Difference Between Sand Casting and Die Casting
Casting is a fundamental manufacturing process used to create metal parts and components through pouring molten material into a mold. Among the various casting methods available, sand casting and die casting are two of the most popular techniques, each possessing unique characteristics, advantages, and applications. Understanding the differences between these two methods is essential for manufacturers when choosing the appropriate technique for their specific needs.
Sand Casting Overview
Sand casting is one of the oldest and most versatile methods of casting. It involves creating a mold from a mixture of sand, clay, and water. The main components of sand casting include
1. Pattern A replica of the final product is created, typically made of wood, metal, or plastic. 2. Mold The pattern is pressed or formed into sand to create a mold cavity. 3. Core If the casting requires internal features, a core made of sand is added. 4. Pouring Molten metal is poured into the mold cavity and allowed to solidify.
Die Casting Overview
Die casting, on the other hand, is a more modern technique that involves forcing molten metal under high pressure into a mold cavity. The molds used in die casting are made of steel and can be reused many times, providing high precision and excellent surface finish. Key components of die casting include
1. Die The mold, typically made of two halves, which can be opened after the metal solidifies. 2. Injection System A mechanism that injects molten metal into the die at high pressure. 3. Cooling System Circulates coolant to hasten the cooling and solidifying process of the metal.
Key Differences
difference between sand casting and die casting
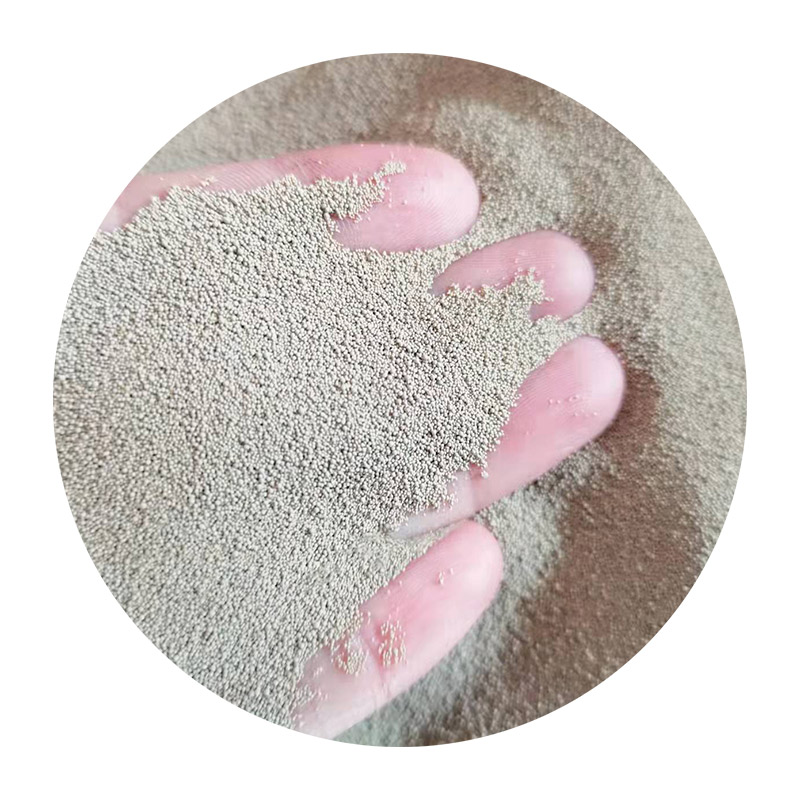
1. Material Types - Sand casting can accommodate a wide range of metals, including aluminum, bronze, cast iron, and magnesium. - Die casting is generally limited to non-ferrous metals, primarily aluminum, zinc, copper, and magnesium alloys.
2. Production Volume - Sand casting is more suitable for low to medium production volumes. It is an economical choice for prototypes and custom parts. - Die casting excels in high-volume production. The upfront costs are higher due to the need for durable dies, but costs per part decrease significantly with large quantities.
3. Mold Preparation - In sand casting, the molds are created each time from sand, which is labor-intensive and time-consuming. - Die casting molds are permanent and expensive but can produce thousands or even millions of parts with minimal variation in dimensions.
4. Precision and Surface Finish - Sand casting typically produces thicker walls and has a rougher surface finish, which may require additional machining or finishing processes. - Die casting achieves tighter tolerances and smoother surfaces directly from the production process, often requiring less post-casting work.
5. Rate of Production - Sand casting has a slower production rate due to the necessary time for mold creation, pouring, and cooling. - Die casting allows for rapid production cycles, which is advantageous for high-demand manufacturing scenarios.
Applications
The distinct characteristics of sand and die casting lead to their use in different applications. Sand casting is prominent in automotive parts, large engineering components, and custom designs where intricate shapes are required. Alternatively, die casting is widely utilized for high-volume production of parts in the automotive industry, electronic housings, and household appliances where uniformity and detail are crucial.
Conclusion
In summary, the choice between sand casting and die casting largely hinges on the production volume, design requirements, and material type. Understanding these differences allows manufacturers to select the best casting method for their specific applications, ensuring efficient production and high-quality outcomes. As technology advances, both methods continue to evolve, enhancing their capabilities and expanding their range of applications in the manufacturing landscape.
Post time:Noy . 07, 2024 22:06
Next:Affordable Options for 3D Sand Printers in Today's Market