Types of Sand Used in Sand Casting
Sand casting is one of the oldest and most versatile manufacturing processes, allowing for the production of complex metal parts. This technique relies heavily on the type of sand used in the mold-making process. The quality and properties of the sand can significantly influence the final product's characteristics, including its strength, surface finish, and accuracy. Different types of sand are employed in sand casting, each offering unique benefits tailored to specific casting needs.
1. Silica Sand
Silica sand is the most common type of sand used in sand casting. It consists predominantly of silicon dioxide (SiO2), making it an ideal choice for high-temperature applications. Its grains are angular, which enhances the mold strength. Silica sand can withstand high temperatures, making it suitable for casting ferrous and non-ferrous metals alike. Additionally, it has good permeability, allowing gases to escape during the solidification of metal, thereby reducing defects such as blowholes and inclusions. However, it can be prone to thermal shock, which is a consideration in high-speed production settings.
2. Resin-Bonded Sand
Resin-bonded sand is another popular choice in foundries. This type of sand is treated with a thermosetting resin binder, which gives it greater strength and durability compared to traditional silica sand. The resulting molds can withstand higher temperatures and provide finer surface finishes on cast products. Resin-bonded sands are particularly advantageous for complex geometries and intricate designs. However, they may require more meticulous preparation and be more costly than natural sands.
sand casting sand types
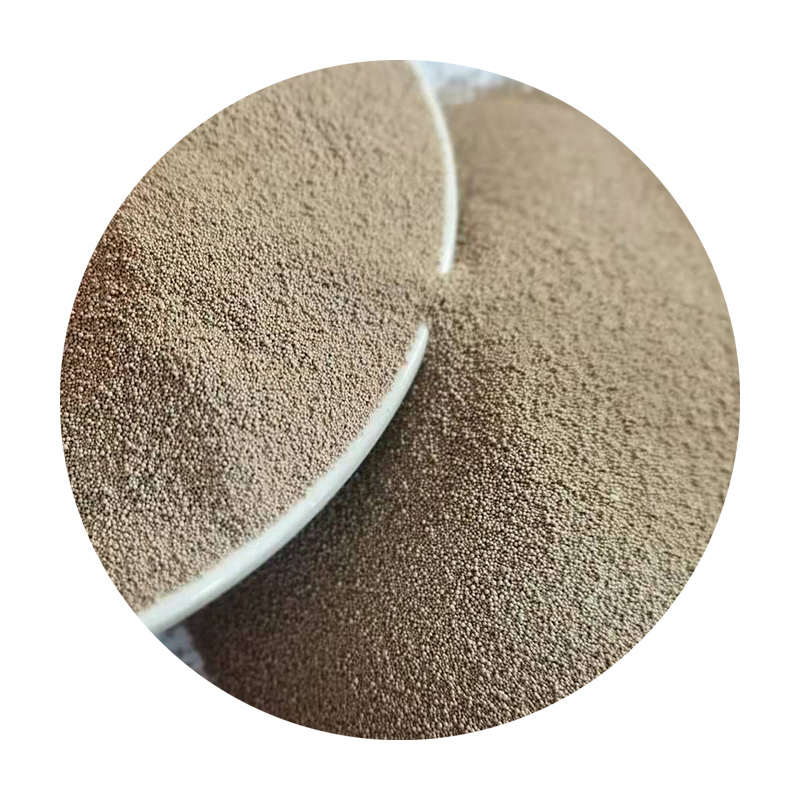
3. Green Sand
Green sand is a mixture of silica sand, clay, and moisture, commonly found in foundries due to its ease of use and cost-effectiveness. This type of sand is called green because it is used in a wet state, allowing for the mold to be formed and then immediately filled with molten metal. Green sand offers excellent flexibility in molding, making it suitable for a wide range of casting applications. Its relatively low cost and reusability make it an industry favorite, although it might not produce the same level of detail or surface finish as resin-bonded sand.
4. Sodium Bentonite Sand
Sodium bentonite sand, known for its exceptional binding properties, is primarily used in foundries for bonding agents. This type of sand can absorb significant amounts of water, creating a robust mold that can withstand high temperatures. The plasticity of sodium bentonite makes it an excellent choice for intricate designs, lending itself to the production of high-quality castings with fewer defects.
Conclusion
Choosing the right type of sand for sand casting is crucial for achieving desired casting characteristics. Silica sand offers high-temperature resistance, while resin-bonded sand provides superior finishing and strength for complex shapes. Green sand remains a cost-effective option for general use, while sodium bentonite sand enhances mold strength and versatility. Understanding the properties of these sands allows foundries to optimize their casting processes, resulting in high-quality final products tailored to specific applications.
Post time:سبتمبر . 03, 2024 21:37
Next:sanding ceramic mug