3D Printing in Sand Casting Revolutionizing Manufacturing Processes
The manufacturing industry has continually evolved over the years, with technological advancements paving the way for innovative processes. One such innovation that has revolutionized the casting industry is the integration of 3D printing with sand casting. This combination not only enhances production efficiency but also offers a myriad of benefits that traditional methods struggle to achieve.
Sand casting, one of the oldest casting methods, involves the creation of a mold from sand and then pouring molten metal into this mold to produce various metal parts. Traditionally, this process has been time-consuming and labor-intensive, with the creation of mold cores often requiring considerable manual effort and expertise. However, with the advent of 3D printing technology, particularly in the production of sand molds, the manufacturing landscape is undergoing a significant transformation.
3D Printing in Sand Casting Revolutionizing Manufacturing Processes
Additionally, 3D-printed sand molds offer greater design flexibility. Engineers and designers can create intricate geometries and complex shapes that would be challenging or even impossible to achieve using conventional molding techniques. The ability to iterate designs quickly and efficiently leads to enhanced innovation and the creation of more advanced products. This adaptability is especially beneficial in industries such as aerospace and automotive, where lightweight and optimized components are critical.
3d printing sand casting
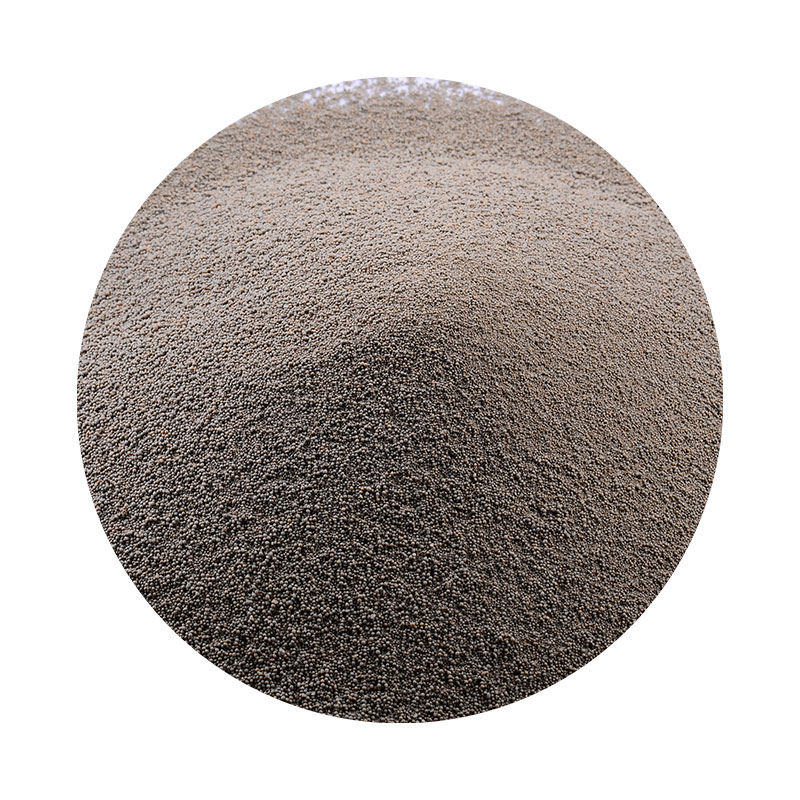
Cost-effectiveness is another significant benefit of integrating 3D printing with sand casting. Although the initial investment in 3D printing technology can be substantial, the long-term savings from reduced material waste, lower labor costs, and decreased lead times can outweigh these costs. Traditional sand casting requires extensive use of raw materials, and the molding process generates waste. In contrast, 3D printing optimizes material use, allowing for more sustainable production practices.
Moreover, the use of 3D printing in sand casting simplifies the supply chain. Traditional methods often involve multiple suppliers and complex logistics to coordinate different stages of production. With 3D printing, manufacturers can produce molds in-house, reducing reliance on external suppliers and minimizing potential delays associated with transportation and outsourcing.
However, the shift to 3D printing in sand casting is not without challenges. Issues such as the need for specialized equipment, the requirement for skilled operators, and the familiarity with new technologies can pose hurdles for some manufacturers. Additionally, there are considerations around material properties and the need for thorough testing to ensure that parts produced meet the necessary performance standards.
In conclusion, 3D printing in sand casting represents a pivotal advancement in the casting industry. By reducing lead times, offering design flexibility, ensuring cost efficiency, and streamlining the manufacturing process, this technology is reshaping how products are designed and produced. As more companies embrace these innovations, we can expect to see even greater developments in manufacturing, leading to better products and more sustainable practices in the years to come. The future of casting is undoubtedly intertwined with the capabilities of 3D printing, opening new horizons for creativity and efficiency in the manufacturing sector.
Post time:Ліст . 15, 2024 00:30
Next:iron sand casting process