Understanding Sand Types in Sand Casting
Sand casting is one of the oldest and most versatile casting processes in the manufacturing industry. It involves creating metal parts by pouring molten metal into a mold made from sand. The choice of sand type is critical to the success of the casting process, as it affects the quality of the final product, the ease of mold production, and the overall efficiency of the operation. In this article, we’ll explore the various types of sands used in sand casting and their unique properties.
1. Silica Sand
Silica sand is the most commonly used sand in sand casting. It comprises mostly of silicon dioxide (SiO2), and its availability makes it a cost-effective choice. Silica sand has excellent thermal stability, which allows it to withstand the high temperatures of molten metal without breaking down. Additionally, it has good permeability, allowing gases to escape during the pouring process, which reduces the risk of defects in the final casting. The grain size and shape of silica sand can vary, and this variability can influence the surface finish and dimensional accuracy of the cast product.
2. Green Sand
Green sand is a mixture of silica sand, clay, and water. It is called green because it is used in a moist state, not because of its color. The clay component acts as a binder, which helps the sand retain its shape during the casting process. Green sand molds are generally easy to produce, making them popular for both small batch and large volume production. However, this type of sand does not perform well at high temperatures, so it is typically used for casting iron and non-ferrous metals.
3. Resin-Sand
sand casting sand types
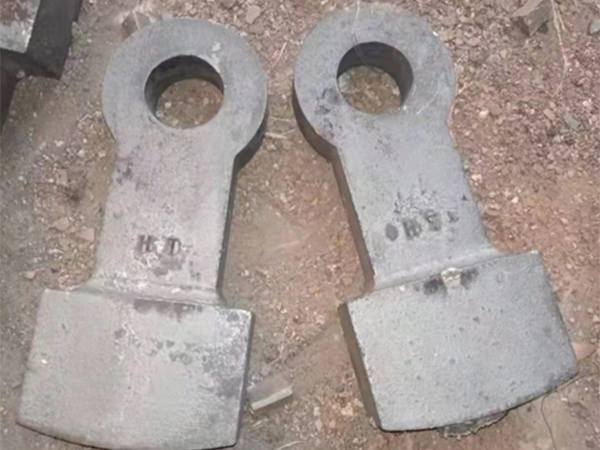
Resin-sand is created by mixing sand with a resin binder. This type of sand can produce very accurate and high-quality molds due to the resin's added strength and rigidity. Resin-sand molds can withstand higher temperatures than green sand and can yield better surface finishes. However, the use of resin-sand can be more expensive, and the curing process requires additional time and energy, which can impact production efficiency.
4. Clay-Sand
Clay-sand, often referred to as oil sand, is a mixture of sand, clay, and oil. This combination results in a malleable material that can be shaped easily. Clay-sand molds are known for their high resistance to thermal shock and are often used in applications requiring intricate designs. The oil content also adds a degree of moisture retention, although it can be more challenging to work with compared to other sand types due to its sticky nature.
5. Zircon Sand
Zircon sand is utilized in high-temperature applications, particularly for casting metals that require superior surface finishes and dimensional accuracy. Zircon has a high melting point and excellent thermal stability, making it suitable for more demanding casting processes. However, zircon sand is significantly more expensive than typical silica sand, and its use is often limited to specialized applications.
Conclusion
Choosing the right type of sand for casting is crucial to the overall success of the process. Each type of sand comes with its own benefits and limitations, and understanding these properties can help manufacturers select the most appropriate material for their specific needs. Whether it's the commonly used silica sand or the more specialized zircon sand, the quality of the sand directly impacts the final product’s integrity and performance.
Post time:نوفمبر . 19, 2024 22:27
Next:what is sand casting used for