The Art and Process of Sand Casting
Sand casting is one of the oldest and most versatile metal casting processes known to mankind. Its roots trace back thousands of years, serving as a cornerstone in the fabrication of metal components across various industries. Whether for artistic purposes or industrial applications, the sand casting technique remains a fundamental method that combines simplicity and efficiency.
At its core, sand casting involves creating a mold from a mixture of sand and a binding agent, typically clay or resin. This mold is then used to shape molten metal into the desired form. The primary material for sand casting is silica sand, which has the right properties to withstand high temperatures and can be easily shaped to create intricate designs.
The process begins with the creation of a pattern, which is essentially a replica of the part to be cast. The pattern can be made from various materials, including wood, plastic, or metal, depending on the intricacy and size of the final product. The pattern is then placed in compacted sand to form a mold, with the sand particles adhering to one another thanks to the binder. Once the mold is formed, it is removed from the pattern and prepared for the pouring of molten metal.
One of the significant benefits of sand casting is its flexibility in producing complex geometries
. Designers can create detailed shapes that might be difficult or impossible to achieve through other methods. Additionally, sand molds can be reused multiple times, making them cost-effective for high-volume production runs. Each casting process typically requires a new sand mold, but innovations in the binding agents have led to more durable molds that can withstand repeated use.sand cast
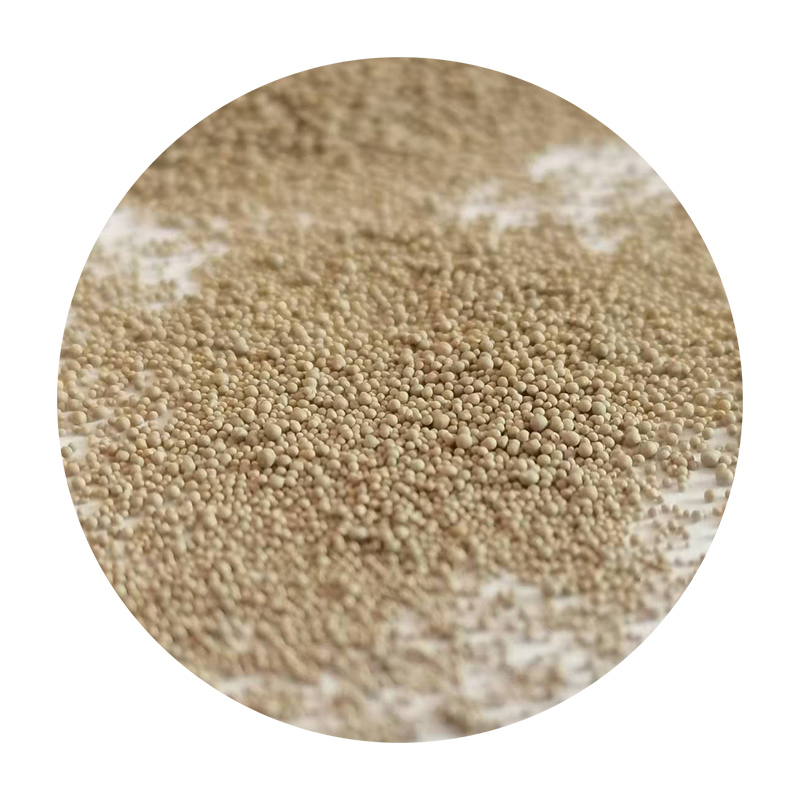
Another advantage of sand casting is the ability to cast a wide range of materials. While ferrous metals like iron and steel dominate the sand casting landscape, non-ferrous metals, including aluminum, bronze, and magnesium, are also commonly cast using this method. This versatility allows manufacturers to choose materials that best suit their application, whether for strength, weight, or corrosion resistance.
Despite its advantages, sand casting is not without its challenges. Surface finish and dimensional accuracy are often lower compared to other casting methods such as investment casting or die casting. The inherent nature of sand allows for slight variations, which can lead to imperfections. To mitigate these issues, manufacturers often apply secondary processes, such as machining or sandblasting, to improve the surface finish and achieve precise dimensions.
Environmental considerations have also come to the forefront of the sand casting industry. The traditional sand casting process can produce waste due to sand loss and the need for binders. However, advancements in technology are promoting more sustainable practices. For instance, some operations have started recycling sand and utilizing eco-friendly binding agents to minimize their ecological footprint.
In conclusion, sand casting is a vital process that marks the intersection of tradition and innovation in metalworking. Its ability to accommodate a wide array of designs and materials, coupled with advancements aimed at reducing waste and improving quality, ensures that sand casting will continue to be a relevant and essential technique in both artisanal and industrial contexts. As technology continues to evolve, so too will the practices surrounding sand casting, promising exciting possibilities for the future of manufacturing.
Post time:سبتمبر . 25, 2024 17:09
Next:sand casting technique