The Process of Sand Casting
Sand casting is one of the oldest and most widely used methods of casting metals, offering several advantages such as flexibility, the ability to create complex shapes, and relatively low costs. This article will explore the steps involved in the sand casting process, illustrating its significance in metal fabrication.
Step 1 Creating the Pattern
The first step in sand casting is to create a pattern, which is a replica of the object to be cast. Patterns can be made from a variety of materials, including wood, metal, or plastic, and they are usually slightly larger than the final product to accommodate for shrinkage during cooling. There are two main types of patterns solid patterns and split patterns. Solid patterns are single pieces, while split patterns consist of two halves that are joined together. The choice of pattern type largely depends on the design and complexity of the final object.
Step 2 Making the Mold
Once the pattern is ready, the next step is to make the mold. This is achieved by packing sand around the pattern. The sand used in sand casting is typically mixed with a binder, such as clay, to enhance its cohesiveness. The mold consists of two halves the cope (the upper part) and the drag (the lower part). The pattern is placed in a mold box, and the sand mixture is packed around it. After the sand has thoroughly encapsulated the pattern, the mold is then removed from the box, and the pattern is taken out, leaving a cavity that represents the shape of the final object.
Step 3 Filling the Mold
After the mold has been formed and the pattern removed, it’s time to fill the cavity with molten metal. The metal is heated in a furnace until it reaches its melting point and then poured into the mold through a pouring cup. The molten metal flows into any small channels and sections created by the pattern, filling the entire cavity. It’s important to control the pouring process to avoid turbulence, which can lead to defects in the finished casting.
how sand casting is done
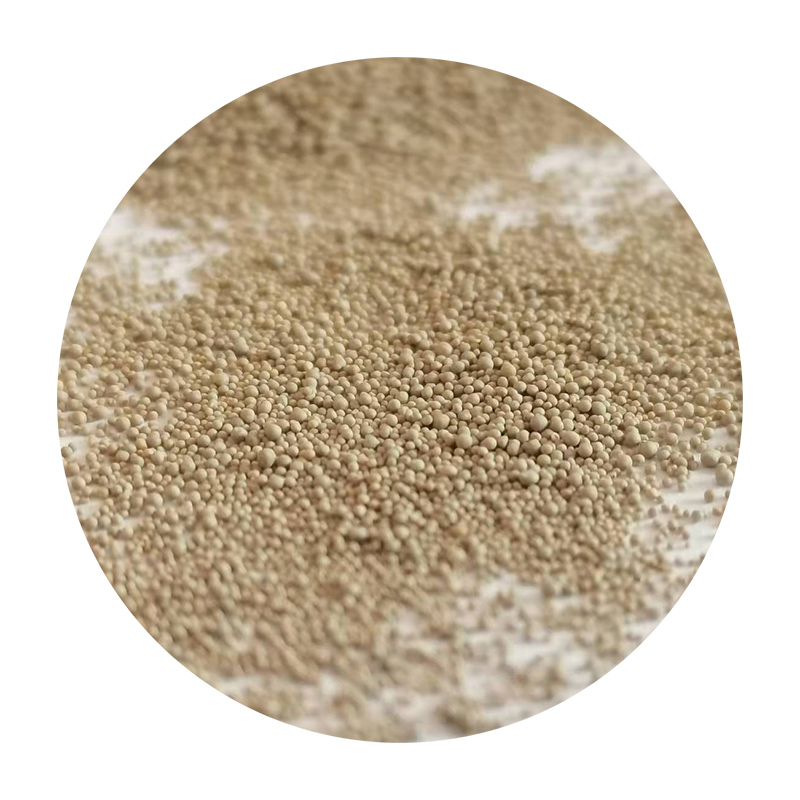
Step 4 Cooling and Solidification
Once the mold is filled, the molten metal is left to cool and solidify. The cooling time depends on the size and thickness of the casting, as well as the type of metal used. Typically, larger castings require more time to cool completely. As the metal solidifies, it shrinks slightly, which is why allowances must be considered during the pattern-making stage to account for any potential cracking or warping.
Step 5 Removing the Casting
After the casting has cooled sufficiently, it is removed from the mold. This process involves breaking away the sand to extract the solid metal object. Depending on the complexity and size of the casting, this can be done manually or with the assistance of machines. Any remaining sand is cleaned off, leaving the newly formed metal part ready for further processing.
Step 6 Finishing Operations
Once the casting is removed, it often requires several finishing processes to meet the specifications required for its application. Common finishing operations include sanding, grinding, and machining to achieve precise dimensions and smooth surfaces. Additionally, any excess material, known as flash or gates, that was created during the pouring process is trimmed away. Sometimes, castings may undergo heat treatment to improve their mechanical properties or coatings to enhance corrosion resistance.
Conclusion
Sand casting remains a crucial method in metalworking, due to its ability to create detailed shapes and structures that other methods may struggle to produce. The entire process, from pattern creation to the finishing touches, showcases the skill and precision required in this age-old craft. Whether in automotive manufacturing, aerospace applications, or artistic metalwork, sand casting continues to be a versatile option that resonates in various industries.
Post time:نوفمبر . 06, 2024 21:30
Next:g2 super sand