3D Printed Sand Casting Patterns Revolutionizing the Foundry Industry
In recent years, the manufacturing landscape has undergone a significant transformation, driven by advancements in technology. Among these innovations, 3D printing has emerged as a game changer across various industries. One particularly noteworthy application of this technology is in the realm of sand casting, where 3D printed patterns are revolutionizing traditional foundry practices. This article will explore the benefits, processes, and implications of using 3D printed sand casting patterns in modern manufacturing.
Understanding Sand Casting
Sand casting is one of the oldest and most versatile manufacturing processes used to create metal parts. It involves creating a mold from a pattern, which is typically made of metal, wood, or plastic. The mold is then filled with molten metal, allowing it to solidify and take the shape of the pattern. While effective, traditional sand casting methods can be time-consuming and costly, particularly in terms of pattern production. This is where 3D printing comes into play.
The Process of 3D Printing Sand Casting Patterns
3D printing, or additive manufacturing, involves layer-by-layer deposition of material to create complex geometries. In the case of sand casting, 3D printing allows for the fabrication of patterns directly from CAD models. The patterns are printed using a special sand material that is bonded together with a liquid binder. This process eliminates the need for traditional machining and tooling, significantly shortening lead times and reducing costs.
Advantages of 3D Printed Sand Casting Patterns
1. Design Flexibility One of the primary benefits of 3D printed patterns is the design freedom it affords manufacturers. Complex geometries and intricate details that would be impossible or prohibitively expensive to achieve with traditional methods can be easily realized. This enables engineers to innovate and improve product performance without the constraints imposed by conventional tooling.
2. Reduced Lead Times The conventional pattern-making process can take weeks or even months, depending on the complexity of the design. In contrast, 3D printing can produce patterns in a matter of days, significantly speeding up the prototyping and production phases. This rapid turnaround is particularly advantageous in industries where time-to-market is critical.
3d printed sand casting patterns
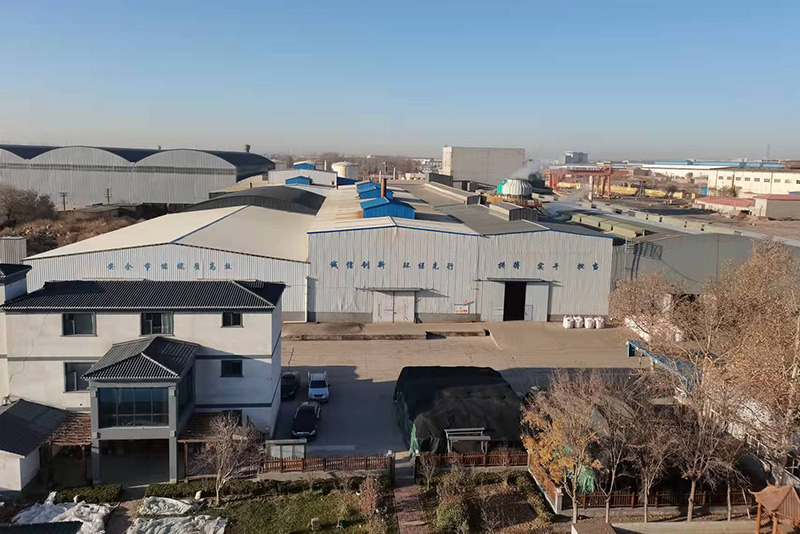
3. Cost Efficiency Traditional sand casting patterns often require costly materials and labor-intensive processes. 3D printing reduces these costs by minimizing material waste and eliminating the need for expensive molds. Additionally, because patterns can be printed on demand, manufacturers can reduce inventory costs and respond more swiftly to market changes.
4. Sustainability As industries increasingly focus on sustainability, 3D printing offers a more environmentally friendly alternative to traditional casting. The additive nature of the process means that only the necessary material is used, resulting in less waste. Furthermore, many 3D printing materials can be recycled, further contributing to sustainable practices in manufacturing.
5. Enhanced Precision and Accuracy The level of precision achievable with 3D printing is often superior to that of traditional methods. This accuracy ensures that the final cast components meet stringent quality standards, reducing the likelihood of defects and the need for rework.
Implications for the Foundry Industry
The integration of 3D printed sand casting patterns has significant implications for the foundry industry. It not only streamlines the manufacturing process but also fosters innovation and creativity. Traditional foundries that embrace this technology can enhance their competitiveness by offering clients customized solutions and faster delivery times.
However, this transition is not without its challenges. Foundries must invest in new technologies and training to adapt to the changes brought about by 3D printing. Additionally, while 3D printing is a powerful tool, it is not a one-size-fits-all solution. Manufacturers must evaluate the feasibility of integrating this technology into their operations based on the specific requirements of their projects.
Conclusion
The advent of 3D printed sand casting patterns marks a pivotal evolution in manufacturing, particularly within the foundry sector. By offering greater design flexibility, reduced lead times, cost efficiency, sustainability, and enhanced accuracy, this technology empowers manufacturers to meet the demands of a rapidly changing market. As the foundry industry continues to adapt to technological advancements, those who embrace the potential of 3D printing will not only survive but thrive in the competitive landscape of modern manufacturing. The future is bright for foundries willing to innovate and evolve with the times.
Post time:Ліст . 07, 2024 07:17
Next:Ceramic Sanding Discs for Efficient Surface Finishing and Precision Smoothing Techniques