The Importance of Metal Casting Sand in Foundry Operations
Metal casting is a significant technique employed in the manufacturing industry, enabling the production of complex metal parts with precision and efficiency. One crucial component of this process is casting sand, which acts as the mold material and directly influences the quality of the final product. Understanding the characteristics, types, and impact of casting sand is essential for optimizing metal casting operations.
Casting sand comes in various types, each suited for specific applications. The most commonly used is silica sand, prized for its excellent thermal stability and resistance to deformation. Silica sand is abundant and relatively inexpensive, making it a preferred choice in many foundries. However, it is not without its limitations—its fine particles can lead to defects, and it can produce harmful silica dust, posing health risks to workers.
Another popular type of casting sand is silica-free sand, such as zircon or chromite sand. These sands offer improved performance in terms of durability and finish quality. Further, zircon sand is highly resistant to thermal shock, making it ideal for high-temperature applications. While these alternatives are more costly, they can significantly enhance the quality of the cast parts, thus providing greater value in high-stakes manufacturing environments.
metal casting sand
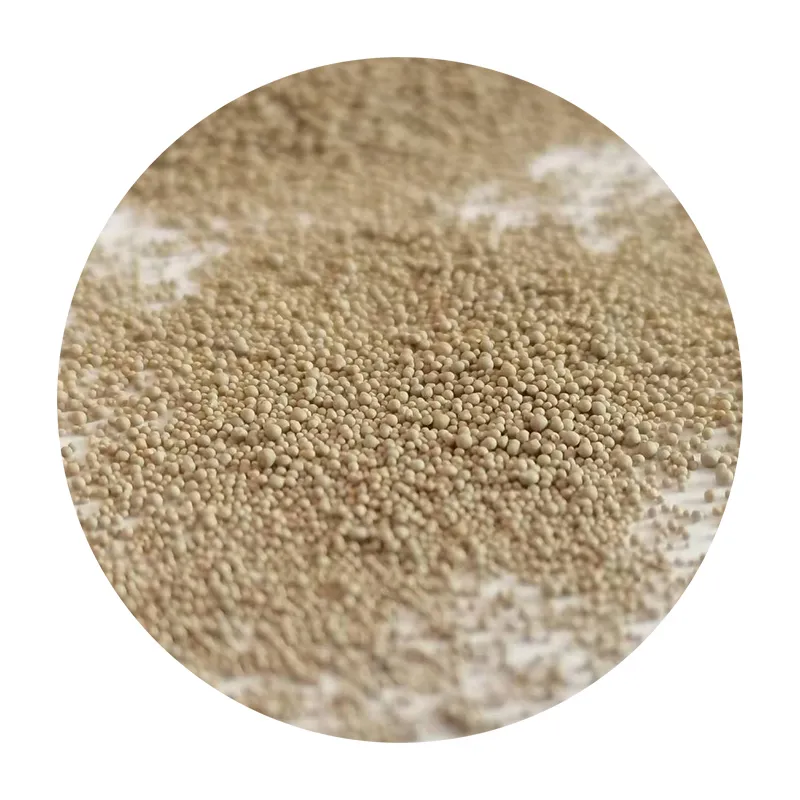
The selection of metal casting sand is critical because it directly affects several key factors mold strength, permeability, and refractoriness. Mold strength indicates the ability of the sand to hold its shape under pressure during the pouring of molten metal. Insufficient mold strength can lead to mold collapse and defective castings. Permeability, on the other hand, refers to the ability of gases to escape through the sand mold. Good permeability is essential to prevent gas retention and consequent defects, such as blowholes, in the final product. Lastly, refractoriness is the ability of the sand to withstand high temperatures without melting or deforming.
Besides the intrinsic properties of the sand, other factors play a role in the ultimate performance of casting sand in the foundry. This includes the mix of sand with binding agents and additives. Typically, sand is mixed with a binder, such as clay, to improve strength and cohesion. Additives like moisture, oil, or organic binders can enhance the mold's characteristics, affecting factors like workability and gas evolution during casting.
Effective sand management practices are pivotal in maintaining the quality of casting sand in foundries. This involves regular testing and screening of sand to remove impurities and ensure consistent grain size. Reclamation processes can also be implemented to recycle used sand, reducing waste and overall costs. Such measures not only improve the sustainability of metal casting operations but also enhance the efficiency and quality of the production process.
In conclusion, metal casting sand is a fundamental element within the foundry industry that significantly influences the quality and efficiency of casting operations. By selecting the appropriate type of sand, managing its properties, and employing effective reclamation and maintenance strategies, foundries can enhance their production capabilities. As the manufacturing industry continues to evolve, embracing innovations in casting sand technology and processes will be vital to staying competitive and meeting the growing demands for high-quality metal components. Thus, investing in the right casting sand and practices can lead to remarkable improvements in both the reliability and precision of metal casting endeavors.
Post time:Ліст . 19, 2024 18:33
Next:smooth 3d prints without sanding