The Process and Significance of Iron Sand Casting
Iron sand casting has emerged as an essential process in the manufacturing industry, particularly in the production of various metal components. This technique utilizes iron sand, a natural mineral composed primarily of iron oxide, as the primary raw material. The versatility and efficiency of iron sand casting have made it a popular choice for a variety of applications, from automotive parts to intricate artistic designs. This article explores the process of iron sand casting, its advantages, and its applications in modern manufacturing.
The Process of Iron Sand Casting
The iron sand casting process begins with the extraction and preparation of iron sand. Once collected, the iron sand undergoes a series of treatments to eliminate impurities and ensure uniform particle size. This step is crucial, as any inconsistencies in the raw material can lead to defects in the final cast product.
The prepared iron sand is then mixed with a bonding agent, typically clay or resin, to enhance its cohesiveness. This mixture is packed tightly into a mold, which is often made from metal or sand. Once the mold is formed, it is subjected to heat to dry and harden the mixture, creating a solid casting mold.
Next, molten iron is produced by heating iron ore in a furnace until it reaches a liquid state. This molten iron is then carefully poured into the mold, where it fills the cavities created by the mold design. After allowing sufficient time for the iron to cool and solidify, the mold is removed to reveal the cast component.
The final stage involves cleaning and finishing the cast product. This usually includes sanding, machining, and sometimes heat treatment to enhance the properties of the iron. The result is a durable, high-quality component that meets specific design requirements.
Advantages of Iron Sand Casting
Iron sand casting offers several advantages over other manufacturing methods. Firstly, the use of iron sand allows for cost-effective production due to the abundance and lower cost of the raw material. Unlike traditional iron casting methods that may require more expensive alloying materials, iron sand provides a sustainable and economical alternative.
iron sand casting
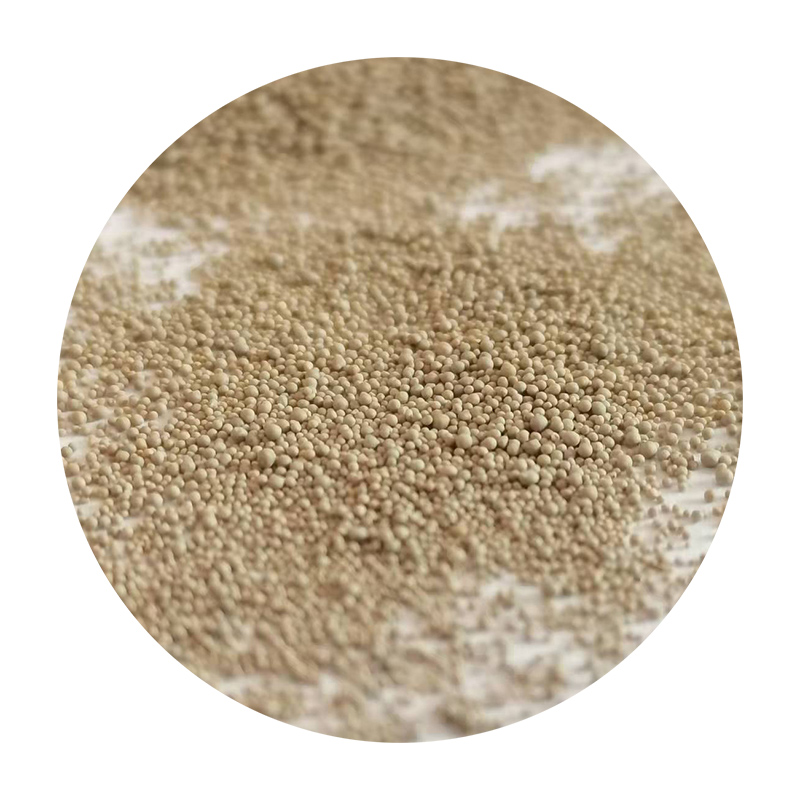
Moreover, the casting process enables the production of complex shapes and designs that may be challenging to achieve with other manufacturing techniques. The flexibility of mold design allows for high customization, making iron sand casting an ideal option for both mass production and small-scale projects.
Another benefit is the excellent mechanical properties of the final products. Iron sand castings display high tensile strength, durability, and resistance to wear, making them suitable for various applications in demanding environments. This inherent strength ensures that components manufactured through this process can withstand heavy loads and stress over time.
Applications of Iron Sand Casting
The applications of iron sand casting are vast and diverse. In the automotive industry, this technique is utilized to produce critical components such as engine blocks, transmission cases, and brake systems. The strength and durability of iron sand castings make them ideal for parts that endure high levels of stress and heat.
Additionally, iron sand casting is widely employed in the construction industry for making fittings, fixtures, and structural components. Its ability to create intricate designs allows architects and engineers to fabricate customized solutions that meet specific project requirements.
Beyond industrial applications, iron sand casting also finds its place in artistic endeavors. Sculptors and artists utilize this technique to create detailed sculptures and decorative pieces, showcasing the aesthetic potential of cast iron.
Conclusion
Iron sand casting is a significant manufacturing process that combines efficiency, cost-effectiveness, and adaptability. It leverages the natural properties of iron sand to produce high-quality, durable components used across numerous industries. As technology continues to evolve, the future of iron sand casting looks promising, with advancements aimed at enhancing its efficiency and applicability, ensuring that it remains a vital part of modern manufacturing practices. The continued exploration and innovation in this field can lead to even more creative and sustainable uses of iron sand casting, reinforcing its importance in the industry.
Post time:ديسمبر . 11, 2024 00:38
Next:Understanding Sand Casting Tolerances and Their Impact on Manufacturing Quality