Sand Casting Technique A Comprehensive Overview
Sand casting is one of the oldest and most widely used metal casting processes. This versatile technique allows manufacturers to create complex shapes and intricate designs that are often required in various industries, including automotive, aerospace, and heavy machinery. In this article, we will explore the fundamentals of sand casting, its process, applications, advantages, and limitations.
Understanding Sand Casting
At its core, sand casting involves creating a mold using sand into which molten metal is poured to create a desired object. This process typically involves several stages pattern making, mold preparation, pouring, and finishing.
1. Pattern Making The first step in sand casting is creating a pattern, which is a replica of the final product. Patterns can be made from various materials, including wood, metal, or plastic, and are designed to account for shrinkage that occurs as the metal cools. Depending on the complexity of the shape, patterns can be either solid or split into multiple pieces for easier removal from the mold.
2. Mold Preparation Once the pattern is ready, sand is mixed with a binding agent, usually clay, to form the mold. This mixture, known as green sand, is then compacted around the pattern to create a mold cavity. The mold is divided into two halves, allowing for the pattern to be easily removed after the sand has been compacted. After removing the pattern, the two halves are assembled, and any necessary cores (internal structures) are inserted.
3. Pouring After the mold is prepared, molten metal is poured into the cavity. The temperature of the molten metal typically ranges between 1,300°C and 1,500°C (2,372°F and 2,732°F), depending on the specific alloy. The pouring process must be carefully controlled to avoid defects such as gas entrapment or uneven filling.
4. Cooling and Finishing Once the molten metal fills the mold, it begins to cool and solidify. After a sufficient cooling period, the mold can be broken apart, and the cast part is removed. Post-casting processes such as trimming, sanding, and surface treatments may be applied to achieve the desired finish and dimensional accuracy.
Applications of Sand Casting
Sand casting is used to produce a vast range of metal components, from small parts to large machinery
. It is commonly employed in industries such assand casting technique
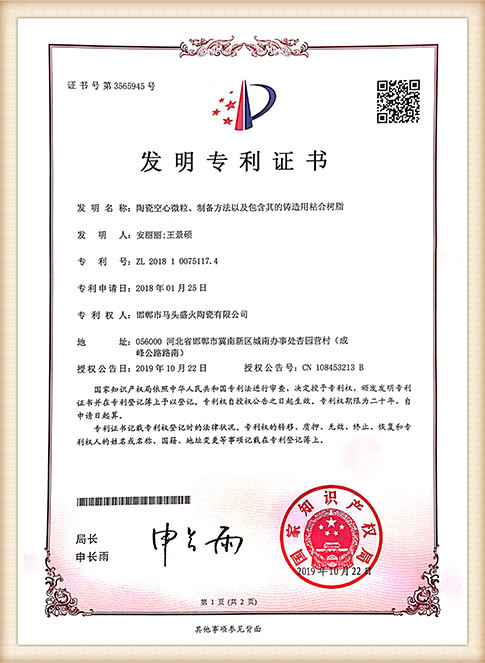
- Automotive Components like engine blocks, transmission cases, and various other components are often produced using sand casting. - Aerospace Specialized parts, including structural components and housings for electronic systems, are manufactured to meet stringent weight and safety requirements. - Construction and Heavy Machinery Large castings for engines, pumps, and construction equipment are made using this technique due to its ability to handle heavy and complex shapes.
Advantages of Sand Casting
The sand casting process offers several benefits
- Cost-Effective Sand casting is economical for both short and long production runs. The materials used, particularly sand, are inexpensive and widely available. - Versatility The technique can be used with a wide range of metals, including ferrous and non-ferrous alloys, making it suitable for various applications. - Complex Shapes Sand casting can easily produce intricate designs and complex geometries that may be challenging to achieve with other manufacturing methods. - Large Castings This process can accommodate large parts that are often difficult to manufacture using other techniques.
Limitations of Sand Casting
Despite its many advantages, sand casting also has limitations
- Surface Finish The surface finish obtained from sand casting may not be as smooth as those produced by other techniques, such as investment casting. - Dimensional Accuracy While sand casting can produce complex shapes, it may not achieve the same level of precision as other methods. - Labor-Intensive The process can be time-consuming and often requires skilled labor for pattern creation and mold assembly.
Conclusion
Sand casting remains a popular and essential method in the metalworking industry due to its flexibility, cost-effectiveness, and ability to produce complex parts. With advancements in technology and innovations in materials, sand casting continues to evolve, meeting the demands of modern manufacturing. As industries strive for efficiency and precision, sand casting will undoubtedly play a pivotal role in shaping the future of metal casting.
Post time:Ліст . 28, 2024 08:01
Next:Anvendelser af sandstøbning i industri og håndværk