Understanding Types of Sand Casting Processes
Sand casting is one of the oldest and most widely used metal casting processes in which sand is utilized to create molds for metal casting. It plays a pivotal role in various manufacturing sectors, allowing for the production of complex shapes and large components. This article delves into the various types of sand casting processes and their unique characteristics.
1. Green Sand Casting
Green sand casting is the most common type of sand casting process. It utilizes a mixture of sand, clay, and water to create molds. The term green refers to the moisture content in the mixture, which gives it a greenish hue. This method is favored for its simplicity and cost-effectiveness. In green sand casting, the sand mold is formed around a pattern of the desired shape, and once the metal is poured in, the mold hardens as it dries. Green sand molds can be reused multiple times, making this an efficient option for foundries.
In contrast to green sand casting, dry sand casting utilizes sand that's been chemically bonded and dried, resulting in a stronger mold. The primary advantage of this process is the higher dimensional accuracy and surface finish it offers compared to green sand casting. Dry sand molds can withstand higher temperatures and are ideal for casting alloys with low melting temperatures. While this process is more expensive due to the additional steps required to cure the mold, it is often preferred when quality and precision are paramount.
3. No-Bake Sand Casting
types of sand casting process
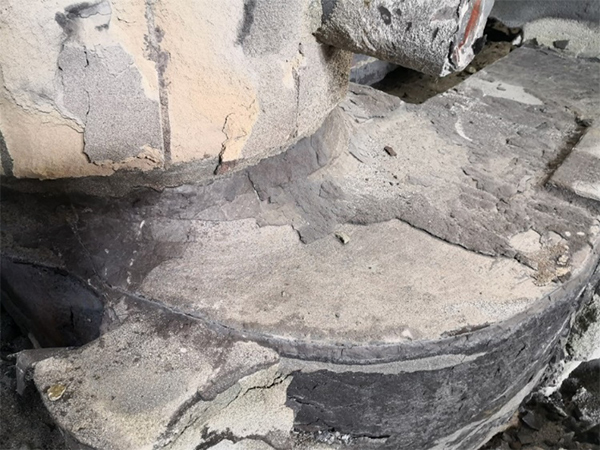
No-bake sand casting, also known as air-set sand casting, involves a mixture of sand and a resin binder that hardens at room temperature. This process does not require any baking or drying, hence the name. The molds are created by compacting the sand-resin mixture around the pattern, and once set, the mold is ready for metal pouring. No-bake casting is ideal for producing intricate shapes and is often used in the manufacturing of complex components that require a high level of detail.
4. Shell Mold Casting
Shell mold casting is a variation of sand casting that uses a thin shell of sand and resin to form molds. The mold is created by introducing the mixture into a heated metal pattern, which causes the resin to cure and form a hard shell around it. This technique is known for producing parts with excellent surface finishes and high dimensional accuracy, making it suitable for precision applications, such as in the automotive and aerospace industries. The main drawback of shell mold casting is the higher cost associated with the resin and the metal patterns.
5. Investment Casting with Sand
Although traditionally, investment casting uses wax patterns, sand can also play a role in this process. In this hybrid method, a shell or coating of sand is applied to the wax pattern before the investment process. Once the mold is created and the wax is melted away, molten metal is poured into the sand shell. This technique combines the best attributes of both sand and investment casting, offering high accuracy and a fine surface finish.
Conclusion
Sand casting processes are versatile and widely employed in various manufacturing applications. Each type, from green sand casting to shell mold casting, offers unique advantages and considerations, making it essential for manufacturers to choose the appropriate type based on their specific requirements—be it cost, precision, or complexity. As technology progresses, the sand casting industry continues to innovate, enhancing efficiencies and expanding the range of potential applications. Understanding these processes is vital for anyone involved in manufacturing or materials engineering.
Post time:نوفمبر . 10, 2024 07:26
Next:Understanding the Process and Benefits of Sand Casting in Metal Fabrication