The Uses of Sand Casting A Versatile Manufacturing Process
Sand casting is one of the oldest and most widely used metal casting processes in the manufacturing industry. Characterized by its simplicity and versatility, it is a highly effective method for producing metal components with complex shapes and geometries. This article will delve into the uses of sand casting, exploring its applications across various industries, the benefits it offers, and its significance in modern manufacturing.
Overview of Sand Casting
At its core, sand casting involves creating a mold from sand, into which molten metal is poured to form a desired shape upon solidification. The process generally begins with the creation of a pattern, which is a replica of the final product. This pattern is then pressed into sand mixed with a binding agent to create a mold cavity. Once the mold is prepared, it is ready to receive molten metal, which after cooling and solidifying, is removed and finished to meet specific requirements.
Major Applications
1. Automotive Industry Sand casting plays a crucial role in the automotive sector, where it is used to produce engine blocks, cylinder heads, and transmission cases. The ability to create complex shapes and sizes makes sand casting an ideal choice for making large, intricate components that are essential for vehicle performance.
2. Aerospace In the aerospace industry, sand casting is employed to manufacture parts that require high strength and low weight. Components such as brackets, housings, and various engine parts benefit from the sand casting process, which allows for the production of lightweight yet durable materials that can withstand extreme operational conditions.
3. Marine Applications The marine sector utilizes sand casting for components that are exposed to corrosive environments, such as pump housings, valves, and fittings. The ability to cast these parts in various metals, including aluminum and brass, enhances their resistance to corrosion and wear.
4. Art and Sculpture Beyond industrial applications, sand casting is also embraced by artists and sculptors. The process allows for the creation of intricate sculptures and artistic pieces, providing artists the freedom to express their creativity in metal. The artistic application of sand casting frequently results in unique, custom designs that cannot be achieved through other manufacturing methods.
sand casting uses
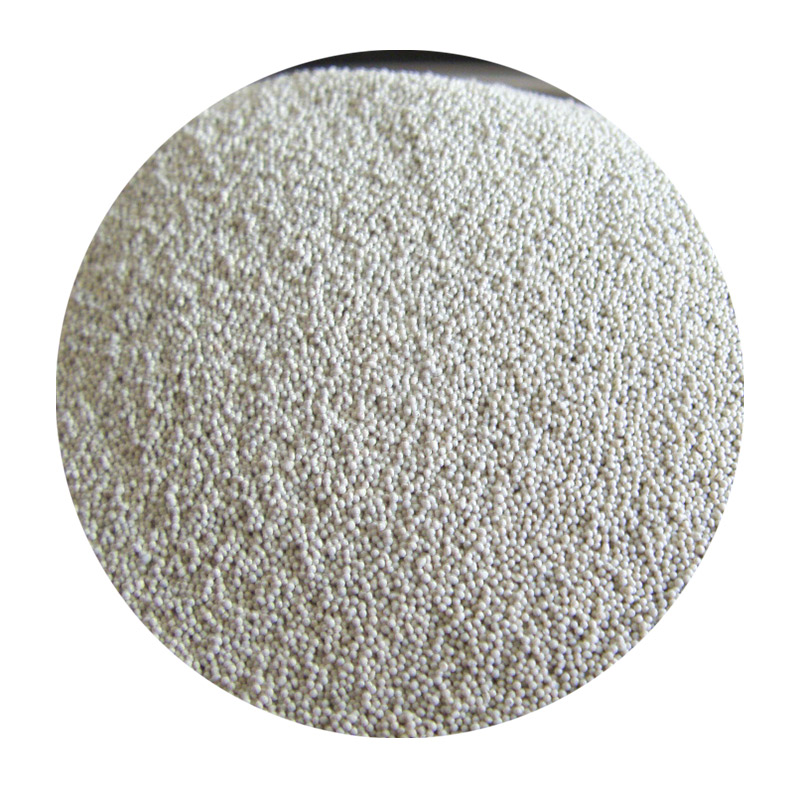
5. Construction In construction, sand casting is utilized for various architectural elements, such as decorative facades, columns, and structural components. The ability to create detailed designs helps enhance the aesthetic appeal of buildings while ensuring structural integrity.
Benefits of Sand Casting
The advantages of sand casting contribute to its enduring popularity in the manufacturing field
- Cost-Effectiveness Sand casting is generally more cost-effective than other casting methods, especially for low to medium production volumes. The materials and equipment required are relatively inexpensive, making it accessible for various businesses.
- Flexibility Sand casting offers a high degree of design flexibility. Since molds can be created to match virtually any shape, manufacturers can produce diverse products without the constraints faced by other casting methods.
- Large Size Capability Sand casting is particularly suited for producing large components. The molds can be easily scaled to accommodate substantial objects, such as engine blocks or large sculptures.
- Material Versatility This casting method can accommodate a wide range of metals, including ferrous and non-ferrous alloys. This versatility allows manufacturers to choose materials based on specific requirements, such as strength, weight, and corrosion resistance.
Conclusion
Sand casting remains a vital technique in the world of manufacturing, thanks to its many applications across industries. From automotive to aerospace, marine to artistic creations, the process demonstrates unmatched versatility and practicality. As technology evolves, sand casting continues to adapt, integrating innovations that enhance efficiency and precision. Therefore, it is clear that sand casting will remain a cornerstone of manufacturing for the foreseeable future, proving its relevance and importance in an ever-changing industrial landscape.
Post time:снеж . 13, 2024 05:31
Next:sanding 3d resin prints