Foundry Sand Casting Process An Overview
Sand casting, also known as foundry casting, is one of the oldest and most versatile metal casting processes used in manufacturing today. This technique involves creating a mold from sand and then pouring molten metal into the cavity to achieve a desired shape. The process is particularly favored for its ability to replicate complex geometries, making it ideal for a wide range of applications in various industries, including automotive, aerospace, and artistic sculpture.
The Basics of Sand Casting
The fundamental steps of the sand casting process include pattern making, mold preparation, pouring, and finishing. 1. Pattern Making The first step involves creating a pattern, which is typically made of metal, plastic, or wood. This pattern represents the final product's shape and is slightly oversized to accommodate the shrinkage that occurs as the metal cools. Patterns can be single-piece or multi-part, depending on the complexity of the design.
2. Mold Preparation Once the pattern is ready, the next step is to prepare the mold. The most commonly used material for molds is sand, primarily because it is abundant, inexpensive, and has a high melting point, making it suitable for molten metal. The sand is mixed with a binder, typically clay, and water. This mixture is compacted around the pattern to form a mold. After the mold is created, the pattern is removed, leaving behind a hollow cavity that matches the desired shape.
foundry sand casting process
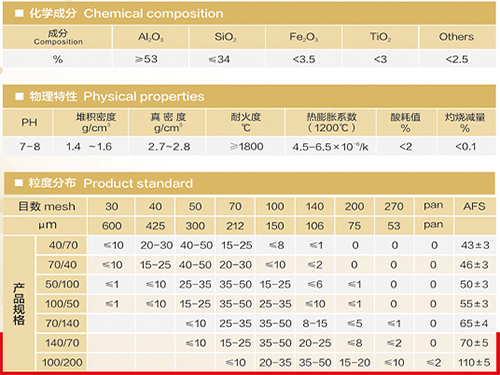
3. Pouring Molten Metal With the mold prepared, the next step involves heating the chosen metal until it reaches a liquid state. The molten metal is then poured into the mold cavity through a system of channels known as gates. It is essential to control the pouring temperature and speed to ensure that the metal fills the mold evenly and reduces the risk of defects.
4. Cooling and Finishing After the metal is poured, it allows sufficient time to cool and solidify within the mold. Once the metal has completely cooled, the mold is broken apart to remove the cast component. The finishing processes, which may include machining, grinding, or surface treatments, are performed to achieve the desired dimensions and surface quality.
Advantages and Applications
The sand casting process boasts several advantages, such as the ability to produce large castings with intricate shapes without requiring extensive processing equipment. This flexibility allows for the production of a wide range of parts, from small components to large industrial pieces. Additionally, sand casting can accommodate almost any metal alloy, including aluminum, iron, and bronze, making it an attractive option for manufacturers.
In summary, the foundry sand casting process is an efficient and economically viable method for producing metal parts. Its simplicity, versatility, and cost-effectiveness have secured its place in the manufacturing landscape, ensuring that it remains a preferred choice for various industries. As technology advances, enhancements in mold design and material properties continue to improve the quality and precision of sand-cast components, further solidifying its relevance in modern manufacturing processes. Whether for producing prototypes or final products, sand casting serves as a critical method in the art of metalworking.
Post time:Avq . 30, 2024 08:51
Next:What is Sand Casting in Engineering? | Process, Applications, and Benefits