The Role of Sand in Sand Casting Types and Their Importance
Sand casting, a widely used manufacturing process, is known for its versatility and cost-effectiveness, especially when producing complex metal components. One of the critical factors that influence the quality of sand castings is the type of sand used in the process. There are several types of sand, each offering distinct properties that affect the casting characteristics. This article explores the various types of sand used in sand casting and their significance.
1. Silica Sand
Silica sand is perhaps the most commonly used type of sand in the sand casting industry. Composed mainly of silicon dioxide (SiO2), silica sand is available in various grades, which reflect the particle size and distribution. Its high melting point, granule stability, and availability make it an ideal choice for a wide range of casting applications. Silica sands can withstand high temperatures often exceeding 1,500°C, making them suitable for casting ferrous and non-ferrous metals alike.
However, silica sand has its drawbacks, primarily concerning safety. The fine particles can produce silica dust, which is a health hazard, leading to respiratory issues for workers. As such, adequate ventilation and protective equipment are necessary to mitigate these risks.
2. Green Sand
Green sand is not a specific type of sand but a mixture of silica sand, clay, and moisture. Its name comes from its moisture content, which gives it a greenish appearance when molded. The clay, often bentonite, acts as a binding agent, providing the sand with plasticity. Green sand is widely used for sand casting due to its ability to produce intricate shapes and good surface finish. Moreover, it’s cost-effective and recyclable, making it an attractive option for foundries.
One of the key advantages of green sand is its ability to retain moisture, which helps in the molding process
. However, the presence of moisture can also complicate the drying procedure, requiring careful handling to avoid defects in the final casting.what type of sand is used in sand casting
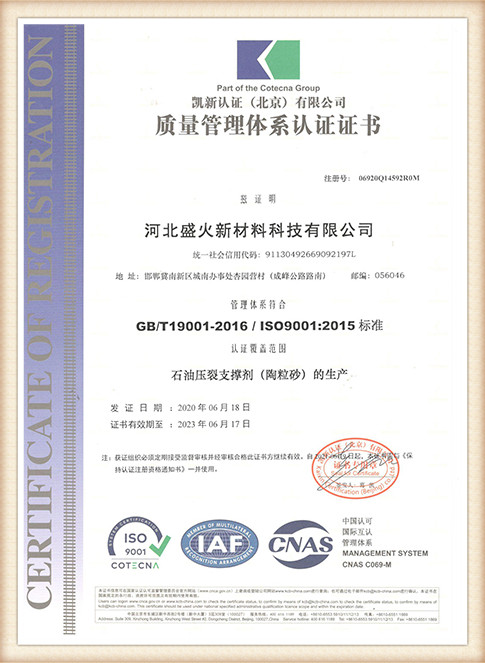
3. Resin Sand
Resin sand is a mixture of silica sand and synthetic resin, used primarily in precision casting applications. The resin is activated by a hardening agent, which binds the sand grains together more effectively than traditional clay. This results in stronger molds that can withstand higher temperatures, reducing the likelihood of defects such as warping or cracking during the casting process.
The primary advantage of resin sand is its ability to produce high-quality finishes and complex geometries with excellent dimensional accuracy. However, it typically involves higher costs and requires proper ventilation during the curing process, as the resins can emit harmful fumes.
4. Shell Sand
Shell sand is another advanced material used in sand casting. Made by coating fine sand with thermosetting resin, it is used to create thin-walled molds. The process involves preheating metal patterns and then applying a layer of the coated sand, resulting in very smooth surfaces and precise dimensions. Shell sand molds are designed for high-volume production and are particularly effective when casting small components that require intricate detailing.
Like resin sand, shell sand comes with increased costs but offers superior casting qualities.
Conclusion
In conclusion, the type of sand used in sand casting significantly influences the quality and efficiency of the casting process. While silica sand remains the industry standard, alternatives such as green sand, resin sand, and shell sand offer various benefits tailored to specific applications. Foundries must carefully select the appropriate sand type based on their production requirements, material specifications, and cost considerations. By understanding the properties and applications of different sands, manufacturers can optimize their casting processes, ultimately leading to improved product quality and reduced production costs.
Post time:ديسمبر . 10, 2024 21:15
Next:Innovative Approaches to Lost Foam Casting Techniques in Modern Manufacturing