Sand Casting Manufacturing Process An Overview
Sand casting, an age-old manufacturing process, remains one of the most widely used methods for producing metal parts today. Its popularity stems from its simplicity, cost-effectiveness, and versatility, allowing for the creation of complex geometries in various materials. This article provides an overview of the sand casting manufacturing process, its key components, and its applications.
The sand casting process begins with the creation of a mold. The mold is typically made of a mixture of sand, clay, and water, which is shaped into the desired form of the final product. The sand used in this process is usually silica sand due to its high melting point and ability to withstand the rigors of molten metal. Once the sand mixture is prepared, it is compacted around a pattern, which mimics the shape of the desired part. The pattern can be made from various materials, such as metal, plastic, or wood.
After the mold is formed, the next step involves removing the pattern to create a cavity where the molten metal will be poured. The mold is designed with a sprue, pouring basin, and riser to facilitate metal flow and to allow for the release of gases that may be trapped during the pouring process. It is crucial to ensure that the mold is properly ventilated to prevent defects in the final casting.
Once the mold is prepared, the selected metal alloy is heated to its liquid state and then poured into the mold cavity. Common materials used in sand casting include aluminum, iron, zinc, and bronze. The molten metal is allowed to cool and solidify, taking on the shape of the mold. The cooling time depends on various factors, such as the size and thickness of the casting and the type of metal used.
sand casting manufacturing process
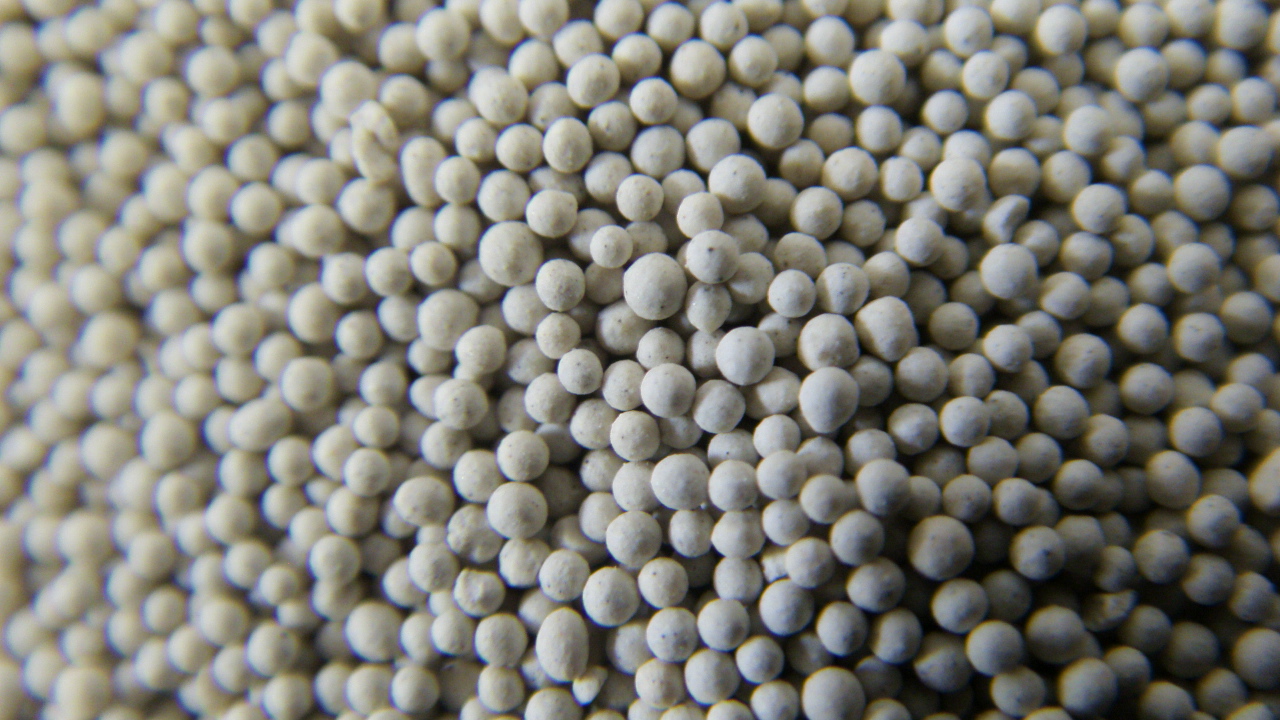
After the metal has cooled and solidified, the mold is broken away, revealing the cast part. This phase requires care to avoid damaging the newly formed component. The sand used in the mold can often be reclaimed and reused, making the process environmentally friendly and cost-effective.
Post-casting operations typically follow, which may include trimming excess material, machining for tighter tolerances, and surface finishing to achieve the desired aesthetic and functional properties. These steps ensure that the final product meets the specifications required for its intended application.
Sand casting is widely used across various industries, including automotive, aerospace, and manufacturing, due to its ability to produce both small and large components efficiently. It is particularly advantageous for low-to-medium production runs, where its flexibility in design and material selection becomes a significant benefit.
In conclusion, the sand casting manufacturing process is a foundational technique that combines simplicity and effectiveness. Its ability to create complex parts at an affordable cost continues to make it a favored choice for manufacturers worldwide. As technology advances, innovations in sand casting techniques promise to enhance its capabilities, ensuring its relevance in the future of manufacturing.
Post time:سبتمبر . 22, 2024 11:56
Next:ceramic sanding discs