Lost Foam Casting Coating An Overview
Lost foam casting (LFC) is a highly efficient and innovative metal casting process that is gaining popularity in various industrial applications. This method involves creating a foam pattern that is coated with a ceramic material, which ultimately helps to produce high-quality metal parts with intricate shapes. In this article, we will explore the essential aspects of lost foam casting coatings, their types, benefits, and applications.
The foundation of the lost foam casting process is the foam pattern, typically made from polystyrene or other similar materials. This pattern is shaped according to the desired final product. Once the foam pattern is created, it is coated with a layer of refractory ceramic material. This coating plays a crucial role in the casting process, as it insulates the foam and withstands the intense heat from the molten metal.
Coatings used in lost foam casting are typically composed of a mixture of silica, alumina, and other binding agents. The primary function of these coatings is to provide thermal insulation and enhance the surface finish of the final metal part. The thickness, composition, and application method of the coating can significantly influence the quality of the final product. Different types of coatings, such as water-based, solvent-based, and colloidal silica formulations, offer various advantages in terms of ease of application, drying time, and overall performance.
One of the key benefits of lost foam casting coatings is their ability to produce intricate designs with excellent dimensional accuracy. The foam pattern can be created with intricate geometric shapes that traditional casting methods may struggle to reproduce. Additionally, the smooth surface finish achieved through the ceramic coating minimizes the need for extensive post-processing, resulting in reduced manufacturing costs and time.
lost foam casting coating
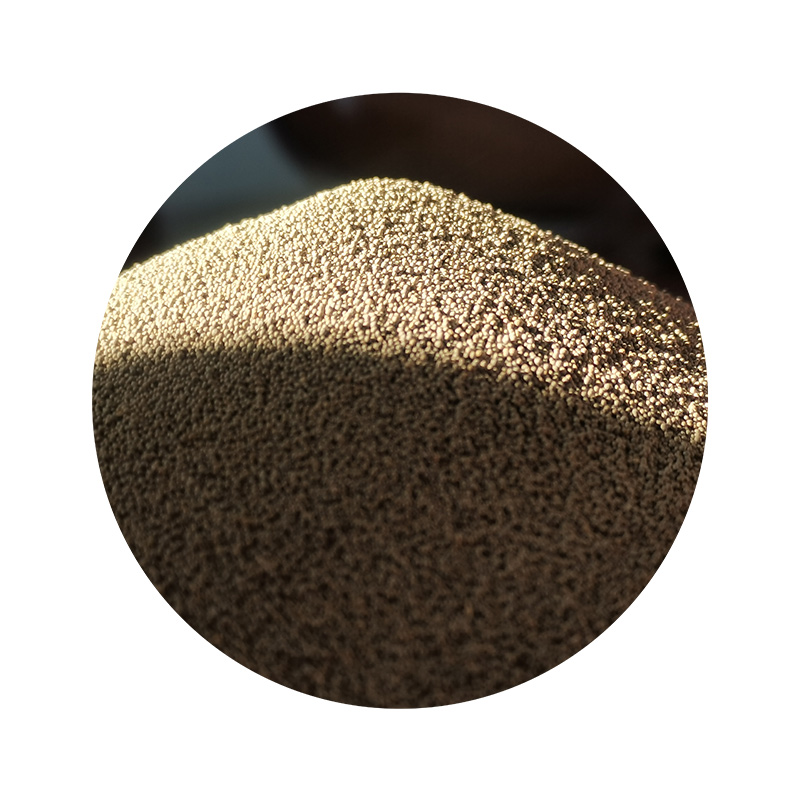
Another advantage of lost foam casting coatings is their thermal stability. The refractory materials used in the coatings can withstand the high temperatures of molten metal, ensuring that the foam pattern does not combust before the metal is poured. This quality allows for a wide range of metals, including aluminum, iron, and steel, to be cast using this method, making it versatile for various industrial applications.
Furthermore, the lost foam casting process reduces the environmental impact associated with traditional casting methods. Since the foam patterns are often made from polystyrene, which can be easily recycled, and the process generates minimal waste, it presents a more sustainable alternative. The elimination of sand molds not only reduces the amount of material waste but also decreases the energy consumption typically associated with mold production and disposal.
The applications of lost foam casting coatings are vast. Industries ranging from automotive to aerospace and industrial machinery employ this method to produce lightweight, high-strength components. The ability to create complex shapes with precision makes it particularly appealing in sectors where performance and efficiency are paramount.
In conclusion, lost foam casting coatings play a vital role in the efficiency and effectiveness of the casting process. Their unique properties contribute to the production of high-quality, intricate metal parts while minimizing waste and environmental impact. As this technology continues to evolve, the potential for lost foam casting to revolutionize metal manufacturing processes remains significant, paving the way for innovation across various industries.
Post time:سبتمبر . 19, 2024 13:47
Next:materials used for sand casting