Lost Foam Casting A Revolutionary Approach in Foundry Technology
Lost foam casting (LFC) is an innovative metal casting process that has revolutionized the foundry industry in recent decades. This method, which involves the use of a foam pattern, offers several advantages over traditional casting techniques, making it increasingly popular among manufacturers seeking cost-effective and high-quality solutions for metal parts.
The Process Defined
The lost foam casting process begins with the creation of a foam pattern, typically made from expanded polystyrene (EPS). This foam pattern is an exact replica of the finished product and can be produced with remarkable precision. Once the pattern is fabricated, it is coated with a fine layer of sand mixed with a binding agent. This layer is crucial for ensuring the final metal part maintains its desired surface finish.
After coating, the foam pattern is placed in a mold box filled with more sand. The next step involves introducing molten metal into the mold. As the metal is poured, it comes into contact with the foam, which evaporates or disappears. This unique feature is where the lost aspect of the process gets its name. The molten metal then fills the cavity left by the foam pattern, assuming its shape and details. Finally, once the metal has cooled and solidified, the sand mold is broken away, revealing the final cast product.
Advantages of Lost Foam Casting
One of the most significant advantages of lost foam casting is its ability to produce complex shapes with excellent surface quality. The foam pattern can be intricately designed and modified, allowing for greater design flexibility compared to conventional methods where patterns are usually made of rigid materials such as metal or wood. This versatility is particularly beneficial for industries producing components with elaborate geometries.
Another critical advantage is the reduction in material waste. The traditional casting process often generates scrap metal, as excess material needs to be trimmed from the final product. In contrast, lost foam casting minimizes these losses, as the foam pattern is fully consumed during the casting process. This not only enhances material efficiency but also contributes to more sustainable manufacturing practices.
Additionally, lost foam casting typically requires fewer steps than conventional casting methods. For instance, the need for pattern making, core making, and other intermediate processes can be significantly reduced. This streamlining of production processes leads to shorter lead times and lower manufacturing costs, making lost foam casting an attractive option for businesses aiming to improve their bottom line.
lost foam casting foundry
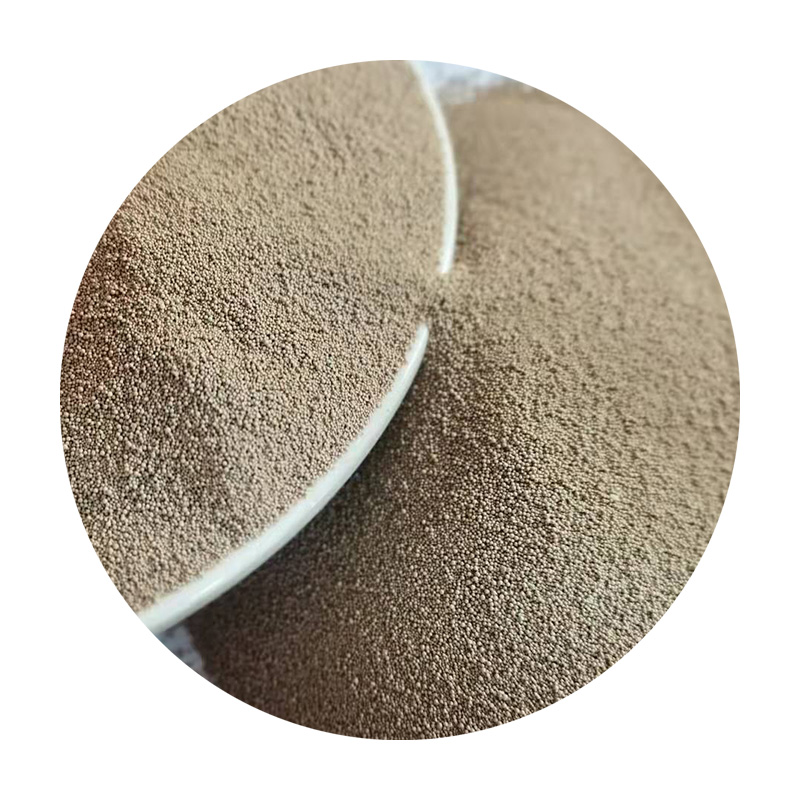
Applications and Industries
Lost foam casting is widely used in various industries, including automotive, aerospace, and heavy machinery. The process is particularly valuable for the production of engine blocks, brackets, and other components requiring high dimensional accuracy and surface integrity. Moreover, its capability to cast larger and more intricate parts makes it an ideal choice for sectors where lightweight yet robust components are critical, such as in the aerospace industry.
In addition to metal parts, some foundries have started to experiment with other materials, expanding the potential applications of lost foam casting. For instance, it has been tested with various ferrous and non-ferrous alloys, broadening its usability across different applications.
Challenges and Future Directions
While the lost foam casting process presents many benefits, it is not without its challenges. One of the primary issues faced by manufacturers is the need for specialized equipment and facilities, which can require significant initial investment. Moreover, controlling the quality of the foam pattern and ensuring proper burnout of the pattern are critical for achieving desired casting results.
Looking towards the future, advancements in materials science and technology are expected to further enhance the capabilities of lost foam casting. Innovations such as improved foam materials and better mold coatings could lead to even more precise and efficient casting processes.
Conclusion
Lost foam casting represents a significant advancement in foundry technology, offering unmatched design flexibility, material efficiency, and cost-effectiveness. As industries continue to seek innovative manufacturing processes, lost foam casting is poised to play a crucial role in shaping the future of metal casting, providing solutions that meet the demanding requirements of modern production environments. With ongoing research and development, this process will likely see increased adoption and further improvements, solidifying its position as a staple in the foundry industry.
Post time:Dek . 19, 2024 00:28
Next:what is sand casting in engineering