Sand Casting Steel A Comprehensive Overview
Sand casting, also known as sand mold casting, is one of the most widely used metal casting processes in the foundry industry. It is particularly significant in the production of steel components. This method involves creating a mold from sand and pouring molten metal into that mold to form parts. The versatility, cost-effectiveness, and capability to produce complex shapes make sand casting a preferred choice for many applications, especially in steel casting.
The Process of Sand Casting
The sand casting process can be broken down into several key steps. These include pattern making, mold preparation, melting of steel, pouring, and finishing.
1. Pattern Making The first step involves creating a pattern, which serves as a replica of the final product. Patterns can be made from various materials, including wood, metal, or plastic, depending on the complexity and size of the casting. The pattern is typically slightly larger than the desired final product to account for shrinkage that occurs during the cooling process.
2. Mold Preparation Once the pattern is made, it is used to create a sand mold. This entails compacting sand around the pattern to form a mold cavity. The sand is mixed with a binding material, often clay, to ensure that it holds its shape after the pattern is removed. The mold is then carefully assembled, allowing for any necessary cores, which are used to create internal cavities in the casting.
3. Melting the Steel The next stage involves melting the steel in a furnace. The steel's specific type and grade are chosen based on the application requirements. Once the steel reaches the appropriate temperature, it is in a molten state and ready to be poured into the mold.
4. Pouring The molten steel is carefully poured into the mold cavity. Pouring techniques must be precise to prevent defects such as turbulence, which can cause imperfections in the final product. The pouring temperature is also critical; too high or too low can affect the integrity of the casting.
5. Cooling and Extraction After pouring, the steel must cool and solidify within the mold. This can take several hours depending on the size and thickness of the casting. Once cooled, the mold is broken away, and the casting is removed, often requiring some finishing processes such as grinding or machining to achieve the desired specifications.
sand casting steel
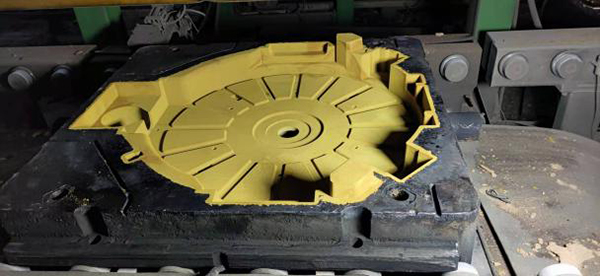
Advantages of Sand Casting Steel
Sand casting offers several advantages, especially when it comes to steel components
- Versatility Sand casting can produce a wide range of complex shapes and sizes, making it suitable for various industries including automotive, aerospace, construction, and art. - Cost-Effective The materials required for sand casting are relatively inexpensive. Sand is abundant and can be reused multiple times, reducing production costs. - Large Castings This method is capable of producing large castings that are not feasible with many other casting techniques. This is particularly important in industries that require heavy machinery and large components.
- Good Surface Finish While sand casting does not yield as smooth a finish as some advanced processes, it can still produce good surface finishes, especially with proper mold preparation and finishing techniques.
Challenges in Sand Casting Steel
Despite its many advantages, sand casting steel also presents challenges. The process can result in various defects, including sand inclusions, porosity, and dimensional inaccuracies. These issues can often be mitigated through careful control of parameters such as mold preparation, pouring techniques, and cooling rates.
Additionally, while sand casting is versatile, it may not be suitable for high-precision applications where tight tolerances are needed. In such cases, other casting methods such as investment casting or die casting may be preferred.
Conclusion
In conclusion, sand casting is a vital and practical method for producing steel components across various industries. Its flexibility and cost-effectiveness, along with the ability to create complex shapes, play a significant role in meeting the diverse needs of manufacturers. By understanding and addressing the challenges inherent in the process, founders can continue to leverage sand casting as a reliable production technique for steel and beyond. As technology advances, improvements in techniques and materials may further enhance the capabilities of sand casting, ensuring its relevance in modern manufacturing.
Post time:Каст . 20, 2024 11:45
Next:what is gold sand