Understanding Sand Used for Sand Casting
Sand casting is one of the oldest and most widely used manufacturing processes in the foundry industry. This traditional method of metal casting entails pouring molten metal into a prepared mold made primarily from sand. The choice of sand is critical to the end product’s quality, finish, and dimensional accuracy. In this article, we will explore the types of sand used for sand casting, their properties, and the factors that influence their selection.
Types of Sand Used in Sand Casting
The most commonly used sand in sand casting is silica sand due to its high melting point, availability, and cost-effectiveness. Silica sand is composed mainly of silicon dioxide (SiO2) and is preferred for its excellent thermal properties. Other types of sand that may be utilized include
1. Green Sand This is a mixture of silica sand, clay, and water. The clay acts as a binder and helps retain moisture, giving the sand its green designation. Green sand molds are known for their strength and ability to produce intricate castings with a good surface finish.
2. Dry Sand Unlike green sand, dry sand is a sand mixture that has been baked and does not contain moisture. This type of sand is often used when precision is required, as it leads to better dimensional control and a smoother finish.
3. Resin Sand This sand is mixed with a resin binder that hardens when heated, resulting in a strong mold that can withstand higher temperatures. Resin sand is ideal for intricate and high-precision castings, often used in the automotive and aerospace industries.
4. Shell Molding Sand This involves a mixture of fine sand and thermosetting resin. The sand is heated in a mold to create a thin shell, resulting in excellent surface detail and dimensional accuracy. This method is particularly useful for complex shapes.
Key Properties of Foundry Sand
The effectiveness of sand in the casting process is largely determined by its properties
- Grain Size The grain size of sand impacts the smoothness of the final casting. Smaller grains yield a finer surface finish, while larger grains may lead to a rougher surface. A balanced grain size is crucial for achieving the desired finish and strength.
sand used for sand casting
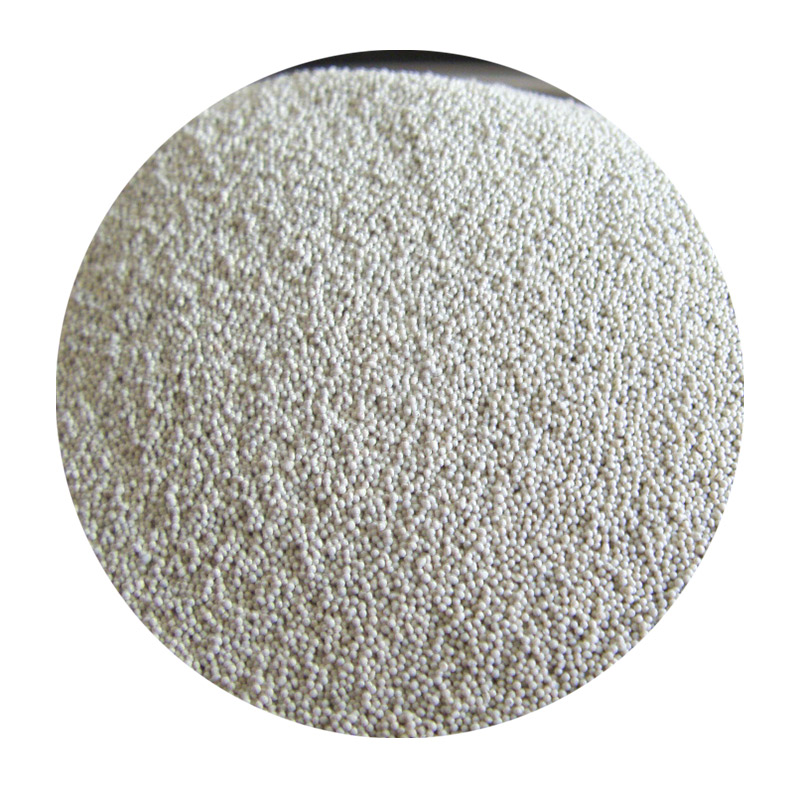
- Shape and Sphericity The shape of the sand grains affects how they pack together. Well-rounded grains provide better flow and packing characteristics. Angular grains, on the other hand, can provide better strength and support for the mold.
- Permeability Permeability refers to the sand's ability to allow gases to escape during the pouring of molten metal. Sands that are too dense may cause blowholes in the casting, while overly permeable sands may lead to a weak mold.
- Thermal Stability The ability of sand to withstand high temperatures without degrading is crucial. Sand must maintain its integrity under extreme heat to prevent mold collapse or defects in the casting.
Factors Influencing Sand Selection
Several factors play a critical role in determining which type of sand is best suited for a particular casting project
1. Type of Metal Being Cast Different metals and alloys have varying melting points and characteristics that can influence which sand type is appropriate.
2. Complexity of Design More intricate designs may require finer sands or resin sand to achieve the desired accuracy and surface finish.
3. Production Volume For large-scale production, cost-effectiveness becomes a key consideration. Green sand is often preferred in such cases; however, for smaller batches and precise parts, resin sand might be more advantageous despite a higher cost.
4. Environmental Factors The environmental impact of different sands must also be considered. Some foundries are moving toward more sustainable options, including recycled sands.
In conclusion, the selection of sand for sand casting is a complex decision that requires careful consideration of various factors, including the type of metal being cast, the complexity of the design, and production requirements. Understanding the properties and types of sand used can ultimately enhance the quality and performance of cast metal products. With ongoing advancements in materials and technologies, the future of sand casting looks promising, engaging a balance between tradition and innovation.
Post time:سبتمبر . 23, 2024 10:49
Next:鋳造用サンドの特性と応用について説明する