Sand Printing Casting Revolutionizing the Foundry Industry
Sand printing casting is an innovative manufacturing process that merges traditional sand casting with modern 3D printing technology. This method has transformed the way foundries operate, offering enhanced precision, reduced waste, and increased design flexibility. As industries seek to optimize production processes and meet the demands of custom manufacturing, sand printing casting emerges as a crucial tool that is changing the landscape of metal casting.
The Basics of Sand Casting
Traditionally, sand casting involves creating a mold from a pattern, usually made of metal or wax. The pattern is placed in a sand mixture, forming a mold cavity. Once the mold is created, molten metal is poured into the cavity to produce a desired part. While this method has been employed for centuries, it does have its limitations, particularly in terms of complexity and lead times. Patterns must be made for each unique part, which can be time-consuming and costly, particularly for small production runs or highly customized parts.
The Introduction of 3D Printing
The advent of 3D printing technology has significantly changed the manufacturing landscape across multiple industries. In the context of sand casting, 3D printing allows for the creation of molds directly from digital models. This means that foundries can produce molds with far greater complexity and precision than ever before. Instead of relying on traditional patterns, manufacturers can print intricate designs that would be impossible or prohibitively expensive to create using conventional methods.
Advantages of Sand Printing Casting
1. Design Flexibility One of the most significant advantages of sand printing casting is the ability to create highly complex geometries. Designers can push the boundaries of what is possible, allowing for innovative product designs that enhance performance and reduce weight.
2. Reduced Lead Times With the elimination of traditional pattern making, the time required to produce molds is drastically reduced. This acceleration in production enables companies to respond quickly to market demands and reduces the overall time to market for new products.
sand printing casting
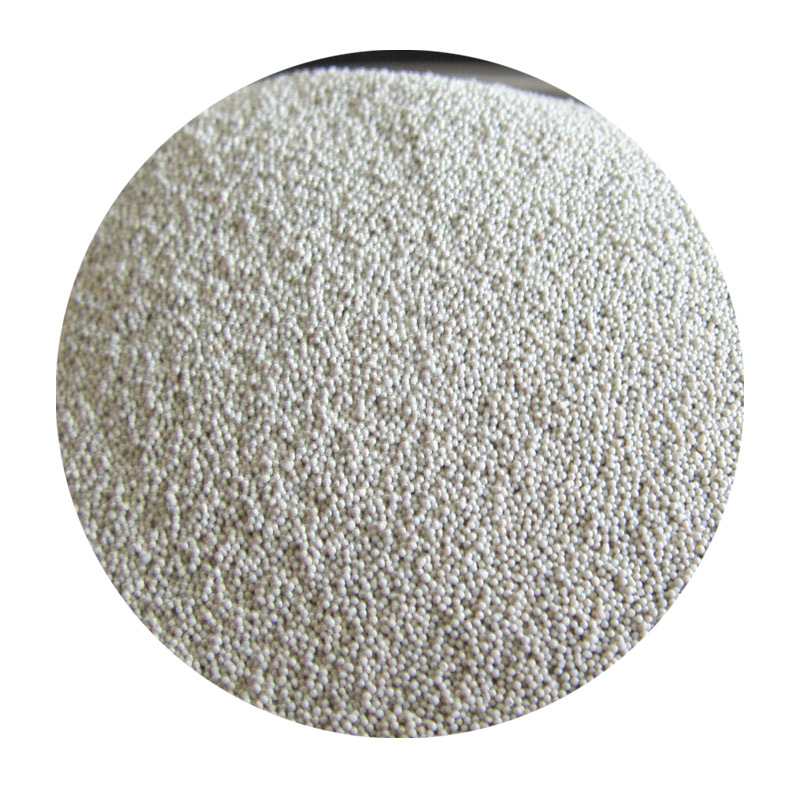
3. Cost-Effectiveness Although the initial investment in 3D printing technology can be substantial, the overall costs tend to decrease due to the reduction in material waste and the ability to produce custom parts without the need for extensive tooling alterations. This is particularly advantageous for low-volume production runs, where traditional methods may not be cost-effective.
4. Sustainability Sand printing casting is inherently more sustainable than traditional methods. As 3D printing technology allows for better control over material use, it minimizes excess waste, contributing to a more sustainable manufacturing process. Additionally, the materials used in sand printing are often recyclable, further enhancing its environmental credentials.
5. Enhanced Precision The high level of precision achievable with 3D printing minimizes the need for secondary machining operations, which can save time and resources. This precision is critical in industries where tolerances are tight, such as aerospace and automotive sectors.
Applications Across Industries
Sand printing casting has found applications in various industries, including automotive, aerospace, healthcare, and art. In the automotive sector, manufacturers can produce custom parts that enhance vehicle performance while simultaneously reducing weight. In the aerospace industry, where precision and weight-saving are paramount, sand printing casting allows for the production of lightweight components that meet strict regulatory standards.
Moreover, in the medical field, custom prosthetics and implants can be manufactured using sand printing casting, tailored to fit individual patients accurately. Artists and designers also use this technology to create intricate sculptures and installations that were previously limited by traditional casting methods.
Conclusion
As technology continues to advance, sand printing casting stands out as a transformative process that combines the efficiency of 3D printing with the established advantages of sand casting. Its ability to produce complex designs more rapidly and sustainably makes it an attractive option for manufacturers facing the challenges of modern production. Whether for automotive components, aerospace parts, medical devices, or artistic creations, sand printing casting is paving the way for a more innovative and efficient future in manufacturing. As this technology continues to evolve, it will undoubtedly further redefine the capabilities of the foundry industry and beyond.
Post time:نوفمبر . 30, 2024 03:05
Next:Applications and Advantages of Sand Casting in Modern Manufacturing Processes