Lost Foam Casting An Innovative Approach to Precision Metal Casting
Lost foam casting is a unique and innovative metal casting process that allows manufacturers to produce complex shapes with high precision. This technique, which is a variation of the investment casting method, uses a foam pattern made from polystyrene or other similar materials to create intricate designs in metal. As industries evolve and demand for more complex and lightweight parts increases, lost foam casting has gained popularity across various sectors, including automotive, aerospace, and general manufacturing.
Understanding the Process
The process of lost foam casting begins with creating a foam pattern that resembles the final product. This foam component is often produced using techniques such as CNC machining or molding. The foam pattern is coated with a thin layer of refractory material, such as sand mixed with a bonding agent, which creates a shell around the foam. This layer is crucial for containing the molten metal during the casting process.
Once the pattern is prepared, it is placed in a mold box, and molten metal is poured over the foam pattern. As the metal fills the mold, it simultaneously vaporizes the foam, effectively losing the foam in the process. This vaporization leaves behind a void that takes the shape of the original pattern. The molten metal solidifies rapidly, capturing the fine details and surface finish of the foam pattern. After the metal cools, the remaining sand shell is broken away, revealing the final cast product.
Advantages of Lost Foam Casting
One of the primary advantages of lost foam casting is its ability to produce complex geometries that would be difficult or impossible to achieve with traditional casting methods. The foam patterns can be designed with intricate features, allowing for the creation of parts that are lighter and more efficient. Additionally, the elimination of draft angles and the need for cores simplifies the design process and reduces production costs.
Another significant benefit of this technique is the smooth surface finish it provides. The fine detail of the foam pattern transfers well to the metal, reducing the need for extensive machining or finishing processes. This not only saves time but also allows manufacturers to enhance the aesthetics of their products.
Cost-effectiveness is another reason why lost foam casting is popular. The use of foam patterns minimizes material waste, and since the process allows for rapid production, manufacturers can respond quickly to market demands. Furthermore, the versatility of the process means it can be employed for various metals, including aluminum, iron, and steel, making it suitable for a broad range of applications.
lost foam casting examples
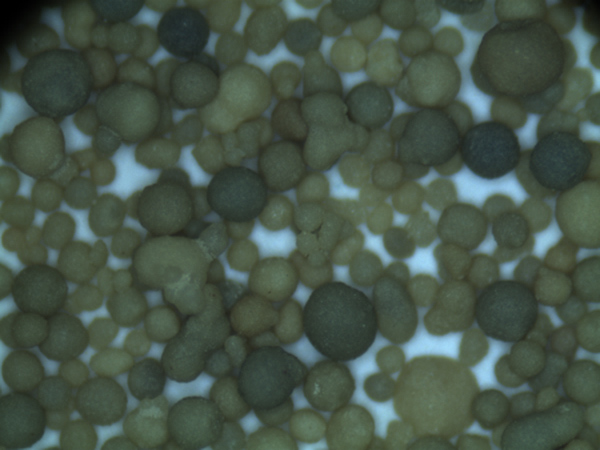
Applications of Lost Foam Casting
Lost foam casting has found applications in various industries due to its versatility and efficiency. In the automotive sector, it is used to create engine blocks, transmission cases, and other critical components that require high precision and complex shapes. As cars become more advanced, the need for lighter and more efficient parts pushes manufacturers towards techniques like lost foam casting.
The aerospace industry also benefits from this casting method, especially in the production of lightweight components that endure extreme conditions. Parts such as brackets, housings, and structural elements can be efficiently produced using lost foam casting, resulting in a significant reduction in weight without compromising strength.
Additionally, the process is gaining attention in the field of art and sculpture, where artists leverage lost foam casting to create intricate metal artworks. The ability to replicate fine details and textures contributes to the uniqueness of each piece.
Challenges and Future Directions
While lost foam casting offers numerous advantages, it is not without its challenges. The process requires careful control of temperature and timing to ensure proper vaporization of the foam and avoid defects in the final product. Additionally, the need for specialized materials and coatings can increase the complexity of the setup.
Despite these challenges, the future of lost foam casting looks promising. As technology advances, improvements in materials and processes are likely to enhance the efficiency and capabilities of this method. Automation and digital design tools can further streamline production processes, allowing for even more complex and precise castings.
In conclusion, lost foam casting represents a significant advancement in metal casting technology. Its ability to produce complex geometries, coupled with cost-effectiveness and high-quality finishes, positions it as a favored method in various industries. As manufacturers continue to seek innovative solutions to meet modern demands, lost foam casting is poised to play a vital role in shaping the future of metal manufacturing.
Post time:Sen . 25, 2024 15:03
Next:3d print sanding