Sand Casting with Resin Revolutionizing Metal Casting Techniques
Sand casting has long been one of the most reputable methods for producing metal components across various industries. Traditionally, this process relied on sand molds and metal alloys in a straightforward yet effective manner. However, recent advancements in materials and technology have introduced a new player to the field resin. The combination of sand and resin, known as resin sand casting, is revolutionizing the metal casting industry with enhanced efficiency, precision, and versatility.
The Basics of Sand Casting
To understand the impact of resin in sand casting, it is essential to grasp the traditional sand casting process. Traditional sand casting involves creating a mold from a mixture of sand and a binder. The metal is then poured into this mold to take shape. This method is favored for its ability to produce complex geometries and large-scale components economically. However, challenges such as mold strength, dimensional accuracy, and surface finish have persisted, often requiring additional finishing steps.
Introduction to Resin in Sand Casting
Resin sand casting merges conventional sand casting techniques with modern resin technology. In this method, a resin binder is used in conjunction with sand to create a high-strength mold. The resins are typically synthetic and are known for their excellent bonding properties. The molds created using this technique show enhanced durability and dimensional stability, which significantly improves the final product's quality.
Advantages of Resin Sand Casting
1. Enhanced Mold Strength One of the principal advantages of using resin is the remarkable strength it imparts to the mold. Traditional sand molds can break or deform under high temperatures, but resin molds offer superior resistance, allowing for more significant and intricate designs.
2. Improved Dimensional Accuracy The resin-bonded sand molds exhibit less thermal expansion compared to traditional sand molds. This precision is crucial in applications demanding strict tolerances. This dimensional accuracy minimizes the need for extensive post-casting machining, reducing time and costs.
sand casting resin
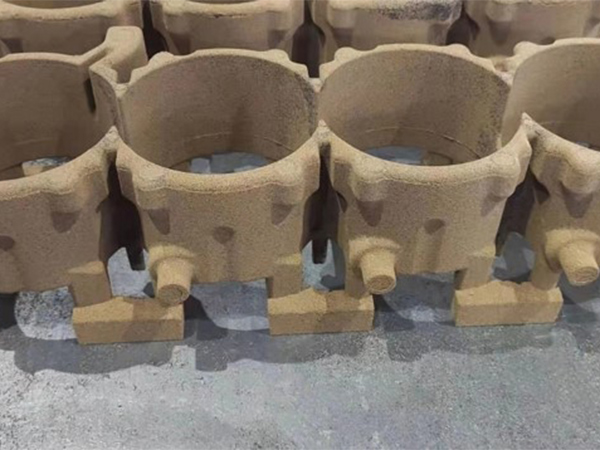
3. Better Surface Finish Due to the finer and more uniform structure of resin sand molds, the surface finish of castings produced is markedly superior. This quality reduces the need for surface treatments and provides a more aesthetically pleasing final product.
4. Reduced Lead Times The resin curing process is faster than that of traditional binders, which allows for quicker mold production. The immediate availability of high-quality molds accelerates the entire casting process, proving advantageous in industries where time is of the essence.
5. Versatility Resin sand casting is compatible with various metals, including aluminum, bronze, and iron. This versatility makes it a valuable option for industries ranging from automotive to aerospace to artistic sculpture.
Applications and Industries
The applications of resin sand casting are vast and diverse. In the automotive industry, precision-engineered components benefit significantly from the accuracy and strength of resin molds. Similarly, in the aerospace sector, where safety and reliability are paramount, the durability provided by resin sand casting techniques contributes to the production of critical aircraft parts.
Additionally, the artistic world has embraced resin sand casting. Sculptors can create intricate designs that would be difficult to achieve with traditional methods. The improved surface finish allows for detailed work that enhances the final aesthetic of the artwork.
Conclusion
As industries continue to evolve and strive for greater efficiency and higher-quality products, resin sand casting is undoubtedly a game changer. The marriage of resin and sand in the casting process demonstrates how innovative materials can address long-standing challenges in manufacturing. If the trend continues, we can expect even more advancements in metal casting techniques, leading to improved products and processes across various sectors.
In summary, resin sand casting not only enhances the traditional method but also opens new avenues for creativity and efficiency in manufacturing. As technology advances, the combination of resin and sand represents the future of casting, enabling producers to meet the demands of modern industries while setting new standards for quality and precision.
Post time:снеж . 10, 2024 19:49
Next:Understanding the Costs Involved in Sand Casting Processes and Techniques