Materials Used in Sand Casting
Sand casting, also known as sand mold casting, is one of the oldest and most widely used metal casting processes. It involves the use of sand as the primary molding material. This technique is favored for its versatility, cost-effectiveness, and the ability to produce complex shapes. Understanding the materials involved in sand casting can provide insight into why it remains a popular choice in various industries, from automotive to aerospace.
1. Molding Sand
The primary material used in sand casting is molding sand. This sand is typically composed of silica (SiO2), which is abundant and inexpensive. However, not all sand is suitable for casting. The ideal molding sand must possess certain properties it should have a fine grain size, be able to retain moisture, and have high refractoriness to withstand the molten metal temperature without breaking down. The most commonly used type of molding sand is green sand, which consists of silica sand mixed with clay and moisture. The clay acts as a bonding agent, helping the sand particles stick together and enabling the mold to hold its shape.
2. Clay and Additives
While silica sand is the backbone of molding sand, clay is essential for its binding properties. Bentonite clay is frequently used in sand casting due to its excellent bonding and plasticity. This clay allows the mold to maintain its shape and rigidity even under the stress of molten metal. Additionally, various additives, such as organic binders and chemical hardeners, may be included to enhance the properties of the sand mixture, improve its performance, and reduce the emissions during casting.
3. Metal Alloys
what materials are used in sand casting
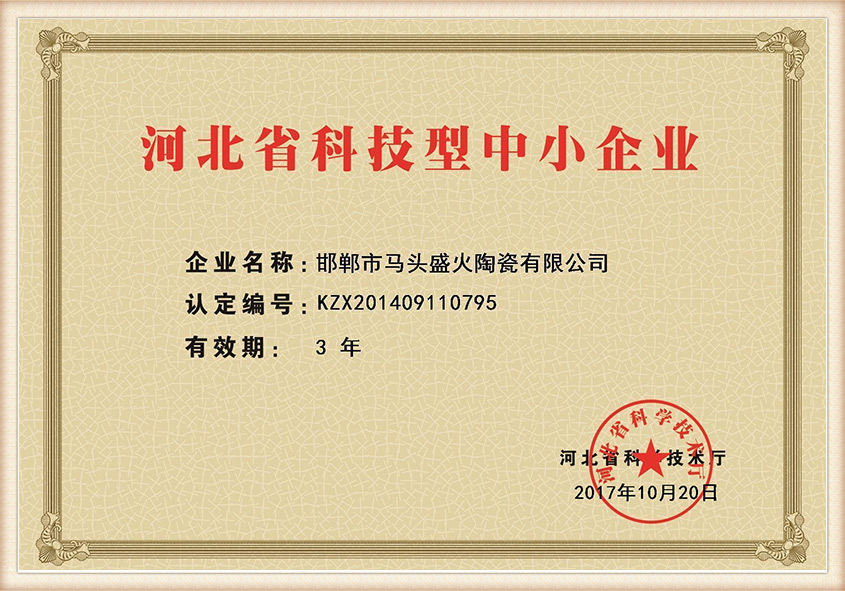
Once the sand mold is prepared, the next essential material is the metal alloy that will be poured into the mold. Sand casting can accommodate a wide range of metals, including ferrous metals like cast iron and steel, as well as non-ferrous metals such as aluminum, bronze, and brass. The properties of metal alloys can vary significantly, influencing the characteristics of the final cast product, such as strength, ductility, and corrosion resistance.
In cases where hollow sections or internal features are needed in the casting, cores made from additional materials are introduced into the mold. These cores are typically made from sand or other compounds, which can be bonded together using similar clays or chemical agents. The core material must be able to withstand the molten metal's heat and maintain its integrity during the casting process.
5. Refractory Coatings
To enhance the quality of the cast surface and prevent sand from adhering to the metal, refractory coatings are often applied to the interior of molds or cores. These coatings are usually composed of fine silica and other minerals that can withstand high temperatures and help achieve smoother finishes on the final product.
Conclusion
In conclusion, the materials used in sand casting play a critical role in determining the quality and characteristics of the final products. From the choice of silica sand and clay to the selection of metal alloys and core materials, each component contributes to the effectiveness and efficiency of the casting process. As technology advances, innovations in these materials continue to improve the sand casting process, making it an enduring choice for manufacturers seeking flexibility and capability in their production methods.
Post time:መስከ . 04, 2024 05:01
Next:how to sand cast