Understanding Sand Casting and Its Applications with Resin
Sand casting is one of the oldest and most versatile methods of metal casting, and it continues to play a crucial role in various industries today. This traditional technique is particularly noteworthy due to its ability to produce complex shapes and sizes with relatively low costs. In recent years, the integration of resin in sand casting has further expanded its capabilities, enhancing the quality and precision of castings.
The Basics of Sand Casting
Sand casting, also known as sand mold casting, involves creating a mold from sand, where molten metal is poured to create a part. The process begins with the preparation of a mold, which typically consists of two halves. This is done using a pattern that reflects the final shape of the desired object. The pattern can be made from various materials including metal, wood, or plastic.
The sand used is often mixed with a binding agent, which helps in maintaining the shape of the mold during the casting process. Silica sand is the most common type due to its high melting point and excellent properties, allowing it to endure the molten metal’s heat.
The Role of Resin in Sand Casting
Incorporating resin into the sand casting process can significantly improve the quality of the molds. Resin-bonded sand provides several advantages over traditional sand mixtures. First, resin sands create stronger molds and cores that can withstand the high temperatures and pressures of molten metal. This leads to improved surface finishes and reduced defects in the final castings.
One of the notable types of resin used is phenolic urethane resin, which when mixed with sand forms a very durable mold. This resin can cure quickly when heat is applied, allowing for shorter production times and preventing the sand from collapsing under the weight of the molten metal.
Additionally, resin sand can be reused multiple times, making it a cost-effective option in manufacturing. The ability to regenerate and recycle the sand with resin not only reduces material costs but also minimizes waste, contributing to greener manufacturing practices.
Advantages of Sand Casting with Resin
sanding casting resin
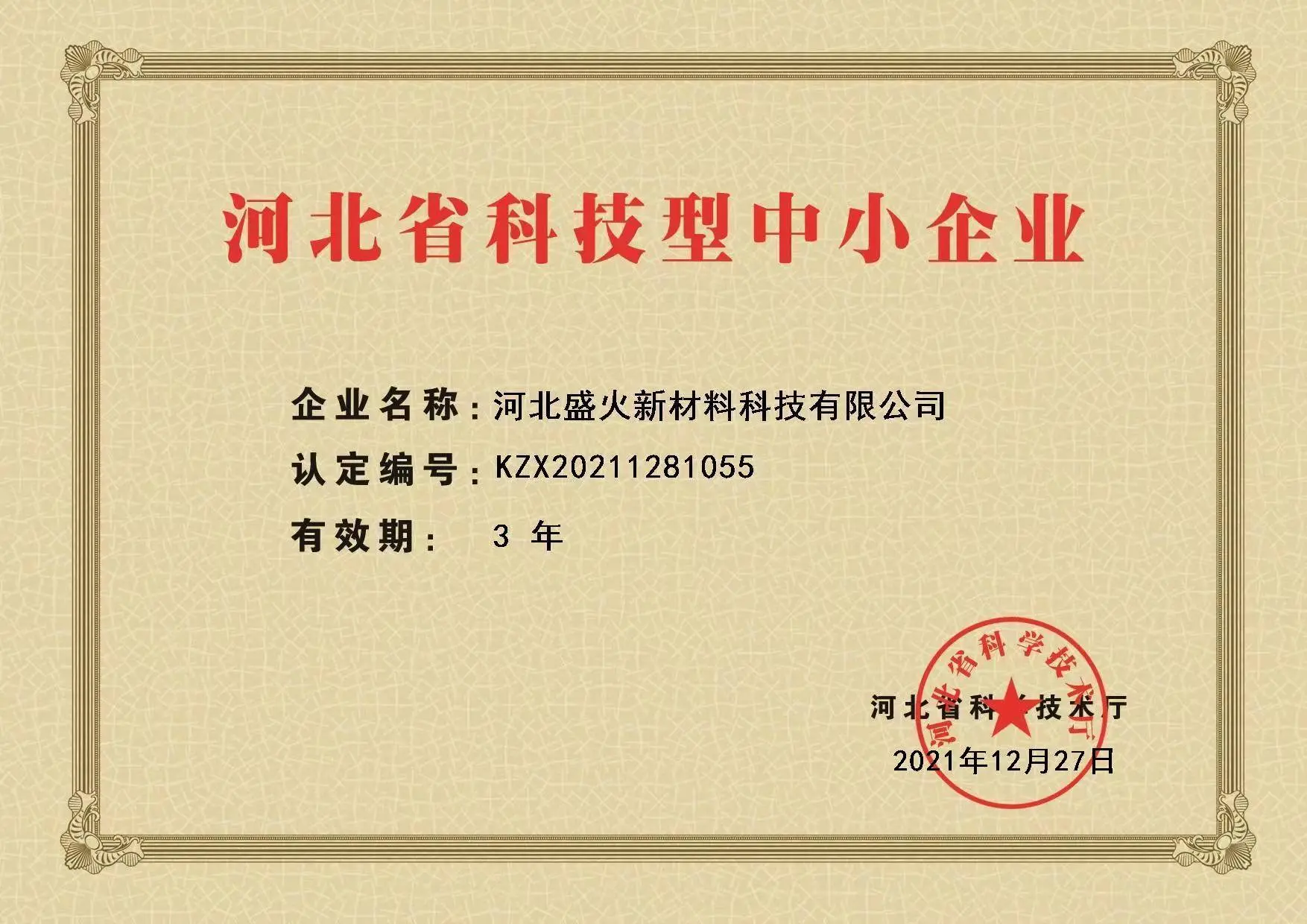
1. Precision and Detail The strength of resin-bound sands allows for finer, more intricate details in castings. This is particularly beneficial in industries such as automotive or aerospace, where precision is paramount.
2. Reduced Defects The superior thermal stability of resin allows for the casting of parts without the common defects seen in traditional sand casting, such as sand blow or pinholes. This translates to higher quality products with fewer rejections.
3. Customization The flexibility of the resin-sand mixtures allows for customization in properties to suit specific applications. Depending on the type of resin, manufacturers can adjust the sand mixture to achieve the desired mold characteristics.
4. Faster Production The quick curing time of resin-bonded sands can significantly reduce the time needed to prepare molds, thus accelerating production rates.
5. Improved Surface Finish Castings produced from resin molds generally exhibit a smoother surface finish, which can reduce the subsequent machining processes needed, saving time and money.
Applications of Sand Casting with Resin
Sand casting with resin is widely used across various industries. In aerospace, it’s employed to produce complex frame components, brackets, and structural parts that require lightweight yet robust features. The automotive industry benefits from this technology by producing intricate engine components and parts with high integrity.
Moreover, the art and sculpture sector harnesses resin sand casting for creating detailed artistic pieces. The ability to capture fine details allows artists to produce replicas or unique pieces that are durable and aesthetically pleasing.
Conclusion
The evolution of sand casting with the integration of resin technology represents a significant advancement in manufacturing processes. By enhancing the strength, precision, and quality of molds, resin not only meets the growing demands of modern industries but also paves the way for innovative applications in various fields. As technology continues to progress, the potential of resin in sand casting is bound to expand further, leading to new opportunities and improved practices in metalworking.
Post time:Ліст . 12, 2024 02:06
Next:foundry sand contamination