Understanding Sand Casting Resins A Comprehensive Guide
Sand casting, a time-honored method in the foundry industry, involves creating metal objects by pouring molten metal into a mold made of sand. One of the critical advancements in this field is the development of sand casting resins, which have significantly improved the efficiency, precision, and quality of castings. This article aims to delve into the various aspects of sand casting resins, including their composition, benefits, applications, and best practices.
What are Sand Casting Resins?
Sand casting resins are synthetic organic compounds used to bind sand particles together to form a mold. Unlike traditional green sand, which relies on moisture to maintain cohesion, resin-bonded sand molds provide greater strength and durability. The most common types of resins used in sand casting include phenolic, urethane, and epoxy resins. These materials are mixed with sand and typically cured by heat or a chemical reaction, forming a rigid mold that can withstand the high temperatures of molten metal.
Advantages of Using Sand Casting Resins
1. Enhanced Strength and Durability Resin-bonded molds exhibit superior mechanical properties compared to traditional sand molds. They retain their shape under high temperatures and pressures, reducing the risk of mold collapse during the casting process.
2. Dimensional Accuracy The precision of resin molds allows for tighter tolerances and detailed surface finishes. This characteristic is particularly beneficial in industries requiring complex shapes or intricate designs.
3. Reduced Environmental Impact Many modern sand casting resins are designed to minimize harmful emissions, making them more environmentally friendly than traditional methods. The reduction in volatile organic compounds (VOCs) helps improve air quality and workplace safety.
4. Efficiency in Production The curing times for resin molds are often shorter than those for traditional sand molds, allowing for faster turnaround times and increased production rates.
5. Versatility Sand casting resins can be formulated to suit a variety of applications, from automotive components to artistic sculptures. Their ability to adapt to different casting processes makes them a preferred choice in many industries.
Applications of Sand Casting Resins
sanding casting resin
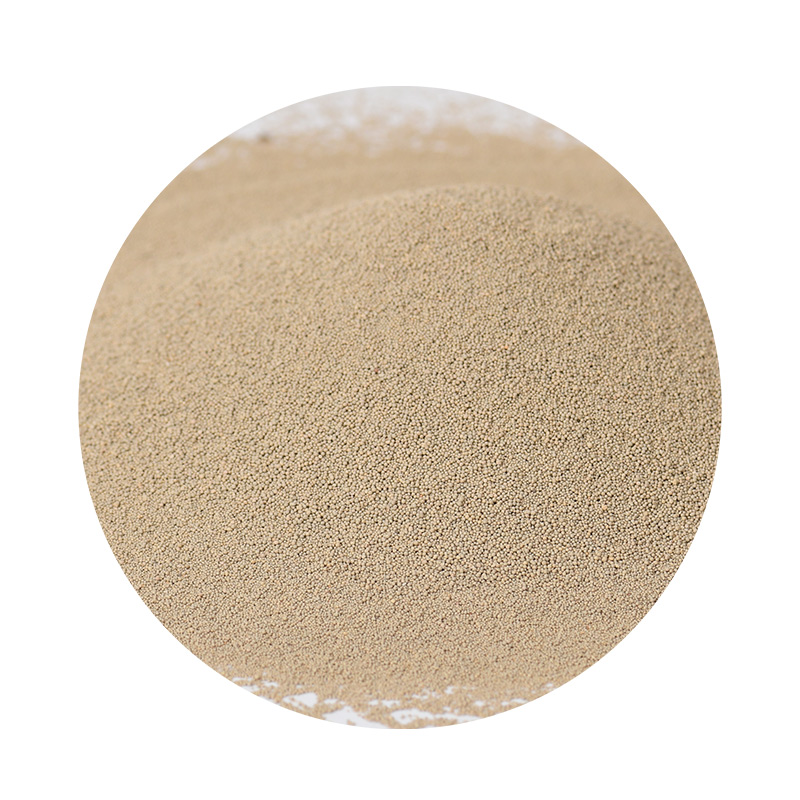
Sand casting resins are used across numerous sectors, each benefiting from the unique properties of resin-bonded molds. Some common applications include
- Automotive Industry The production of engine blocks, transmission housings, and various other components is often achieved using sand casting resins to meet stringent performance requirements. - Aerospace Lightweight and high-strength components are critical in aerospace applications. Resin-bonded molds can produce complex shapes that meet the rigorous standards of this industry. - Art and Sculptures Artists and sculptors utilize resin-bound sand casting to create detailed and durable art pieces that often require intricate designs.
- Heavy Equipment Components for machinery and equipment used in construction, mining, and agriculture are regularly produced using sand casting resins, ensuring durability and robust performance
.Best Practices in Using Sand Casting Resins
To maximize the benefits of sand casting resins, it is essential to follow best practices
1. Proper Mixing Accurate mixing of resin with sand is crucial for achieving the desired properties. Follow the manufacturer’s specifications for ratios and ensure thorough blending.
2. Controlled Curing Conditions Monitor the curing conditions carefully. The temperature and humidity can significantly affect the final properties of the mold.
3. Quality Control Regular testing of the molds for strength, dimensional accuracy, and surface finish is vital. Implementing a quality control system can help identify potential issues early in the casting process.
4. Safety Measures Since working with resins can involve exposure to harmful substances, ensure that adequate ventilation, protective gear, and safety protocols are in place to safeguard workers.
Conclusion
Sand casting resins represent a significant advancement in foundry technology, offering a wide range of benefits over traditional methods. Their strength, precision, and versatility make them an excellent choice for various applications, from automotive to artistic endeavors. By understanding their characteristics and adhering to best practices, manufacturers can leverage sand casting resins to enhance production efficiency and improve the quality of their cast products. As industries continue to evolve, the role of sand casting resins will undoubtedly become more prominent, pushing the boundaries of what is possible in metal casting.
Post time:أكتوبر . 22, 2024 10:17
Next:Understanding Tolerances in Sand Casting for Improved Precision and Quality Control