Sand Casting Foundries An Overview
Sand casting is one of the oldest and most versatile manufacturing processes used for producing metal parts. It involves pouring molten metal into a sand mold that forms the shape of the desired component. This age-old technique has evolved significantly over the years, and today, sand casting foundries leverage advanced technologies to enhance efficiency, precision, and product quality.
The Basics of Sand Casting
The sand casting process begins with the creation of a pattern, which is a replica of the final product. Patterns can be made from a variety of materials, including wood, metal, or plastic, depending on the complexity of the design and production volume. Once the pattern is ready, it is used to form a mold by packing sand around it. The sand mixture typically contains silica sand, a binder (such as clay), and water to help maintain shape and stability.
After the mold is created and the pattern removed, it is ready for the pouring of molten metal. The choice of metal varies; common materials include aluminum, iron, and bronze. Once the metal solidifies, the sand mold is broken apart to retrieve the cast part. This process can be repeated multiple times, making it an efficient choice for both small and large production runs.
Advantages of Sand Casting
One of the primary advantages of sand casting is its ability to create complex shapes that would be difficult or impossible to achieve with other methods. The flexibility of sand molds allows for intricate designs, including internal features and undercuts. Moreover, sand casting is suitable for a wide range of metals and alloys, making it applicable to various industries, including automotive, aerospace, and construction.
Another significant benefit is cost-effectiveness. The materials required for sand casting are relatively inexpensive, and the equipment needed for the process can be simpler compared to other casting methods. This makes sand casting an attractive option for small businesses and startups looking to produce metal parts without substantial investment.
sand casting foundries
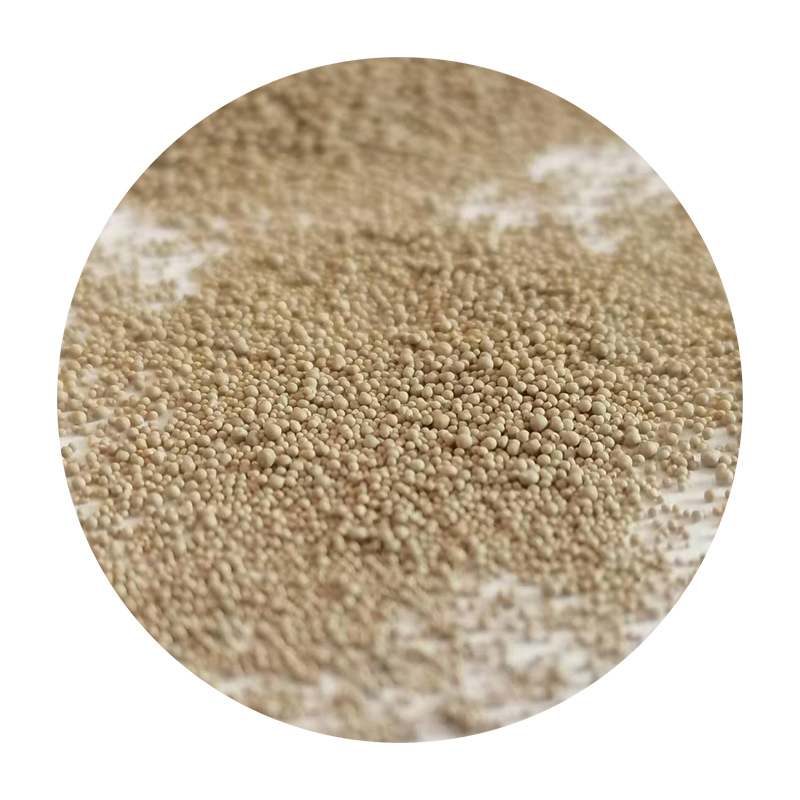
Modern Advances in Sand Casting Foundries
In recent years, sand casting foundries have embraced automation and digital technologies to optimize their operations. Computer-aided design (CAD) software allows engineers to design patterns with high precision, reducing errors and improving turnaround times. The integration of 3D printing technologies has also transformed the production of patterns and cores, allowing for rapid prototyping and shorter lead times.
Moreover, advancements in mold materials and additives have improved mold durability and reduced the occurrence of defects in the final castings. Foundries are utilizing more sophisticated sand mixtures that enhance mold strength and thermal stability, leading to better quality casts.
Environmental Considerations
As the industry evolves, environmental concerns have prompted foundries to adopt sustainable practices. Recycling spent sand and implementing waste reduction techniques are becoming standard practices to minimize the environmental impact of sand casting. Many foundries are investing in cleaner technologies that reduce emissions during the metal pouring process, aligning with global initiatives for sustainability.
Conclusion
Sand casting foundries play a vital role in modern manufacturing. With their unique ability to produce complex shapes and their adaptability to different materials, they continue to be a preferred choice for metal casting. As technology progresses, these foundries are poised to enhance efficiency while embracing sustainability, ensuring their relevance in the ever-evolving industrial landscape. The blend of tradition and innovation keeps sand casting at the forefront of metalworking processes into the future.
Post time:سبتمبر . 04, 2024 05:35
Next:what materials are used in sand casting