The Difference Between Sand Casting and Die Casting
Casting is a fundamental manufacturing process used in various industries to produce complex metal parts. Among the most commonly used methods are sand casting and die casting, each with its unique advantages, disadvantages, and application areas. Understanding the differences between these two casting techniques can help businesses and engineers to choose the right method for their specific requirements.
Sand Casting An Overview
Sand casting is one of the oldest and most versatile casting processes. In this method, a mold is created using a mixture of sand, clay, and water, which is packed around a pattern of the desired part. The pattern is typically made from a non-metallic material, such as wood or plastic. Once the mold is formed, it is prepared for pouring by creating a cavity that corresponds to the part shape.
The molten metal is then poured into the mold cavity and allowed to cool and solidify. After cooling, the sand mold is broken apart, and the casting is removed. Sand casting can accommodate metals with high melting points and is suited for both ferrous and non-ferrous alloys.
Die Casting An Overview
Die casting, on the other hand, involves forcing molten metal under high pressure into a pre-formed metal mold, known as a die. This process allows for a high level of precision and smooth surface finishes, making it ideal for producing intricate parts in large quantities. Die casting can be done using various metal alloys, including aluminum, zinc, and magnesium.
There are two primary types of die casting processes hot chamber and cold chamber. Hot chamber die casting is used for low-melting-point alloys and allows for quicker cycle times, while cold chamber die casting is used for higher melting-point metals and generally involves a slower process but can handle a wider variety of materials.
difference between sand casting and die casting
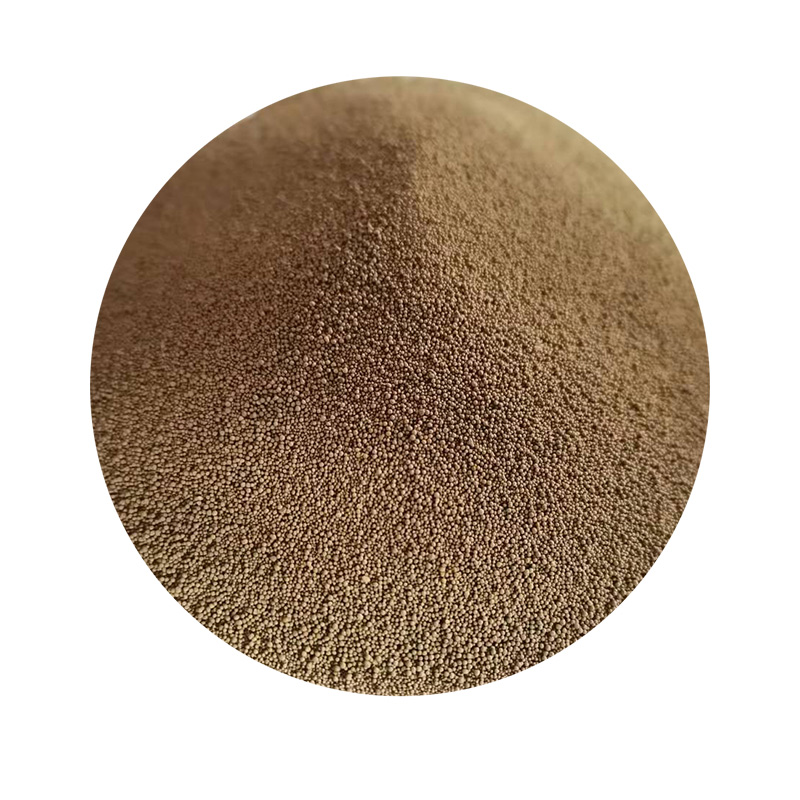
Key Differences
1. Material Properties - Sand casting can be used for a broader range of metals, including those with higher melting points, while die casting is often limited to non-ferrous metals like aluminum and zinc.
2. Production Volume - Sand casting is better suited for low to medium production volumes and is often used for prototypes or custom parts. Conversely, die casting is most efficient for high-volume production runs due to its speed and consistency.
3. Cost Implications - The initial tooling cost for die casting is significantly higher than that of sand casting due to the complexity of die manufacturing. However, the per-unit cost is lower in die casting as production volumes increase. Sand casting, with its lower setup cost, may be more economical for small batches.
4. Surface Finish and Detail - Die casting typically produces parts with superior surface finish and dimensional accuracy, making it preferable for applications where detail is critical. Sand casting may yield a rougher finish and has lower accuracy, which can require additional machining for tight tolerances.
5. Cooling Rates - In die casting, the rapid cooling of the molten metal leads to fine grain structures and enhanced mechanical properties. Sand casting tends to cool slower, resulting in coarser grains and potentially lower strength in some applications.
Conclusion
In summary, the choice between sand casting and die casting largely depends on the specific requirements of the project, including the type of material, production volume, cost constraints, and desired part characteristics. Understanding these differences is crucial for engineers and manufacturers to optimize their production processes and achieve the best possible outcomes for their products. Whether opting for the versatility of sand casting or the precision and efficiency of die casting, each method has its place in the modern manufacturing landscape.
Post time:снеж . 02, 2024 05:46
Next:Understanding Molding Sand Types for Effective Metal Casting Processes