Metal Sand Casting An Overview
Metal sand casting, also known simply as sand casting, is one of the oldest and most versatile manufacturing processes in the world. This technique involves the use of sand as the mold material to create complex metal parts. Its prolific use across various industries, including automotive, aerospace, and machinery, attests to its effectiveness and adaptability.
The sand casting process begins with creating a pattern, which is a replica of the desired product. Patterns can be made from a variety of materials, including wood, plastic, or metal, and they are typically slightly larger than the final part to account for metal shrinkage during cooling. The pattern is then placed in a mold box, and fine grains of sand, often mixed with a binder to enhance strength, are packed around it to form a mold.
Once the mold is prepared and the pattern is removed, the next step involves pouring molten metal into the mold cavity. Common metals used in sand casting include aluminum, iron, and bronze, which can be melted using electric furnaces or induction heaters. The molten metal fills the cavity, taking the shape of the mold. After sufficient cooling time, the metal solidifies and the mold is broken apart to reveal the cast part.
The primary advantage of metal sand casting lies in its ability to produce large and complex shapes. Unlike other casting methods, sand casting does not require extensive tooling, which significantly lowers production costs, especially for low to medium volume runs. Additionally, the process allows for the integration of various features like cores, which can create internal cavities in the castings.
metal sand casting
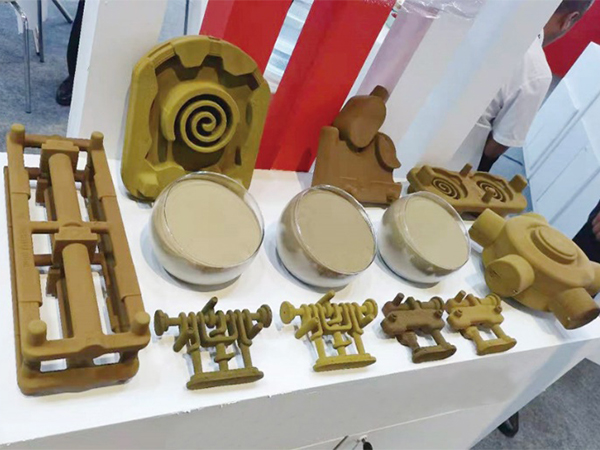
However, despite its many benefits, sand casting does have some drawbacks. The surface finish of sand-cast parts is typically rougher compared to other casting methods, such as investment casting. Moreover, the dimensional tolerance achieved through sand casting can be less precise, which may require additional machining operations for close-tolerance applications.
Another consideration is the environmental impact of the materials used in sand casting. The sand itself is recyclable, but the binders and other additives can pose waste disposal challenges. Many foundries are increasingly adopting environmentally friendly practices, such as using reclaimable materials and reducing emissions during the melting process.
The versatility of metal sand casting continues to be an asset in modern manufacturing. Innovations in technology are streamlining the process, allowing for better precision and improved casting quality. Advanced techniques, including 3D printing for pattern creation and the use of simulations to optimize mold design, are pushing the boundaries of what can be achieved with sand casting.
In conclusion, metal sand casting remains a fundamental component of the manufacturing landscape. Its ability to produce complex shapes in a cost-effective manner makes it ideal for a wide range of applications. As industries evolve and demand for high-quality parts continues to grow, sand casting is likely to remain a staple due to its resilience and adaptability to technological advancements.
Post time:Каст . 08, 2024 18:14
Next:Impression 3D sur résine sablée