Metal Sand Casting An Essential Process in Manufacturing
Metal sand casting is one of the oldest and most versatile manufacturing processes used to create metal components. This technique involves pouring molten metal into a sand mold that has been shaped to the desired geometry of the final product. The process has stood the test of time due to its effectiveness, cost-efficiency, and ability to create complex shapes.
The initial step in the sand casting process entails creating a pattern, which is essentially a replica of the desired metal part. Patterns can be made from various materials, including wood, plastic, or metal, depending on the production requirements and the expected volume. Once the pattern is prepared, it is placed within a flask, a type of container that holds the sand mixture that forms the mold.
The sand used for casting is typically a mixture of high-quality silica sand, clay, and water. The sands' bonding properties are crucial for maintaining the shape of the mold as it is created. The pattern is then covered in the sand mixture, and the sand is compacted around it to form a rigid mold. After the mold is formed, the pattern is removed, leaving behind a void in the shape of the desired part.
One of the key advantages of metal sand casting is its ability to produce intricate designs that would be difficult to achieve through other manufacturing processes
. The malleability of sand allows for the creation of complex geometries and detailed features, making it suitable for a wide range of applications across various industries, including automotive, aerospace, and machinery.metal sand casting
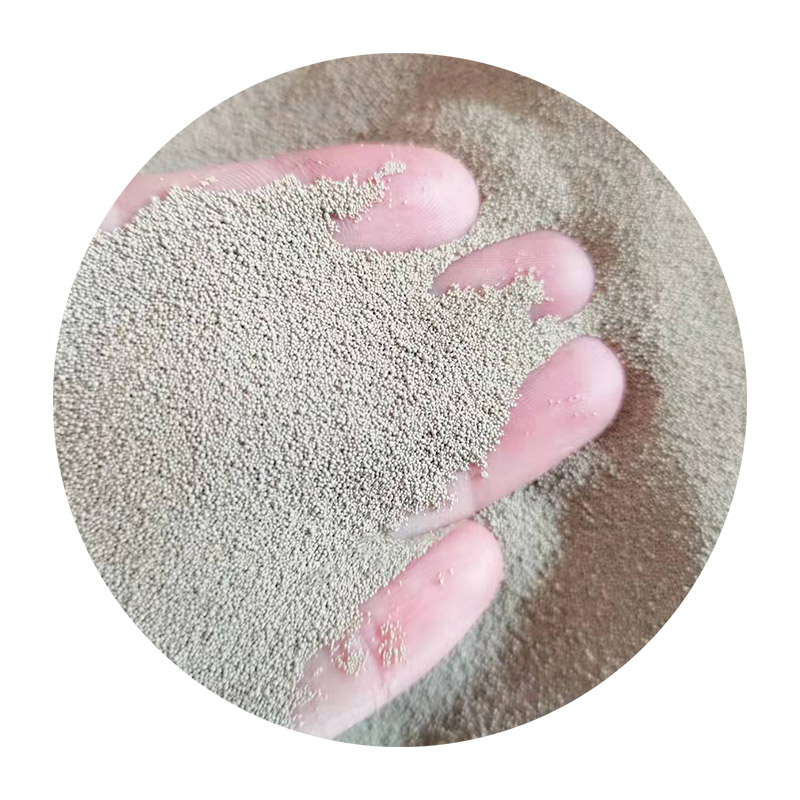
After the mold is created, the molten metal is carefully poured into the cavity. It is essential to control the temperature of the metal to ensure it flows properly into every part of the mold. Depending on the type of metal being used (such as aluminum, cast iron, or bronze), different melting points and pouring temperatures are required.
Once the molten metal has cooled and solidified, the mold is broken away to reveal the cast part. This stage of the process is often followed by finishing operations, which may include grinding, machining, or surface treatment, to achieve the final dimensions and surface quality required by the application.
While metal sand casting is an efficient method for producing metal parts, it is important to note that it is not without its challenges. For instance, controlling the quality of the sand, ensuring the accurate alignment of the mold halves, and managing thermal contraction during cooling can all pose difficulties. Therefore, skilled operators and quality control measures are critical to ensure a high standard of output.
In conclusion, metal sand casting remains a vital process in the manufacturing sector, providing a means to produce high-quality metal components at a reasonable cost. Its adaptability to various materials and complexity in design continues to make it an attractive option for industries worldwide. As technology progresses, innovations in sand casting techniques and materials promise to enhance the efficiency and scope of this traditional yet essential manufacturing method.
Post time:Sen . 10, 2024 05:26
Next:what is sand casting in engineering