Hard Sand Casting A Blend of Tradition and Technology
Hard sand casting, often referred to as sand casting, is one of the oldest and most versatile manufacturing processes known to mankind. It’s a method that has stood the test of time, evolving through technological advancements while retaining its foundational principles. With applications spanning numerous industries, from automotive to aerospace, understanding the intricacies of hard sand casting is essential for anyone involved in metalworking.
The Process
At its core, hard sand casting involves creating a mold from a mixture of sand, clay, and water. The sand is compacted around a pattern that mimics the final object. The patterns can be crafted from various materials, including metal, plastic, or wood, and are designed with allowances for shrinkage and finishing. Once the mold is prepared, the pattern is removed, leaving a cavity that represents the shape of the desired part.
The next step involves pouring molten metal into the mold cavity. The metal solidifies as it cools, forming a solid object that mirrors the shape of the mold. After the metal has cooled sufficiently, the mold is broken apart to reveal the casting. The final steps involve trimming away excess material, machining surfaces for precision, and finishing the surface to meet the desired specifications.
Advantages of Hard Sand Casting
One of the most significant advantages of hard sand casting is its flexibility
. It can accommodate a wide range of metal types, including aluminum, iron, and bronze, and is suitable for producing both small and large parts. The ability to create complex geometries is another major benefit, making it ideal for intricate designs that may be challenging to achieve using other methods.Furthermore, hard sand casting is relatively cost-effective, especially for low to medium production runs. The materials used, primarily sand and binder, are inexpensive and readily available. Unlike other casting techniques, such as investment casting, which may require considerable tooling costs, sand casting allows for a quick turnaround time in developing molds.
hard sand casting
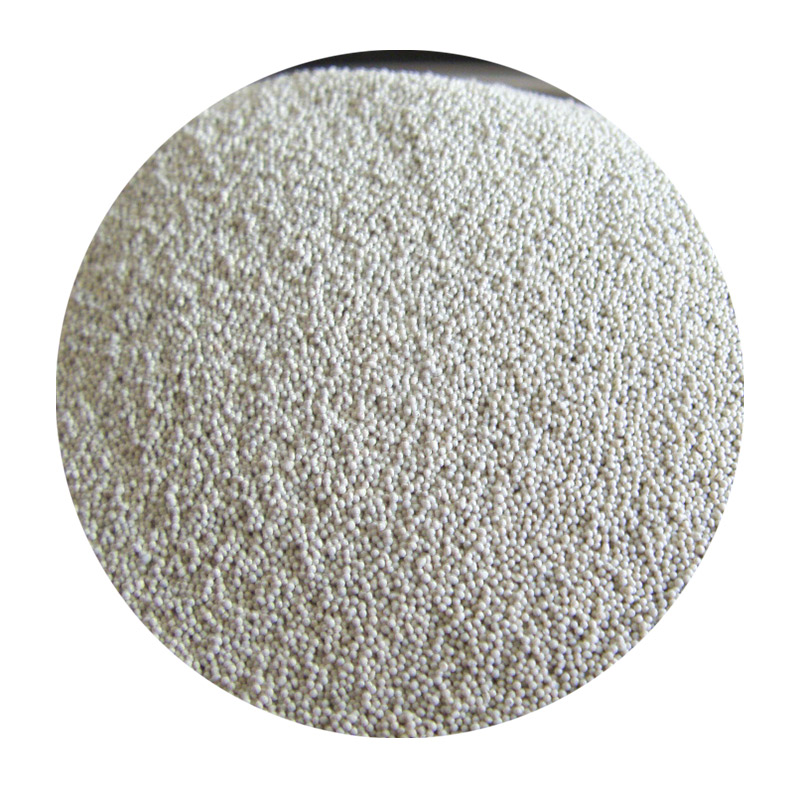
Challenges and Solutions
While hard sand casting certainly comes with numerous advantages, it is not without its challenges. One of the primary issues encountered is the potential for defects such as porosity and surface imperfections. These can arise from factors like improper mold preparation, inadequate molten metal quality, or incorrect pouring techniques.
To address these challenges, advancements in technology play a crucial role. The use of computer-aided design (CAD) and simulation software can significantly enhance the mold design process. By modeling the molten metal flow and cooling stages, engineers can identify potential defects before casting begins. Additionally, modern materials for sand casting molds, such as resin-bonded sands, improve surface finish and reduce the likelihood of defects.
Environmental Considerations
As with many manufacturing processes, hard sand casting has environmental implications. Traditional sand casting methods can generate waste materials that need proper disposal. However, efforts are underway to mitigate these impacts. Recycling sand and using eco-friendly binders are becoming prevalent practices in the industry. Not only do these methods reduce waste, but they also contribute to sustainability efforts.
Conclusion
Hard sand casting remains a foundational process in metal manufacturing, combining traditional techniques with modern advancements. Its capacity for producing complex shapes, alongside its cost-efficiency, ensures its continued relevance in various industries. By embracing new technologies and prioritizing sustainable practices, the future of hard sand casting looks promising, allowing it to thrive in an ever-evolving manufacturing landscape. As industries seek to balance efficiency, quality, and environmental responsibility, hard sand casting will play a pivotal role in meeting these demands.
Post time:Каст . 12, 2024 18:25
Next:3d printing for sand casting