Sand casting, also known as sand molded casting, is one of the oldest and most versatile metal casting processes. This method primarily involves the use of sand as the mold material, which allows for the production of intricate shapes and components in various sizes. It has been widely adopted in numerous industries, including automotive, aerospace, and manufacturing, due to its cost-effectiveness and flexibility.
The sand casting process begins with the creation of a pattern, which is a replica of the final product. Patterns can be made from various materials, including wood, metal, or plastic, and are designed to be slightly larger than the final component to accommodate for material shrinkage during cooling. After the pattern is prepared, it is placed in a box called a flask, which is filled with a mixture of sand and a binding agent, usually clay or resin. The sand is compacted around the pattern to form the mold.
Once the mold is formed, the pattern is removed, leaving a cavity that precisely matches the shape of the desired object. This cavity is then filled with molten metal, which is poured from a furnace at high temperatures. The metal fills the mold, taking on its shape as it cools and solidifies. After sufficient cooling time, the sand mold is broken apart, and the casting is removed. The final product may require additional finishing processes, such as sanding, machining, or painting, to achieve the desired surface quality and dimensions.
sand casting
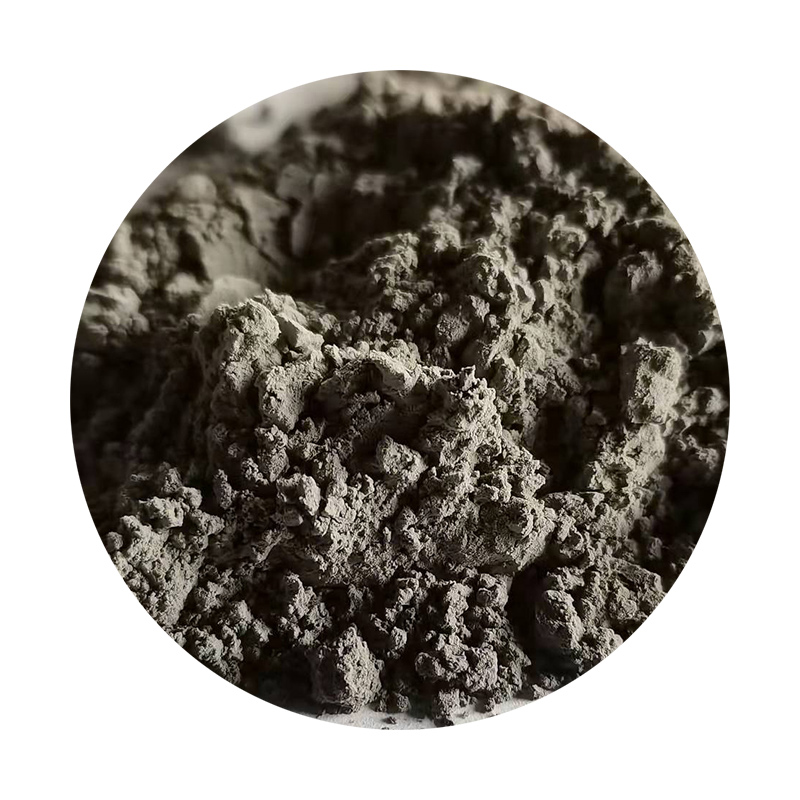
One of the significant advantages of sand casting is its ability to produce complex geometries that would be difficult or impossible to achieve with other manufacturing processes
. Additionally, the material used in sand casting is readily available and inexpensive, making it an attractive option for both small-scale and large-scale production runs.However, sand casting does have its limitations. For instance, the surface finish of sand cast components may not be as smooth as those produced by other methods, and adjustments may be needed for precise tolerances. Furthermore, the casting process can be slower than other techniques like die casting due to the time required for the mold preparation and cooling.
In conclusion, sand casting remains a fundamental method in metalworking, offering a combination of versatility and cost-effectiveness. As technologies advance, innovations in materials and processes continue to enhance its capabilities, ensuring its relevance in modern manufacturing.
Post time:نوفمبر . 06, 2024 20:39
Next:Manufacturing Process of Resin-Coated Sand for Enhanced Casting Applications