Lost Foam Casting Materials An Overview
Lost foam casting is a unique and versatile metal casting process that leverages the use of expandable polystyrene (EPS) patterns. This innovative technique has gained popularity in various manufacturing sectors due to its ability to produce complex shapes with high accuracy and excellent surface finishes. In this article, we will explore the materials involved in lost foam casting, their properties, and the benefits they bring to the casting process.
The Basics of Lost Foam Casting
Lost foam casting is a process that combines the principles of investment casting and traditional sand casting. The process begins with creating a foam pattern, usually constructed from EPS. This foam pattern is coated with a refractory material to form a shell. Once the shell is hardened, the foam is vaporized by pouring molten metal into the cavity, leaving behind a precise metal replica of the original foam.
Core Materials in Lost Foam Casting
1. Expandable Polystyrene (EPS) EPS is the primary material used for making patterns in the lost foam casting process. This lightweight and cost-effective plastic allows for the creation of intricate designs with minimal tooling. The key features of EPS include its ability to be easily shaped and its excellent dimensional stability. Furthermore, EPS patterns can be produced rapidly, significantly speeding up the prototyping phase in manufacturing.
2. Coating Materials The coating applied to the EPS pattern plays a crucial role, as it must withstand the high temperatures of molten metal while providing strength and support. Commonly used materials include ceramic slurries that can be composed of aluminosilicate, silica, and other refractory particles. These coatings not only provide thermal resistance but also help in achieving a smooth surface finish on the final cast product.
3. Filler Materials In some applications, fillers may be added to the coating material to enhance certain characteristics. For instance, adding fine sand can improve the shell’s permeability, allowing gas to escape during the pouring process which can minimize defects. Other additives can increase strength or help control the thermal expansion of the mold.
4. Binder Materials To ensure that the sand mixture used in creating the coating adheres well, binders are incorporated. These binders can include sodium silicate or organic binders that help in binding the refractory material while maintaining the necessary flexibility and strength.
lost foam casting materials
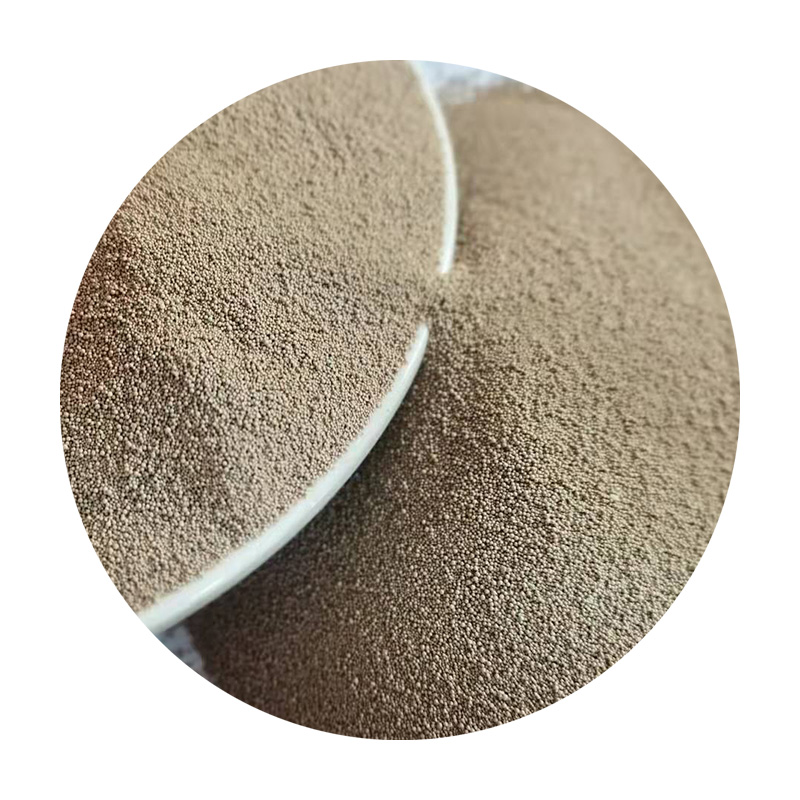
Advantages of Using These Materials
The choice of materials in lost foam casting directly influences the quality and efficiency of the manufacturing process
. Here are some advantages1. Complex Geometries The use of EPS allows manufacturers to create intricate shapes and designs that would be difficult or impossible to achieve with traditional casting methods. This capability is particularly beneficial in industries like aerospace, automotive, and art.
2. High Precision Lost foam casting is known for its high dimensional accuracy, which reduces the need for extensive machining post-casting. This precision is largely attributed to the accurate replication of the EPS pattern.
3. Excellent Surface Finish The careful application of the coating material ensures that the final casting exhibits a smooth surface finish. This quality reduces the need for additional surface treatments, saving both time and resources.
4. Reduced Waste The process of lost foam casting minimizes material waste. Since the foam pattern is vaporized during the pouring of molten metal, there are no scrap pieces left behind as in other casting processes. This factor contributes to lower costs and a more environmentally friendly manufacturing process.
Conclusion
The lost foam casting process represents a significant advancement in metal casting technology, largely due to the innovative use of materials such as expandable polystyrene, refractory coatings, and binding agents. Its ability to produce complex shapes with high precision and excellent surface finishes has made it a preferred choice in various industries. As advancements in materials science continue to evolve, the potential applications and efficiencies of lost foam casting are expected to expand, solidifying its place in the future of manufacturing.
Post time:Noy . 09, 2024 10:40
Next:Innovative Methods for Enhancing Coated Sand Applications in Various Industries