The Art and Science of Sand Casting
Sand casting, one of the oldest and most versatile methods of metal casting, has played a vital role in various industries for centuries. This process involves creating a mold from a mixture of sand, a bonding agent, and water, which is then filled with molten metal to form a desired shape. Its simplicity, cost-effectiveness, and efficiency make sand casting a preferred method for producing complex metal parts in large quantities.
The Sand Casting Process
The sand casting process begins with the preparation of the mold. The primary material, sand, is typically mixed with clay and water to enhance its binding properties. The mixture is then compacted around a pattern, which is a replica of the final product. Patterns can be made from various materials, including metal, wood, or plastic, depending on the complexity and the number of casts required.
Once the mold is formed, the pattern is removed, leaving a cavity in the sand that exacts the shape of the desired metal piece. In some cases, two or more halves of the mold are created, allowing for more intricate designs. After the pattern is removed, the mold is ready for the next step pouring in the molten metal.
The metal, often aluminum, iron, or bronze, is heated to its melting point and carefully poured into the mold cavity. As the molten metal flows into the shape, it fills all the detailed features left by the pattern. After a cooling period, the metal solidifies, and the mold is broken away, revealing the finished product. This can require additional processes such as cleaning, grinding, and machining to achieve the desired surface finish and dimensions.
Advantages of Sand Casting
sand caste
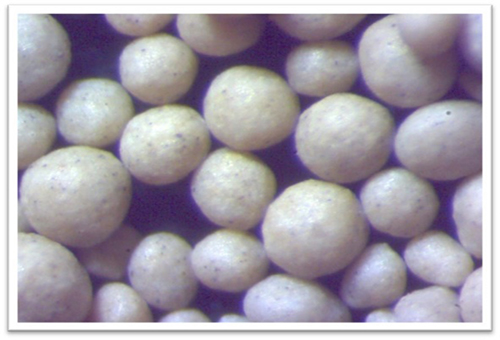
One of the key advantages of sand casting is its ability to produce large and complex geometries that would be difficult or impossible to achieve through other forms of casting or manufacturing. The flexibility of sand molds allows for the recreation of intricate designs, making it suitable for a wide range of applications in industries such as automotive, aerospace, and art.
Furthermore, sand casting is a relatively low-cost process, as the raw materials are inexpensive and widely available. The tools and equipment required for sand casting, such as the molds and furnaces, can be constructed at a lower investment than other casting methods, such as die casting or investment casting. Additionally, the sand used in the process can be reused multiple times, which further reduces material costs and waste.
Challenges and Considerations
Despite its many advantages, sand casting also presents some challenges. The quality of the final product can be affected by factors such as the type of sand used, the moisture content of the mixture, and the pouring temperature of the metal. Furthermore, the sand casting process can produce defects such as sand inclusions, air pockets, and surface imperfections that may require additional processing to correct.
Maintaining quality control throughout the casting process is crucial to ensure that the final products meet the required specifications. This can involve thorough testing of the sand mixture, regular inspections of the molds, and monitoring the pouring process to minimize defects.
Conclusion
In conclusion, sand casting remains a fundamental and valuable technique in the manufacturing industry. Its ability to create complex shapes at a relatively low cost makes it a go-to choice for various applications. As technology advances, so too does the sand casting process, with innovations aimed at improving quality, efficiency, and sustainability. Despite the challenges it poses, the art and science of sand casting continue to thrive, illustrating the balance between tradition and modernity in manufacturing practices.
Post time:نوفمبر . 24, 2024 16:25
Next:foundry sand specifications