Sand Casting Procedure An Overview
Sand casting is one of the oldest and most widely used metal casting processes, known for its versatility, simplicity, and cost-effectiveness. This procedure involves creating a mold from sand, into which molten metal is poured to form a desired shape. The following is a comprehensive overview of the sand casting process, outlining its key stages and considerations.
1. Pattern Making
The first step in sand casting is the creation of a pattern, which is a replica of the final product. Patterns are typically made from materials such as wood, metal, or plastic and are designed to be slightly larger than the desired final shape to account for shrinkage during cooling. The accuracy and finish of the pattern directly influence the quality of the final cast.
2. Molding
Once the pattern is ready, the next step involves creating the mold. This is done by compacting a mixture of sand and a binding agent, typically clay or synthetic resins, around the pattern. The sand must be properly mixed to achieve the right grain size and moisture content, which affects the mold's strength and permeability.
In practice, the molding process can be divided into two primary types open mold and closed mold. Open mold casting allows for easy access to the molten metal, while closed mold processes, such as investment casting, offer higher precision and can result in smoother surfaces.
3. Core Making
For complex shapes or internal features, cores made from sand or metal are created. Cores are additional components placed within the mold to form internal cavities. They are essential for producing intricate designs that cannot be attained with a single mold cavity. Careful consideration must be given to the core material, as it must withstand the heat of the molten metal.
4. Pouring
sand casting procedure
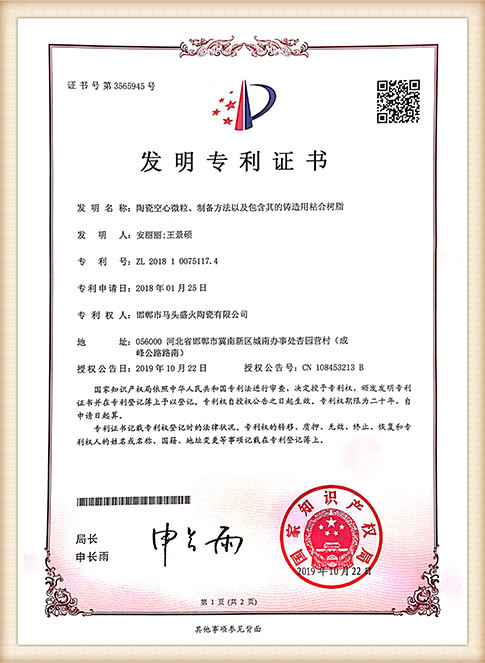
After the mold is prepared and any necessary cores are in place, the next step is pouring the molten metal into the mold. The metal is heated in a furnace to its melting point, achieving the desired temperature for pouring. The speed and technique of pouring are critical; too slow a pour can allow the metal to solidify prematurely, while too fast may lead to defects like turbulence or sand inclusion.
5. Cooling
Once the molten metal has been poured, it is allowed to cool and solidify. This cooling phase can take anywhere from a few minutes to several hours, depending on the size and thickness of the cast piece. During this time, the molten metal transitions into a solid state, taking the shape of the mold. Care must be taken to monitor cooling rates, as rapid cooling can introduce stresses and defects into the final product.
6. Mold Removal
After the metal has completely cooled and solidified, the mold is broken apart to reveal the casting. This process often involves mechanical shaking or vibration to separate the sand from the metal. Once the casting is extracted, any sand adhering to the surface must be cleaned off.
7. Finishing
The last step involves finishing the casting to achieve the desired surface quality and dimensions. This may include operations such as grinding, machining, or polishing to remove any imperfections and ensure that the casting meets the specified tolerances. Additionally, surface treatments such as painting or coating may be applied for corrosion resistance or aesthetic purposes.
Conclusion
Sand casting remains a fundamental process in the manufacturing industry due to its adaptability and effectiveness in producing a wide variety of metal components. Understanding the detailed stages of the sand casting procedure allows manufacturers to optimize their operations and produce high-quality castings efficiently. Whether for automotive parts, machinery components, or artistic sculptures, sand casting provides an essential solution in modern engineering and design.
Post time:снеж . 16, 2024 07:36
Next:The Evolution and Significance of Sand Casting in Metalworking History