Sand Casting Metal An Overview
Sand casting is a versatile and widely used metal casting process that has been employed for thousands of years. This method utilizes sand as the molding material, which gives it a unique set of characteristics that make it suitable for a variety of applications, from automotive components to artistic sculptures. In this article, we will explore the fundamentals of sand casting, its advantages, limitations, and its application in modern manufacturing.
The Process of Sand Casting
At its core, sand casting involves several key steps that transform molten metal into a solid object. The process begins with the creation of a mold. A pattern, usually made of a material like wood, metal, or plastic, is used to form the shape of the desired metal part in a sand mixture. This mixture typically consists of silica sand, a binder (such as clay), and water. The pattern is placed in a flask—a rigid frame that holds the sand—and the sand mixture is packed around it.
Once the sand has been compacted around the pattern, it is removed carefully to leave a cavity in the shape of the part to be cast. This mold is then assembled, and the molten metal is poured into the cavity through a sprue. After the metal cools and solidifies, the mold is broken apart, allowing the casting to be removed. Any excess material, known as flash, can be trimmed away, and the finished product may require additional machining or finishing processes.
Advantages of Sand Casting
One of the primary advantages of sand casting is its adaptability to a wide variety of metals, including aluminum, iron, copper, and bronze. Its flexibility makes it suitable for both small-scale and large-scale production runs. Since patterns can be made in various materials, it is also easy to create complex shapes and intricate designs that would be difficult to achieve with other casting methods.
Another significant advantage is cost-effectiveness. The materials used in sand casting are relatively inexpensive, and the process does not require expensive equipment. This makes it ideal for small manufacturers and for producing one-off components. Additionally, because sand is readily available in many regions, the logistics of sourcing materials are generally straightforward.
sand casting metal
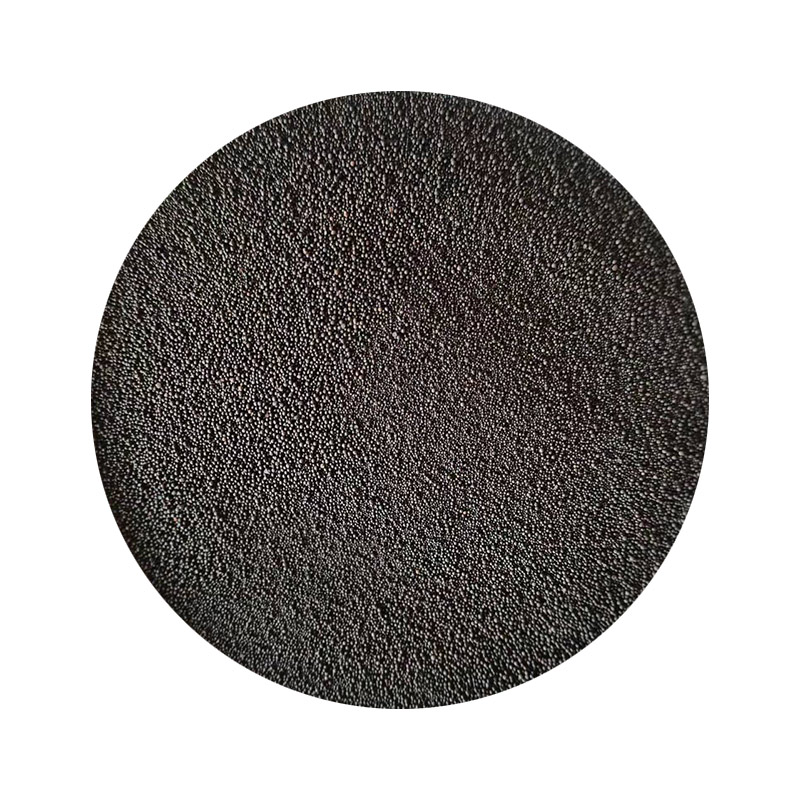
Limitations of Sand Casting
Despite its many benefits, sand casting does have some limitations. The surface finish of sand castings is typically rough, and the dimensional accuracy is often not as precise as other methods such as investment casting. This can require additional post-processing to achieve the desired smoothness and accuracy, which can add time and costs to the overall production.
Moreover, the sand casting process can be slow, especially compared to pressure die casting or other advanced techniques. The need for molds and patterns means that production rates may not be as high when compared to some modern manufacturing technologies.
Applications of Sand Casting
Sand casting is widely used across various industries. In the automotive sector, sand casting is employed to produce engine blocks, cylinder heads, and various other components. In the aerospace industry, it is used for turbine housings and structural elements where lightweight and strength are critical.
Beyond industrial applications, sand casting is also used in the art world. Artists and sculptors utilize this technique to create unique pieces and limited edition works. The ability to capture intricate details is one reason why sand casting remains popular among metal artists.
Conclusion
Sand casting is a time-honored method of metal casting that combines versatility, cost-effectiveness, and a broad range of applications. Despite its limitations, it continues to thrive in both industrial and artistic domains. As manufacturing processes evolve, sand casting remains a fundamental technique that reflects the ingenuity and adaptability of metalworking. Whether in producing practical components or artistic masterpieces, sand casting will continue to play a vital role in the world of metal fabrication.
Post time:Ліст . 06, 2024 18:59
Next:Innovative Techniques for 3D Printing with Wet Sand Materials in Construction Applications