The Role of Resin Sand in Modern Foundry Techniques
In the ever-evolving landscape of modern manufacturing, the use of resin sand has emerged as a pivotal innovation in the foundry industry. The transition from traditional sand casting methods to resin sand molding has been driven by the need for enhanced precision, improved product quality, and greater operational efficiency. This article explores the benefits, composition, and applications of resin sand in contemporary foundry practices.
Resin sand, as the name suggests, is a mixture of fine sand and thermosetting resin, which is usually activated by a catalyst. The most common types of resins used include phenolic, furan, and epoxy resins. This unique combination allows for the creation of molds that are not only highly durable but also capable of achieving intricate designs with superior surface finishes. This capability is essential in industries such as automotive and aerospace, where precision and detail are paramount.
One of the primary advantages of using resin sand is its ability to produce molds that can withstand high temperatures and mechanical stresses. Traditional sand molds often suffer from brittleness and poor dimensional accuracy, particularly in complex shapes. In contrast, resin sand molds exhibit improved resistance to thermal deformation and shrinkage, resulting in castings that require minimal post-processing. This translates to significant time and cost savings in production cycles.
resin sand
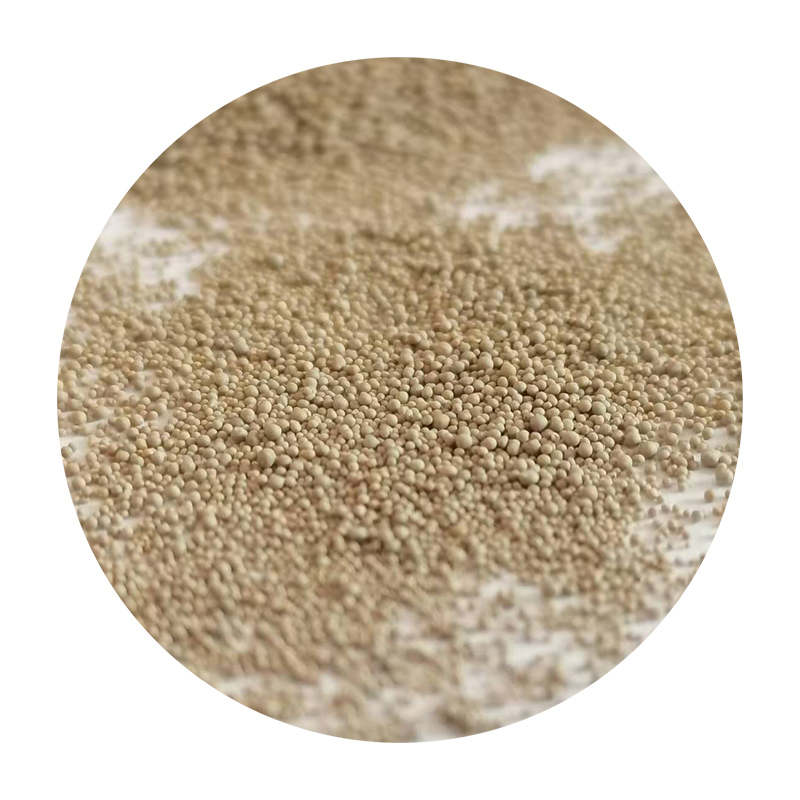
Moreover, resin sand molds provide a smoother surface finish compared to conventional green sand molds
. The fine grain structure of resin sand allows for a fine detail capture that is unmatched by traditional methods. This characteristic is especially beneficial for producing components with tight tolerances and intricate geometries, such as engine blocks, turbine housings, and various specialized tooling components.Another noteworthy aspect of resin sand technology is its environmental impact. The traditional foundry industry has faced increasing scrutiny over its ecological footprint, particularly regarding waste generation and emissions. Resin sand systems, however, are designed to minimize waste through recyclable sand materials and reduced binder consumption. Furthermore, advancements in resin formulations have led to the development of more eco-friendly options that do not compromise on performance. This alignment with sustainability goals is becoming crucial as industries transition towards greener manufacturing practices.
The versatility of resin sand is evident in its wide array of applications. It is not only utilized in the foundry sector but also finds uses in art casting, prototype development, and the production of complex mechanical components. The flexibility it offers in terms of mold design and composition allows manufacturers to cater to specific project requirements, thereby enhancing overall productivity.
In summary, resin sand has revolutionized the foundry industry by addressing the limitations of traditional casting methods. Its unique properties of durability, precision, and environmental sustainability make it a preferred choice among manufacturers looking to optimize their production processes. As technology continues to advance and industries increasingly demand higher quality standards, the adoption of resin sand is poised to grow, paving the way for innovative casting solutions and exceptional product outcomes. With the ongoing development in resin formulations and molding techniques, the future of resin sand in foundry applications looks promising, setting new benchmarks for quality and efficiency in metal casting.
Post time:Верас . 03, 2024 15:32
Next:ประเภทของทรายหล่อ - การหล่อทรายและเทคโนโลยี