Molding Sand for Metal Casting An Essential Component in Foundry Operations
Molding sand is an integral material in the world of metal casting, playing a pivotal role in shaping the final product. Choosing the right type of molding sand can significantly influence the quality of the casting, the efficiency of the production process, and the overall cost-effectiveness of metal casting operations. In this article, we will explore the types of molding sand, its properties, and its significance in metal casting.
Types of Molding Sand
Molding sand can be classified into several categories based on its composition and intended application. The most common types include
1. Green Sand This is the most widely used molding sand, composed of silica sand, clay, water, and various additives. Green sand is renowned for its excellent molding characteristics, ease of use, and cost-effectiveness. Its name derives from the fact that it is used in a moist state, which allows for easy molding and shaping.
2. Dry Sand Unlike green sand, dry sand is heated to remove moisture, making it harder and more rigid. This type of sand is often utilized for producing intricate shapes and finer details in castings. However, dry sand is generally more expensive and requires more detailed handling.
3. Oil Bonded Sand This type of molding sand uses oil-based binders instead of water, which creates a stronger mold. Oil-bonded sand is particularly useful for high-temperature applications and can withstand higher molten metal pouring temperatures. Consequently, it's common in the casting of ferrous and nonferrous metals.
4. Shell Sand This is a special type of sand that involves a process where the sand is coated with a resin binder, creating a shell-like mold. Shell sand molds are known for their precision and detail. They are primarily used in high-production environments due to their quick setting times and superb surface finish.
Properties of Molding Sand
The effectiveness of molding sand is influenced by several key properties
molding sand for metal casting
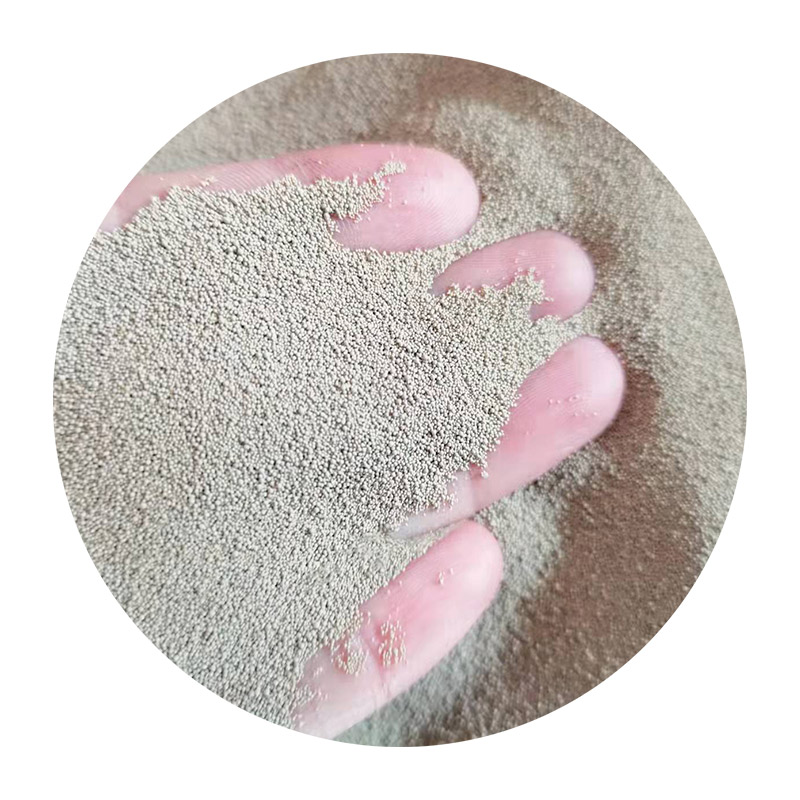
- Grain Size The size of the sand grains affects the mold's strength, permeability, and the intricacy of the casting detail. Fine grains provide a smoother surface finish, while coarser grains can enhance strength but may lose resolution.
- Plasticity This property determines how well the sand can be molded and shaped
. High plasticity ensures that the mold can hold intricate details, while low plasticity can lead to breakage and loss of shape under metal pouring.- Permeability Permeability refers to the ability of the sand to allow gases generated during the pouring of molten metal to escape. Proper permeability is crucial to prevent defects in the casting, such as gas holes and blowholes.
- Moisture Content The correct level of moisture in green sand is essential for optimal molding. Too much moisture can weaken the mold, while too little can lead to cracking.
Significance in Metal Casting
Molding sand serves multiple functions in metal casting. Firstly, it provides the necessary shape and dimension for the metal being cast. The mold's detailed impressions allow for the production of complex geometries, crucial in industries like automotive and aerospace where precision is paramount.
Moreover, the thermal properties of molding sand can influence the cooling rate of the molten metal, affecting the microstructure and mechanical properties of the final casting. A well-designed molding sand can aid in achieving the desired material characteristics, whether toughness, strength, or ductility.
Additionally, the utilization of molding sand is pivotal for cost efficiency. By optimizing the type and mixture of molding sand, foundries can reduce waste, minimize defects, and enhance production rates, directly impacting profitability.
Conclusion
In conclusion, molding sand is a fundamental aspect of the metal casting process, with various types tailored to meet specific needs and properties that dictate performance. Understanding these elements allows foundries to select the appropriate molding sand for their applications, ensuring high-quality castings that meet industry standards. As manufacturing processes evolve, the role of molding sand will continue to be critical, driving innovations and improvements in the metal casting sector.
Post time:ديسمبر . 02, 2024 05:46
Next:sand casting suppliers