Sand Casting Metal A Timeless Manufacturing Technique
Sand casting is one of the oldest and most versatile metal casting processes in manufacturing. It dates back to ancient civilizations, where artisans used sand to create molds for metal objects. Today, it continues to be a popular method due to its simplicity, cost-effectiveness, and ability to produce intricate designs.
The process begins with creating a mold, which consists of two halves known as the cope and the drag. The cope is the upper part of the mold, while the drag is the lower part. Sand, typically mixed with a binding agent like clay, is packed around a pattern, which represents the desired final shape of the metal object. This pattern can be made of various materials, including metal, plastic, or wood, depending on the size and complexity of the desired casting.
Sand Casting Metal A Timeless Manufacturing Technique
With the metal molten and the mold prepared, the liquid metal is poured into the cavity. This step requires precision, as the temperature and pouring technique can significantly affect the final product’s quality. Once the mold is filled, it is left to cool, allowing the metal to solidify and take the shape of the cavity. The cooling time can vary depending on the material and size of the casting, but care must be taken to ensure even cooling to prevent defects.
sand cast metal
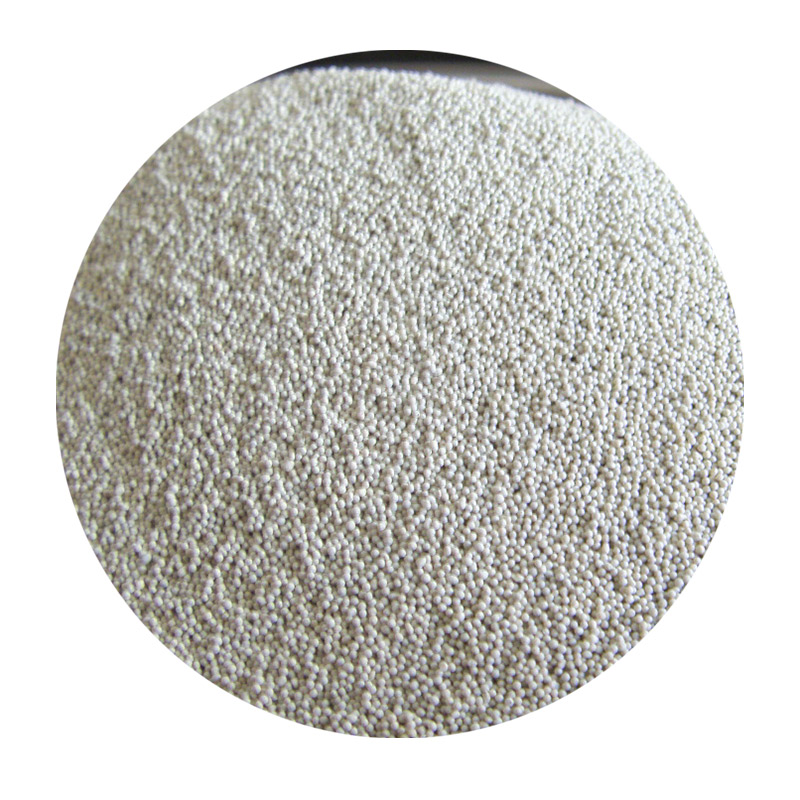
After the metal has solidified, the next step is breaking away the sand mold, leaving behind the finished metal casting. This process is often referred to as shakeout. Post-casting, the object may require additional finishing processes such as grinding, machining, or surface treatment to achieve the desired specifications.
One of the main advantages of sand casting is its ability to produce large and complex parts in a variety of sizes. It can accommodate intricate designs and features that might be challenging for other casting methods. Additionally, sand casting is highly adaptable, allowing for modifications in design without significant changes to the manufacturing process.
Moreover, sand casting is cost-effective, especially for low to medium production volumes. The materials used in making the molds are relatively inexpensive, and the process allows for recycling of sand, making it environmentally friendly. Another key benefit is that it requires minimal tooling, which reduces lead times and costs associated with setting up production.
In conclusion, sand casting metal remains a fundamental and efficient method in the manufacturing sector. Its rich history of craftsmanship, combined with modern technology, ensures that this process will continue to evolve and meet the needs of various industries, from automotive to aerospace. As industries seek to balance quality, efficiency, and sustainability, sand casting will undoubtedly play a vital role in the future of metal manufacturing.
Post time:Каст . 05, 2024 01:02
Next:Innovative Sand Adhesive for Ultimate Bonding Performance and Durability