Exploring the World of Sand Casting A Comprehensive Guide to Sand Castings Manufacturers
Sand casting, also known as sand mold casting, is one of the oldest and most versatile casting methods in the manufacturing industry. This process is vital in producing complex metal parts, and understanding its nuances can greatly assist in recognizing the capabilities of sand castings manufacturers.
What is Sand Casting?
At its core, sand casting involves creating a mold from a sand mixture, which then receives molten metal to form a desired shape. The flexibility of this method allows for the production of large and intricate parts, making it a preferred choice across various industries, including automotive, aerospace, and construction.
The Sand Casting Process
The process begins with the creation of a pattern, which is a replica of the final product. Patterns are usually made from materials like wood, metal, or plastic. Once the pattern is prepared, it is pressed into a sand mixture, often composed of silica sand, clay, and water. This creates a mold cavity that reflects the pattern's shape. To ensure sturdiness, the mold is compacted using different techniques depending on the manufacturer’s capabilities.
After forming the mold, it is then assembled and prepped for pouring. Molten metal, typically aluminum, iron, or steel, is carefully poured into the cavity. The cooling time depends on the size and thickness of the casting being produced. Once the metal solidifies, the mold is broken apart to reveal the sand casting, which may require further finishing processes such as grinding and sandblasting to achieve the desired surface finish and dimensional accuracy.
Advantages of Sand Casting
sand castings manufacturer
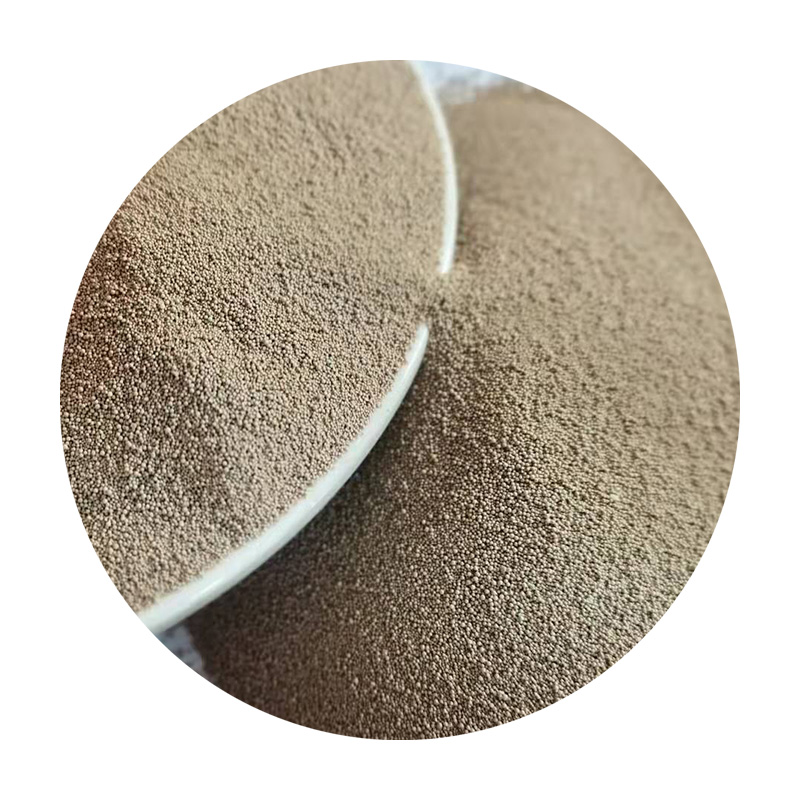
One of the key benefits of sand casting is its adaptability. Its ability to produce disproportionately large items or very intricate details sets it apart from other casting methods. The sand itself is reusable, making the process economically favorable and environmentally friendly. Additionally, sand casting is suitable for both low and high production volumes, allowing manufacturers to cater to a wide range of client needs.
Selecting a Sand Castings Manufacturer
When choosing a sand castings manufacturer, consider their experience and expertise in the industry. A reputable manufacturer should have a proven track record of producing high-quality castings at competitive prices. It's essential to verify their ability to work with different metals and alloys, as well as their proficiency in handling complex designs.
Quality assurance is also a critical factor; manufacturers should adhere to rigorous inspection processes to ensure consistent quality. Certifications such as ISO can indicate a commitment to maintaining industry standards. Furthermore, assessing their technological capabilities—such as advanced simulation software for mold design and optimized pouring techniques—can give insights into their operational efficiency.
The Future of Sand Casting
As industries evolve, so do the techniques used in sand casting. Innovations like 3D printing are starting to shape the future of mold production, allowing for even more complex designs and reducing lead times. However, traditional sand casting remains a cornerstone of manufacturing due to its established methods and ability to produce reliable and robust parts.
In conclusion, sand casting is a time-tested method that continues to thrive due to its versatility and adaptability. Understanding its processes and the critical role played by sand castings manufacturers can help businesses make informed decisions, ensuring quality and effectiveness in the production of metal parts. As technology progresses, the efficiency and capabilities of sand castings manufacturers are likely to expand, setting the stage for further advancements in this essential aspect of manufacturing.
Post time:Каст . 19, 2024 14:11
Next:3d sand printer price