What is Sand Casting in Engineering?
Sand casting, one of the oldest and most versatile metal casting processes, has played a fundamental role in engineering and manufacturing for centuries. This method involves creating a mold from sand, into which molten metal is poured to form various components. The advantages of sand casting include its ability to produce complex shapes, its cost-effectiveness for small production runs, and its suitability for a wide range of metals.
What is Sand Casting in Engineering?
One of the primary benefits of sand casting is its flexibility in producing complex geometries. Engineers can create intricate designs that would be challenging or impossible with other manufacturing techniques. This is particularly advantageous in industries such as automotive, aerospace, and industrial machinery, where components often have complex shapes and sizes. Additionally, sand casting can accommodate a variety of metals, including aluminum, iron, and copper alloys, making it suitable for many applications.
what is sand casting in engineering
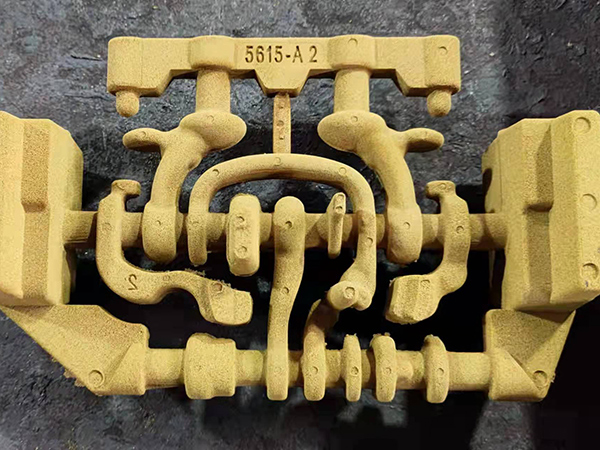
The sand used in sand casting must possess specific properties to ensure the mold holds its shape while allowing the molten metal to flow freely. The most commonly used sand is silica sand, which is chosen for its high melting point and thermal stability. To enhance its performance, additives such as clay are mixed in; this helps in binding the sand grains together and improves the mold's strength.
Once the mold is prepared, the molten metal is poured into the cavity created by the sand mold. Care must be taken during this phase to maintain the correct temperature and pouring speed to avoid defects in the final product, such as cold shuts or voids. After the metal has cooled and solidified, the mold is broken away, revealing the cast part.
While sand casting offers numerous benefits, it is not without limitations. The surface finish of sand cast parts is generally rougher than that of parts made by other methods such as die casting or investment casting. Additional finishing processes might be required to achieve the desired surface quality. Moreover, the dimensional accuracy of sand cast components can be less precise, which may necessitate further machining for critical applications.
In conclusion, sand casting remains an essential technique in the field of engineering and manufacturing. Its versatility, cost-effectiveness, and capability to create complex shapes makes it a popular choice for producing a wide range of components. As industries continue to evolve and demand more intricate designs and high-quality products, sand casting will likely adapt and thrive alongside new technologies, maintaining its relevance in modern engineering practices. Whether for prototyping, low-volume production, or specialized parts, sand casting offers a dependable and efficient solution that is integral to many sectors of the economy.
Post time:ጥቅም . 01, 2024 05:54
Next:तीन आयामीय मुद्रित बालू ढलान प्रक्रिया में नवाचार रचनाहरू