Sand for Casting The Essential Material in Metalworking
Sand casting is one of the oldest and most versatile processes in the field of metalworking. This method has been used for centuries to produce intricate metal parts and is favored for its relatively low cost and the ability to create complex shapes. At the heart of this process lies sand, which serves as the primary material for the mold. This article explores the significance, types, properties, and advantages of using sand in the casting process.
The Significance of Sand in Casting
Sand plays a crucial role in the casting process as it forms the mold into which molten metal is poured. This material is selected for its properties that facilitate easy molding and reliable performance under heat. The unique characteristics of sand make it an ideal choice for forming the negative impressions of the desired objects. Proper preparation and compaction of sand can yield molds that accurately replicate the intricate designs required in modern manufacturing.
Types of Sand Used in Casting
There are several types of sand used in casting, each with its unique properties and applications
1. Green Sand This is the most commonly used type in sand casting. It is a mixture of sand, clay, and moisture, which gives it a natural green color. Green sand is preferred for its ability to retain moisture, allowing it to be packed tightly around patterns.
2. Dry Sand Dry sand casting involves the use of sand that has been dried to remove moisture. This type of sand is often used for making more complex molds that require greater stability and strength.
3. Synthetic Sand Composed of specially prepared materials, synthetic sand offers uniform particle sizes and enhanced characteristics compared to natural sand. Its higher strength allows for better details and finer mold finishes.
4. Resin Sand This type of sand is mixed with a resin binder that hardens when exposed to heat. Resin sand offers high accuracy and durability, making it suitable for producing intricate designs and finer details in parts.
Properties of Casting Sand
The effectiveness of sand as a mold material largely depends on its physical and thermal properties. Key properties include
sand for casting
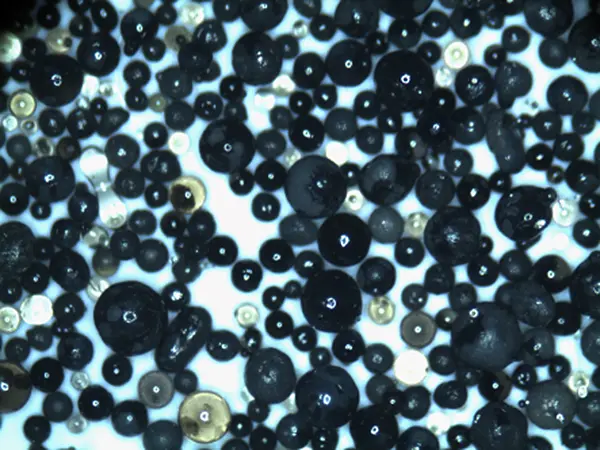
- Grain Size The size of individual sand grains affects the fineness of the mold surface. Finer grains can produce smoother finishes but may be more difficult to compact effectively.
- Refractoriness This refers to the ability of sand to withstand high temperatures without collapsing or losing its shape. High refractoriness is crucial as it enables the sand to maintain its structural integrity when molten metal is poured into the mold.
- Permeability Permeable sands allow gases generated during the casting process to escape, preventing defects such as blowholes in the finished component. A good balance of permeability is critical for producing high-quality casts.
- Thermal Conductivity This property influences how quickly heat is transferred from the molten metal to the sand. Adequate thermal conductivity can reduce the risks of defects caused by rapid cooling.
Advantages of Using Sand for Casting
The use of sand for casting offers numerous advantages
- Cost-Effectiveness Sand is widely available and inexpensive compared to other mold materials. This makes it a popular choice for both small-scale operations and large manufacturing plants.
- Reusability Sands can often be reclaimed and reused several times, especially when proper procedures are followed to clean and restore their properties.
- Versatility Sand casting can accommodate a wide range of metals, including aluminum, iron, and bronze, making it suitable for various applications across industries.
- Complex Shapes With the proper techniques, sand casting can produce complex geometries that would be difficult or impossible to achieve with other methods.
In conclusion, sand remains a cornerstone of the casting industry, providing the critical foundation for creating high-quality metal parts. Its versatility, affordability, and ease of use ensure that sand casting will continue to be a preferred method in manufacturing for years to come. Understanding the various types of sand, their properties, and the advantages they offer is vital for any metalworking professional aiming to optimize their casting processes.
Post time:Каст . 18, 2024 11:55
Next:Exploring the Benefits and Applications of Cerabeads Sand in Modern Industries