Understanding the Sand Casting Process
The sand casting process is one of the most widely used manufacturing techniques in foundries around the world. It involves the creation of metal castings by pouring molten metal into a sand mold, allowing it to solidify into the desired shape. This method is particularly favored due to its versatility, cost-effectiveness, and ability to create complex geometries. Let's explore the sand casting process in detail, covering its steps, applications, advantages, and disadvantages.
Steps in the Sand Casting Process
1. Pattern Making The first step in the sand casting process is creating a pattern, which is an exact replica of the final product. Patterns are typically made from materials such as wood, metal, or plastic. The choice of material often depends on the size and complexity of the part. The pattern should also account for shrinkage of the metal as it cools.
2. Mold Preparation Once the pattern is made, the next step involves creating the mold. This is achieved by packing sand around the pattern to form a mold cavity. The sand used in this process is often mixed with a binding agent to help it maintain its shape. After packing the sand, the pattern is removed, leaving behind a cavity that represents the part to be cast.
3. Melting the Metal The metal to be cast (such as aluminum, iron, or bronze) is then melted in a furnace. The choice of metal will depend on the required properties of the final product. The molten metal needs to be heated to a specific temperature to ensure it flows easily into the mold.
4. Pouring After the metal has reached the proper temperature, it is poured into the mold through a gating system. This system directs the flow of molten metal and helps fill the mold cavity completely. It is crucial to pour the metal in a controlled manner to avoid creating defects.
5. Cooling Once the mold has been filled, the molten metal is allowed to cool and solidify. The cooling time can vary based on the size of the casting and the type of metal used. Proper cooling is essential to ensure even solidification and minimize defects such as warping.
6. Mold Removal After the metal has solidified, the sand mold is broken away to reveal the cast metal object. This process is often done gently to avoid damaging the casting.
what is sand casting process
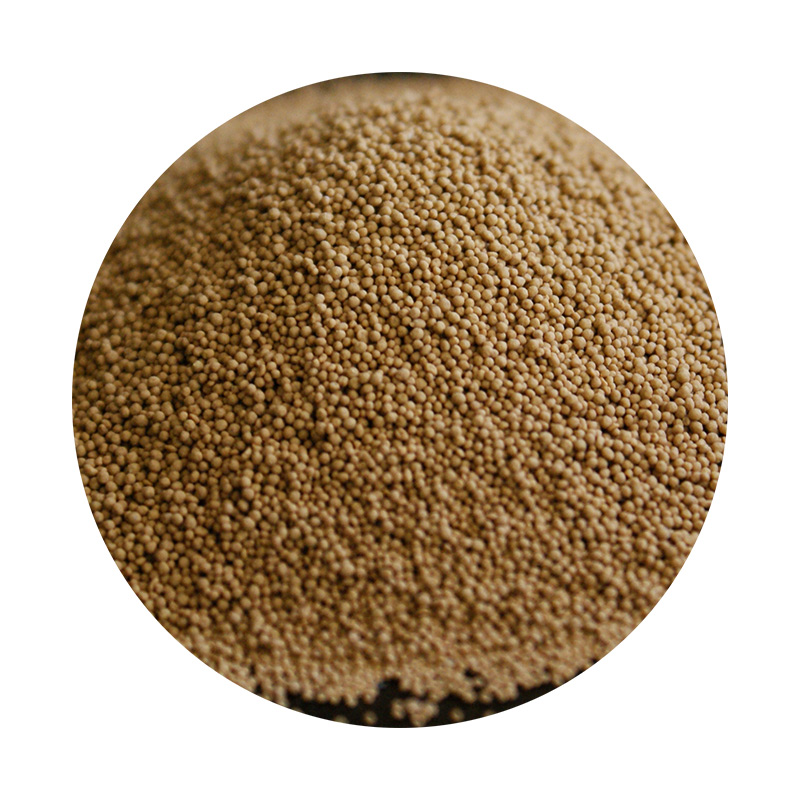
Applications of Sand Casting
Sand casting is utilized in various industries, including automotive, aerospace, and machinery manufacturing. It is commonly used to produce engines, pumps, valves, and various components that require significant durability and strength. The process is also prevalent for creating artistic pieces, sculptures, and decorative elements due to its capability to produce intricate designs.
Advantages of Sand Casting
- Versatility Sand casting can accommodate various metal types and allows for the casting of large and complex shapes. - Cost-Effectiveness The materials used for sand casting are relatively inexpensive, and the process does not require expensive molds, making it ideal for small to medium production runs. - Ease of Modification Patterns and molds can be easily altered, allowing for quick adjustments in design.
Disadvantages of Sand Casting
- Surface Finish The surface finish of sand cast products may not be as smooth as those produced by other casting methods, requiring additional finishing work. - Dimensional Tolerances While sand casting can produce complex shapes, the dimensional tolerances may not be as precise as those achieved through other methods like die casting. - Labor-Intensive The process can be labor-intensive, particularly in the pattern-making and mold preparation stages.
Conclusion
The sand casting process remains a fundamental and widely used manufacturing technique, known for its simplicity and effectiveness in producing a diverse range of components. Despite some limitations in surface finish and precision, its advantages in terms of cost, versatility, and ease of adaptation make it an indispensable process in modern manufacturing. Whether used for industrial applications or artistic creations, sand casting continues to play a significant role in shaping the products we rely on every day.
Post time:ديسمبر . 05, 2024 03:00
Next:Different Types of Sand Used in Foundry Applications and Their Characteristics