The Art and Science of Sand Casting Metal
Sand casting is one of the oldest and most versatile metal casting processes, dating back thousands of years. This technique has played a significant role in the manufacturing industry, offering unique advantages that have made it a favorite among engineers and metalworkers alike. In this article, we will explore the process of sand casting, its advantages, and its applications.
What is Sand Casting?
Sand casting, also known as sand mold casting, entails creating a mold from sand to form metal parts. The process begins with creating a pattern of the desired part, typically made of metal, plastic, or wood. This pattern is then placed in a mixture of sand and a binding agent, which is compacted into a mold. The mold is subsequently opened, and the pattern is removed, leaving a cavity that reflects the shape of the original pattern.
The next stage involves pouring molten metal into the mold cavity. Once the metal cools and solidifies, the mold is broken apart to reveal the cast part. The final step is the finishing process, where any excess material, burrs, or imperfections are removed, and the part is polished as needed.
Advantages of Sand Casting
One of the most significant benefits of sand casting is its flexibility in terms of materials and sizes. Almost any metal can be used in sand casting, including aluminum, iron, bronze, and brass, making it suitable for a wide range of applications. Sand casting can also accommodate parts of varying sizes, from small intricate designs to large components used in machinery and automotive parts.
sand cast metal
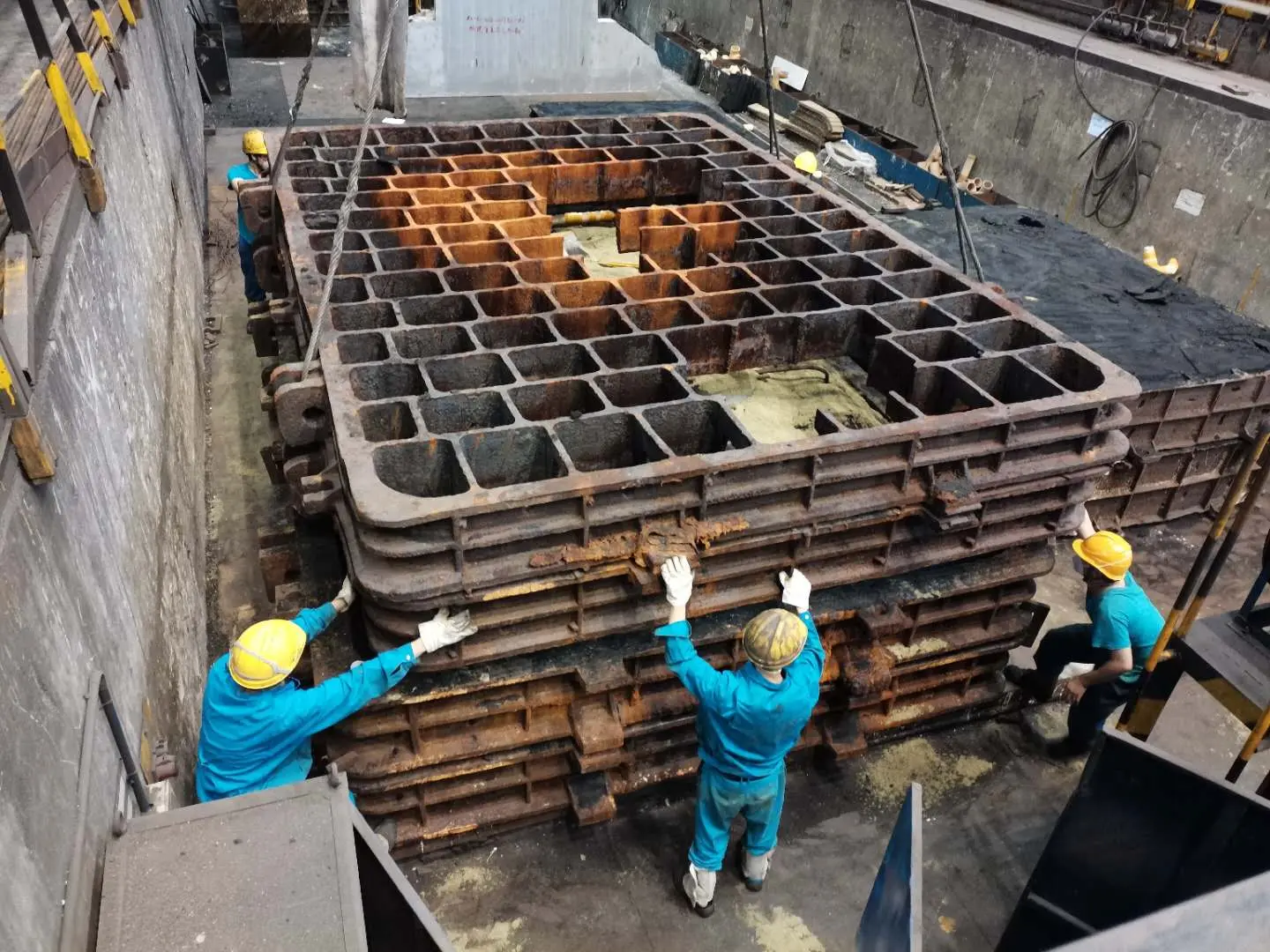
Another advantage is the cost-effectiveness of sand casting. The materials required for making sand molds are relatively inexpensive, and the process can be conducted using simple equipment. This quality makes sand casting an attractive option for small manufacturers and hobbyists.
Additionally, sand casting offers good dimensional accuracy and surface finish. While not as precise as some modern techniques like die casting or investment casting, it still provides a reasonable level of detail for many applications. With advancements in technology, the precision and finish of sand cast parts have continued to improve.
Applications of Sand Casting
Sand casting finds applications across various industries due to its versatility. The automotive sector is one of the most prominent users of sand casting, utilizing it to manufacture engine blocks, transmission cases, and other critical components. The aerospace industry also employs sand casting to produce parts for aircraft, ensuring lightweight and sturdy components that meet strict safety standards.
In the industrial field, sand casting is crucial for producing gear boxes, pumps, and valves. The renewable energy sector also benefits from sand casting through the production of turbine components. Moreover, in art and sculpture, artists often use sand casting to create bronze sculptures and decorative pieces, showcasing the artistic capabilities of this ancient technique.
Conclusion
Sand casting is a time-honored method that continues to thrive in the modern manufacturing landscape. Its blend of simplicity, cost-effectiveness, and versatility makes it an ideal choice for a broad spectrum of applications. As industries evolve and the demand for unique components expands, sand casting will undoubtedly remain an essential process for creating high-quality metal products. Whether for intricate art pieces or essential machinery parts, the art and science of sand casting metal hold an important place in the world of manufacturing, reflecting both tradition and innovation.
Post time:Dek . 05, 2024 15:19
Next:spherical sand