Lost Foam Casting Coating An Essential Component for Quality Castings
Lost foam casting (LFC) is an innovative process that merges the advantages of traditional casting methods with modern technology. This method allows for complex shapes and high precision in metal parts production, making it an invaluable technique in various industries, including automotive, aerospace, and manufacturing. One critical element in the lost foam casting process is the coating applied to the foam patterns, which plays a significant role in ensuring the quality and integrity of the final cast products. This article will explore the importance of lost foam casting coating, its application processes, and the materials used.
The Role of Coating in Lost Foam Casting
The primary objective of the coating in lost foam casting is to create a barrier between the molten metal and the foam pattern. When the molten metal is poured into the mold, it comes into contact with the foam, causing the foam to evaporate. A well-applied coating ensures that this evaporation occurs uniformly, minimizing defects such as misruns, cold shuts, or surface imperfections on the final casting.
The coating also provides necessary thermal insulation, reducing heat transfer between the molten metal and the foam. This thermal resistance helps to control the solidification rate of the metal, which is crucial for obtaining desirable mechanical properties in the final product. Additionally, a properly formulated coating can enhance the surface finish of the casting, resulting in reduced machining and finishing costs.
Types of Coatings Used in Lost Foam Casting
Various materials can be used for coatings in lost foam casting
. These include sodium silicate, ceramic, and other proprietary formulations designed to meet the specific requirements of different casting applications.1. Sodium Silicate Coating One of the most commonly used coatings in the lost foam casting process is sodium silicate, often known as water glass. This coating is applied as a liquid and dries to form a rigid shell. It is economical and has good thermal stability, making it suitable for many types of metals, including aluminum and iron. Sodium silicate also offers good adhesion to the foam pattern, ensuring that the coating remains intact during the pouring of the molten metal.
2. Ceramic Coating Ceramic coatings provide high levels of thermal resistance and can withstand higher pouring temperatures, making them ideal for non-ferrous metals. These coatings are typically applied in two or more layers to build up the necessary thickness. They offer excellent surface finish and can improve the overall mechanical properties of the casting.
lost foam casting coating
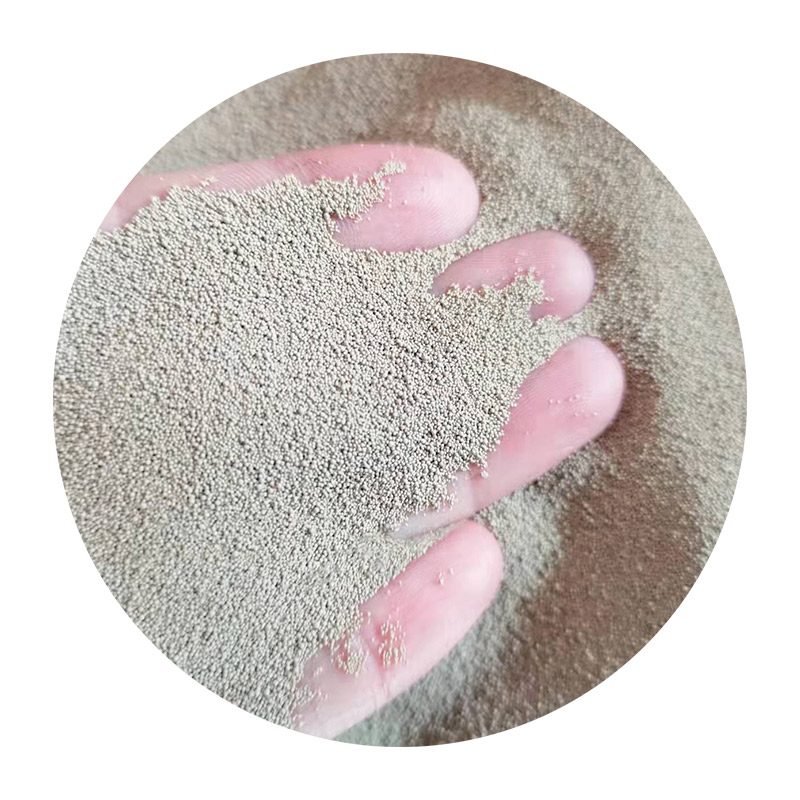
3. Proprietary Coatings Many manufacturers develop proprietary coating solutions tailored to specific casting needs. These coatings may be engineered to enhance certain attributes, such as viscosity, drying time, or thermal conductivity. The use of proprietary formulations allows for greater flexibility in optimizing the casting process based on material and design requirements.
Application Process for Lost Foam Casting Coatings
The application of coating in lost foam casting involves several key steps
1. Preparation of Foam Patterns The foam patterns must be prepared and cleaned to ensure proper adhesion of the coating. Any debris or contaminants can hinder the coating’s ability to bond.
2. Coating Application The coating is typically applied using dipping, spraying, or brushing methods. The chosen application method depends on the coating material and the complexity of the foam pattern.
3. Drying and Curing After application, the coating must be allowed to dry and cure properly to develop the necessary properties. This step is critical, as insufficiently dried coatings can lead to defects in the final casting.
4. Quality Control Final checks should be conducted to ensure that the coating is uniform, defect-free, and meets the required thickness. Visual inspections, as well as specialized tests, may be employed to confirm coating integrity.
Conclusion
In conclusion, lost foam casting coating is a vital component in the production of high-quality castings. Its mission extends beyond simply acting as a barrier; it plays a key role in optimizing the thermal and structural integrity of the final product. The selection of appropriate coating materials and application techniques is crucial for achieving successful castings with fine tolerances and excellent surface finishes. As lost foam casting techniques continue to evolve, so too will the innovations in coating materials and processes, paving the way for even greater advancements in manufacturing technology.
Post time:снеж . 03, 2024 11:23
Next:resin coated sand plant