The Art of Sand Casting A Timeless Technique in Metal Shaping
Sand casting, also known as sand mold casting, is one of the oldest and most versatile metal casting processes in existence today. This traditional method offers a unique combination of simplicity and efficiency, making it an enduring choice for artisans and industries alike. Whether for creating prototypes or producing large-scale components, sand casting has become a cornerstone in various manufacturing sectors.
At its core, sand casting involves the creation of a mold from a mixture of sand, water, and a binding agent. The process begins with the pattern, which is usually made from wood, metal, or plastic and mirrors the shape of the final product. This pattern is pressed or packed into a sand mixture to leave a detailed impression. Once the mold is formed, it is assembled and prepared for the molten metal.
The Art of Sand Casting A Timeless Technique in Metal Shaping
One of the main advantages of sand casting is its cost-effectiveness, especially for low to medium production runs. The materials required for sand casting are relatively inexpensive, and the process can be easily scaled to meet varying production demands. Additionally, because no elaborate machinery is needed, small workshops can readily execute sand casting projects, making it accessible to hobbyists and professionals alike.
make sand casting
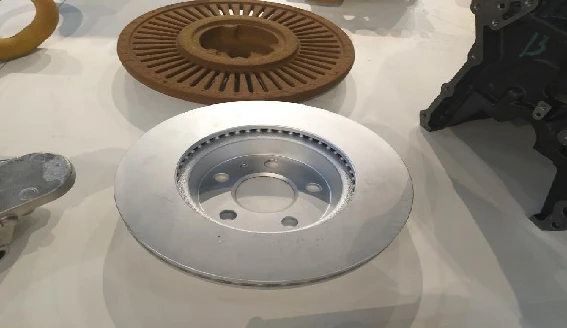
Another benefit of sand casting is its versatility. The process can accommodate intricate designs and large parts that would be challenging to produce using other methods, such as die casting or investment casting. Since the mold is made from sand, it is more forgiving to complex geometries and allows for a greater degree of artistic expression. This capability is particularly appealing in industries such as sculpture and art, where custom, one-off pieces are required.
However, sand casting does have its drawbacks. The surface finish of sand-cast products is typically rougher than those produced by other casting methods, which may necessitate additional machining or finishing processes for applications requiring a smoother finish. Furthermore, the process is generally slower than other high-speed alternatives, making it less suitable for high-volume production tasks.
Environmental considerations also play a role in the sand casting process. The sand used can be recycled multiple times, reducing waste and promoting sustainability. However, care must be taken to ensure the proper disposal of any binders and other additives that may not be biodegradable.
In conclusion, sand casting remains a fundamental technique in the world of metalworking. Its simplicity, cost-effectiveness, and adaptability make it an attractive option for many applications. While it may not be without its challenges, the advantages of sand casting ensure its continued relevance in modern manufacturing. As industries continue to evolve, so too will the methods and materials used in sand casting, keeping this ancient technique alive for generations to come. Whether for small-scale artisanal projects or large industrial components, sand casting embodies the spirit of craftsmanship and innovation in metal shaping.
Post time:Ліст . 14, 2024 12:30
Next:can you sand a 3d print