high-volume production.
5. Lost Foam Casting
Lost foam casting is a method that uses a foam pattern, typically made from polystyrene, which is coated with a sand mixture. When molten metal is poured into the mold, the foam evaporates, leaving a void for the metal to fill. This process allows for the creation of complex shapes that are often difficult to achieve with other sand casting techniques. Lost foam casting is particularly suited for producing large components with intricate designs and is used in industries such as automotive engineering and pipe fittings.
Conclusion
In summary, sand casting is a versatile manufacturing process with various types catering to different needs and requirements. Green sand, shell mold, investment, CO2 sand, and lost foam casting each have unique advantages that make them suitable for specific applications. By understanding these processes, manufacturers can select the most appropriate method for their production requirements, ensuring quality and efficiency in their casting projects. Whether for intricate designs or large components, sand casting continues to be a vital process in the realm of metal fabrication.
Post time:Ліст . 29, 2024 21:22
Next:Exploring Various Alloys Used in Sand Casting Processes and Their Applications